If the world is to come close to achieving its climate goals, there’s no escaping the fact that we must not only pump less carbon dioxide into the atmosphere—we’ll also have to take CO2 out. Indeed, the more we exceed the target of limiting global warming to 1.5o C by 2050, the greater this challenge will become.
This hard reality is driving impressive progress in direct air capture (DAC) technologies, which are among the surest means of permanently capturing and storing CO2. It’s also why this emerging technology should be on the radar of pretty much any company that is serious about achieving net-zero emissions.
Unlike conventional carbon-capture technology, which removes CO2 directly from a source—such as a power plant or factory smokestack—DAC extracts it from the air. DAC is evolving, but the basic chemical processes have been used in industry for many decades, and startups around the world already operate modest DAC facilities. Both the market signals and revenue models are in place to make it a commercial reality.
The challenges now mainly involve engineering: We need much greater scale and efficiency to bring down the cost and dramatically expand deployment. The conventional estimate is that up to 10 billion tons of CO2 will have to be removed from the atmosphere by 2050, compared with the few thousand tons being removed now.
We believe that DAC will be an important part of virtually every company’s comprehensive decarbonization strategy.
We believe that DAC will be an important part of virtually every company’s comprehensive decarbonization strategy. As regulatory deadlines for specific products or target dates for reaching net-zero commitments approach, most companies will find they can get only so far by directly reducing their own emissions, such as by shifting to renewable energy or using lower-carbon materials. They’ll also have to find ways to offset so-called Scope 3 emissions at a reasonable cost. These emissions are beyond most companies’ direct control because they’re embedded in value chains throughout their products’ life cycles. Service companies, whose greenhouse-gas footprints mainly stem from hard-to-cut things like air travel or heat for offices, will have a particularly strong need for offsets.
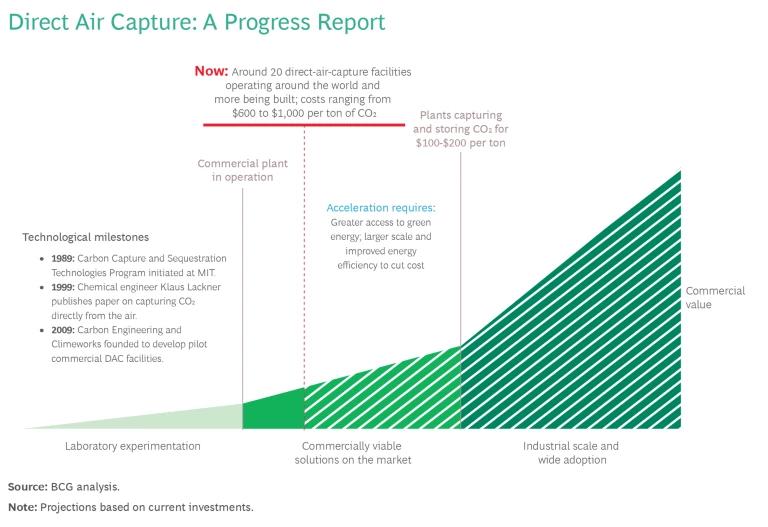
Signing long-term contracts with DAC providers to store and capture CO2 on their behalf will be not only the most cost-effective solution but also the most compelling: carbon removal will be verifiable, permanent, and won’t result in “leakage”—emissions that are eliminated in place only to arise somewhere else.
How DAC Works
The most common DAC method is to build what essentially are large fans that blow air over or through a “sorbent”—a solid membrane or liquid that naturally binds with molecules. Through heat and a series of chemical processes, which vary by company, the CO2 is released and refined into a pure concentrated gas that is either stored in the ground or used as a commercial feedstock for a variety of applications. Although CO2 is dispersed in the air in miniscule amounts—around 420 parts per million—DAC plants now in operation are capable of capturing several thousand tons over the course of the year.
Startups are deploying this basic approach in various ways. One of the most established DAC companies, Canada’s Carbon Engineering, recently acquired by Occidental Petroleum, took a process long used by cement manufacturers that uses calcium oxide to absorb CO2 and then convert it into calcium carbonate. Climeworks, another industry leader, is building DAC facilities in which airstreams circulate over physical membranes that absorb CO2. The filters are then heated so that the CO2 can be removed and processed. On the other end of the spectrum are companies like CarbonCapture, based in Los Angeles, which builds super-modular structures that use a range of sorbents—some chemical, some physical.
For DAC to hit its inflection point, we estimate that the cost needs to drop to around $200 per ton or lower.
A big problem, though, is cost. Right now, depending on the maturity of the technology and machines being used, it costs anywhere from $600 to $1,000 to remove CO2 from the atmosphere and store it. Only certain companies are willing to pay that much. For DAC to hit its inflection point, we estimate that the cost needs to drop to around $200 per ton or lower. That would be comparable to the cost of other solid-waste disposal methods in high-income countries, a goal we think is possible as companies go down the technology learning curve. Some companies pioneering more novel DAC technologies believe they can get the cost down to $100.
Overcoming the Obstacles to Scaling Up
Scaling up requires overcoming some real practical barriers. DAC facilities currently require tremendous amounts of energy to power air-circulation systems and provide the heat needed for chemical processes. And that energy needs to be renewable; otherwise, you’d have to keep recapturing and processing emissions.
What’s more, to amortize the cost of all the equipment, you’d need to run these facilities at around 90% of capacity. If your plant runs entirely on solar power, which is available only when the sun shines, it may only operate at 20% capacity. That would dramatically increase costs.
One way to address the energy problem is to locate DAC facilities close to where renewable resources are abundant.
One way to address the energy problem is to locate DAC facilities close to where renewable resources are abundant. Climeworks, for example, has projects in Iceland, which has cheap geothermal energy 24 hours a day, although that approach isn’t scalable. DAC facilities could also locate in “energy islands”—regions with tremendous renewable energy resources that aren’t yet tapped because there isn’t enough local demand. Take Western Australia, which is lightly populated and has tremendous solar resources, pretty good wind resources, and, in some places, good geothermal. Land is also abundant. You could operate carbon capture facilities there closer to around the clock.
It will also be critical to improve energy efficiency. Much of the current innovation in DAC is about minimizing the energy needed to run processes. A lot of research is also going into new sorbents and membranes, for example. Some startups are exploring metal organic frameworks, a highly porous material that absorbs gas molecules. Yet other companies are studying the use of algae and other biological methods to trap and store CO2.
Granted, there are still naysayers who contend DAC is too far away from being practical and cost-effective enough to make a real difference. We believe otherwise. The remaining challenges to widespread adoption are straightforward, and the realities of global warming will only increase the motivation of innovators, investors, and energy consumers to remain on the path to solving them.
Alex Dewar made important contributions to this article.