How Manufacturers Can Become Data Champions
Today’s manufacturing companies have a great strategic opportunity: the chance to use advanced data gathering and analytics to drive productivity, improve customer experience, and foster societal and environmental benefits. Those that embrace the opportunity are turning their supply chains into hyperconnected value networks for sharing data across company boundaries and collaboratively managing the flow of goods around the world.
One catalyst for this change is uncertainty in the economy and the world at large brought on by megatrends such as rising global temperatures and COVID-19. Increasingly, business leaders see the innovative use of data as a stabilizing force in their industries. The benefits include increased productivity, improved quality, reduced environmental impact, and more effective innovation. (See Exhibit 1.)
Although interest in such advanced methods is high, many companies do not yet have the technological or organizational enablers in place to achieve data excellence. In a BCG survey conducted in 2019, 72% of manufacturing executives said that they considered advanced analytics to be important. But only 17% said that they had captured satisfactory value from it. (See Exhibit 2.)
A Data Excellence Framework
The January 2021 report published by the World Economic Forum in collaboration with BCG, Data Excellence: Transforming Manufacturing and Supply Systems, introduced a framework to help manufacturers overcome these impediments. This design structure, called the Manufacturing Data Excellence Framework, focuses on the three main challenges that manufacturers say hold back their efforts to implement data and analytics solutions at scale: a lack of data applications, insufficient technology, and organizational hurdles. (See Exhibit 3.)
To meet these challenges, manufacturers have developed and deployed data and analytics applications in various business functions, such as new product launches, engineering, logistics, maintenance, and health and safety. In support of these applications, they have invested in technological enablers—the digital and analytic foundation necessary for capturing data, comprehensively processing and visualizing it, and protecting it from intrusion and cyber theft. They have also introduced organizational enablers—managerial practices and processes related to functions such as legal compliance, skill building, and governance.
Companies can use applications, technological enablers, and organizational enablers to assess their current proficiency in manufacturing data excellence and to develop a plan for further progress. In 2021, ten leading manufacturers aligned with the WEF Platform for Advanced Manufacturing and Value Chains used the framework in exactly this way. Analytics at 18 plants associated with these companies yielded a composite benchmark of the manufacturers’ self-assessments. (See Exhibit 4.)
Stages in the Journey
Our research suggests that the journey toward data excellence comprises three successive stages of digital prowess: actionable insights, predictable outcomes, and self-optimizing systems. (See Exhibit 5.) Each stage features an increased degree of collaboration and data sharing across company boundaries, as well as a higher level of analytic prowess.
Actionable Insights. In the initial stage, companies use operational data to track the performance of current processes and production lines, deriving actionable insights for optimizing production and reducing errors. Sensors in factories and distribution centers, along with core software applications such as enterprise resource planning, gather the data, which is then presented in the form of reports and digital dashboards. Managers use this data to discern patterns and trends and to inform decision making. (See the sidebar “Case Study: The Henkel Company.”)
Case Study: The Henkel Company
Underlying this application is a set of technological enablers gathering data on more than 150 parameters from a wide variety of sources (such as GPS, weather, and traffic indicators), which it then analyzes and processes. A standardized model permits integration with ERP and warehouse management systems, and execution of subsequent activities such as invoicing and claims generation. Henkel has deployed Track & Trace in North America and Europe, covering nearly 75% of the company’s shipments.
Predictable Outcomes. The second stage of the journey involves ensuring predictable outcomes. Machine learning (ML) algorithms receive large sets of operational performance data from historic and real-time sources, which they use to train themselves and to predict the manufacturing system’s future behavior, thereby providing guidance on ways to prevent mishaps and prepare for growth. (See the sidebar, “Case Study: ZF Group.”)
Case Study: ZF Group
The system comes with a strong set of technological enablers, including advanced analytics processing capabilities with ML-based algorithms that analyze continuous streams of video from cameras located in the company’s facilities, as well as graphical, virtual overlays placed in the video feed. Organizational enablers have played a big role, too: ZF collaborated with a startup incubator to refine the solution and adapt it to the manufacturer’s specific needs.
Self-Optimizing Systems. In the third stage of the journey toward data excellence, the applications take autonomous action. Self-learning algorithms get smarter as their experience with historical and real-time data grows. At this stage, companies might develop a digital twin—a simulation of a specific production asset or manufacturing plant. This digital representation can correct and optimize itself in real time, responding to changes in factors such as employee availability and scheduled production assets. Fully digitized plants of this sort often have significantly lower environmental footprints, too, because they can reduce resource consumption or improve efficiency in response to fluctuations in demand. (See the sidebar, “Case Study: Arçelik.”)
Case Study: Arçelik
The Internet of Things (IoT) is a key technological enabler for this solution. More than 400 sensors and measurement devices—including energy analyzers, natural gas meters, compressed air flow meters, and calorimeters—are installed throughout the manufacturer’s operations facilities. These instruments send data to the company’s analytic systems.
After piloting the system at a greenfield plant, Arçelik is now rolling it out across the globe. Arçelik’s participation in Horizon 2020, a consortium that includes the European Union, has proven to be an important organizational enabler for kicking off the investment and scaling it across the organization.
Companies that master the use of data, successfully deploying advanced technological and organizational enablers in data applications across their ecosystems, are considered data champions. They generate consistently high scores on measures of productivity and customer experience, as well as of society and the environment.
Accelerating Progress
Almost all manufacturing companies have started their journey toward data excellence, but so far none have reached the end of the path. Because of the ever-evolving nature of technology and the ongoing introduction of new practices, companies must continuously innovate and improve. To accelerate this process, the Manufacturing Data Excellence Framework, along with BCG’s Digital Acceleration Index (DAI) survey, can help companies make progress.
The framework and the DAI survey provide a solid understanding of a company’s current status. Decision makers can also use them to compare their results to peer-group or industry benchmarks, and thus set transformation and growth priorities.
Companies should then develop or obtain the specific applications they need to raise their degree of mastery, either at a local (facility-based) level or at a global (company-wide) level. They can also set up community-style interactions among collaborative organizations, learning from one another’s best practices and innovating together. These are critical steps to take in moving toward a shared goal of manufacturing data excellence—a world of globally connected business ecosystems that continually improve their performance, their environmental record, and the value of what they produce.
Meet the Project Advisors
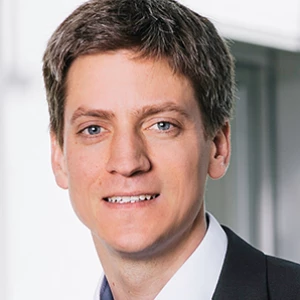
Related Project Content
Download the full report
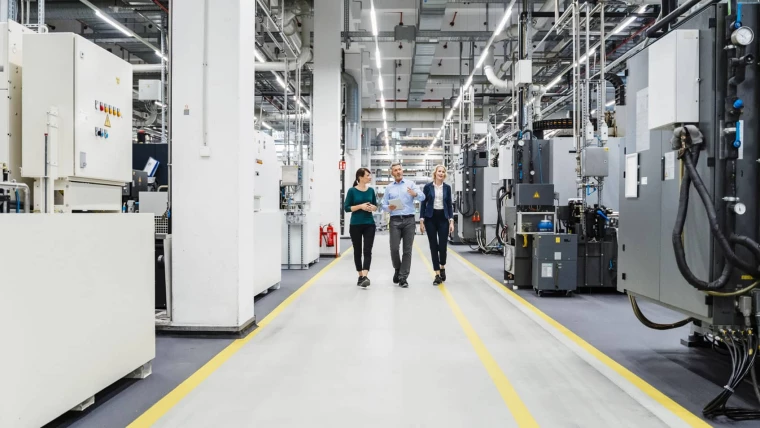
About Unlocking Value in Manufacturing
For more information, please visit https://www.weforum.org/projects/data-sharing-for-manufacturing.