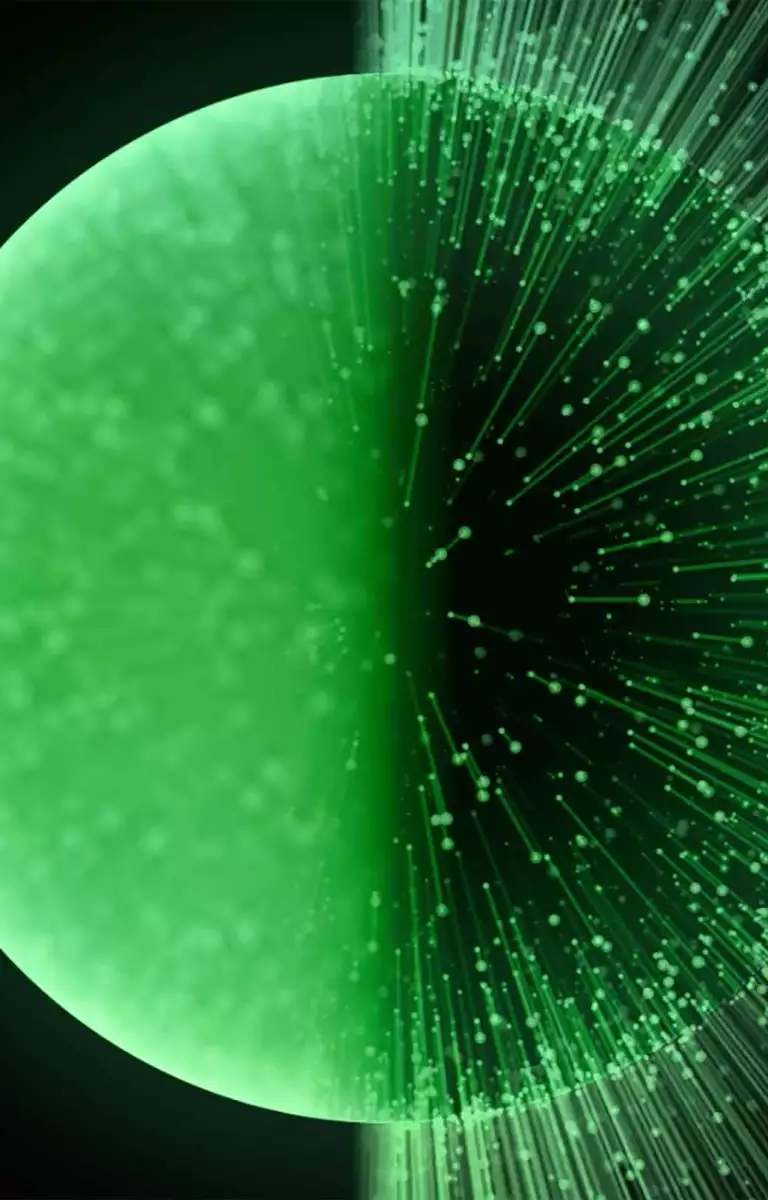
BCG SPOTLIGHT
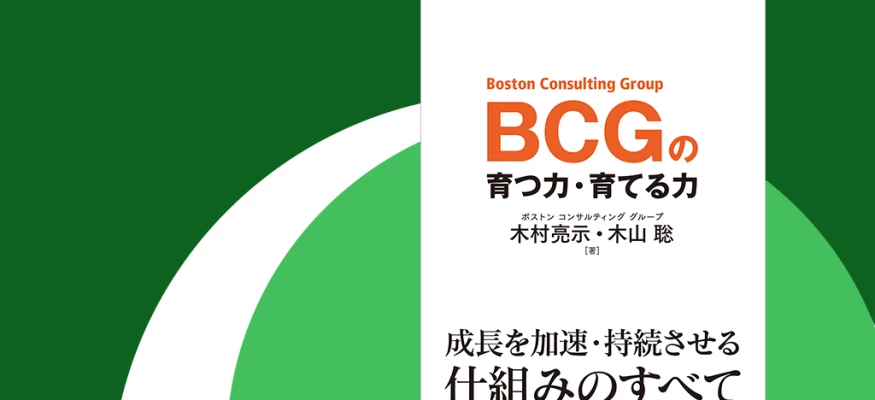
BCGの育つ力・育てる力
→ 2015年に刊行されロングセラーとなっている『BCGの特訓』の増補改訂版。「育つ側」「育てる側」の双方の視点で、人材開発のソフトな側面についてBCG社内で実践している取り組みを、広範な業界やビジネスパーソンの参考にしていただけるよう紹介しています。
詳細はこちら
その他おすすめコンテンツ
1 /
7
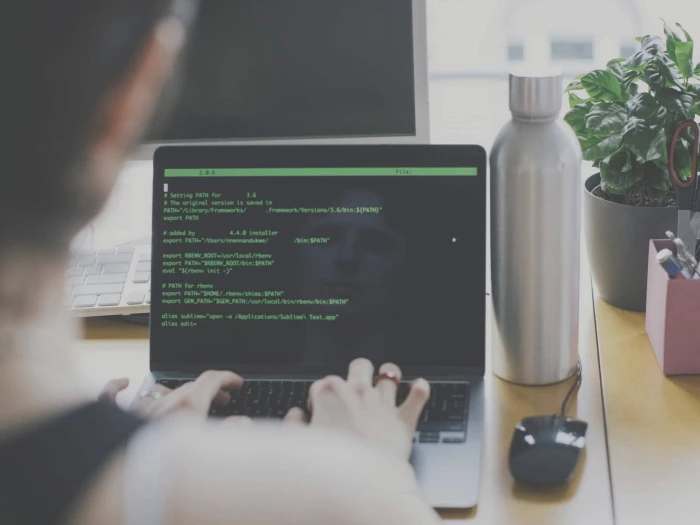
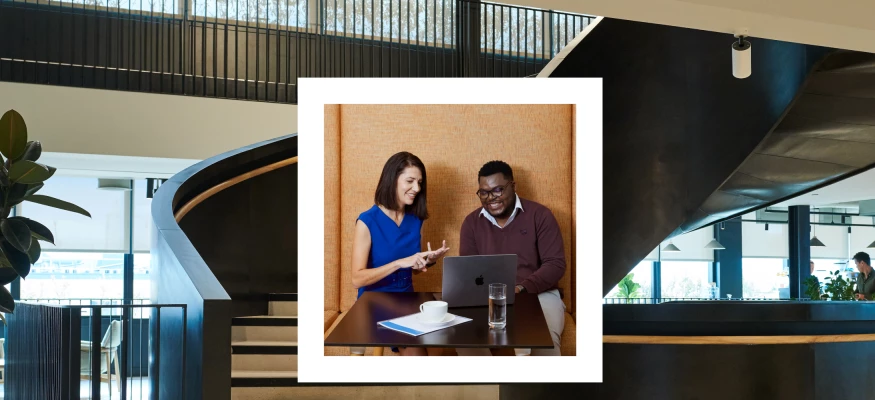