Key to the fight against global warming are the many technologies, old and new, that can help abate the emission of greenhouse gases (GHGs) across every industry. According to our analysis, existing technologies can address about 45% of the 51 gigatons of CO2 equivalent (CO2e) GHGs emitted annually around the world.
The remaining 55% must be mitigated in large part through implementation of new green technologies—approaches that range from low-carbon hydrogen and biofuels to carbon capture, utilization, and storage (CCUS).
If these technologies are to play an essential role in mitigating GHG emissions and helping countries meet their Paris Agreement goal of limiting global warming to well below 2° Celsius above preindustrial levels and pursue efforts to further limit the temperature increase to 1.5°C, they must achieve mass industrialization two to four times faster than did earlier green technologies such as solar photovoltaic and onshore wind.
Two challenges stand in the way of achieving these results. The first is the need to reduce what Bill Gates in his book How to Avoid a Climate Disaster termed the green premium: the added cost of low-carbon technologies compared with technologies based on fossil fuels—synthetic aviation fuels versus traditional petroleum-based jet fuel, for example. Already, countries with favorable green energy costs and subsidy schemes have significantly reduced the green premium, due in large part to the surge in energy prices as the COVID-19 pandemic subsides and the war in Ukraine roils energy markets. Recent favorable policies such as the US’s Inflation Reduction Act and the recently adopted reforms of the EU’s Emissions Trading System are likely to enable other markets to reach green parity sooner than previously expected.
This amplifies the importance of shifting the focus to the second challenge: scaling up green technologies for mass industrialization within the limited time that remains. Doing so will require an unprecedented effort to overcome six major hurdles, from developing mass manufacturing processes to fully integrating them into end markets. Besides reducing the threat of climate disaster, succeeding at this endeavor will unlock business opportunities worth up to $25 trillion between now and 2040 for the companies involved.
In our view, only by assembling entire ecosystems of complementary organizations—including incumbent industry players, green tech startups, industry associations, educational institutions, and public bodies—can the global community overcome the remaining hurdles and enable critical green technologies to deliver their full potential to mitigate GHGs.
The Industrialization Imperative
The math is simple: the green technologies now being scaled up around the world—including renewable energy generated by solar and wind, heat optimization and recovery, electrical efficiency, operations optimization, and natural carbon sequestration—have the potential to reduce only about 23 gigatons of CO2e per year—45% of the 51 gigatons of CO2e currently being released into the atmosphere every year. To reach net zero goals, countries must eliminate or offset the remaining 28 gigatons of CO2e per year.
This will require changes in both energy consumption and energy production. On the consumption side, this entails reducing demand for the fossil fuels that drive GHG emissions. On the production side, it involves developing and bringing to market eight categories of new green technologies: low-carbon hydrogen and synfuels, bioenergy, carbon removal, CCUS, energy storage, green building technologies, distributed energy, and green factory technologies.
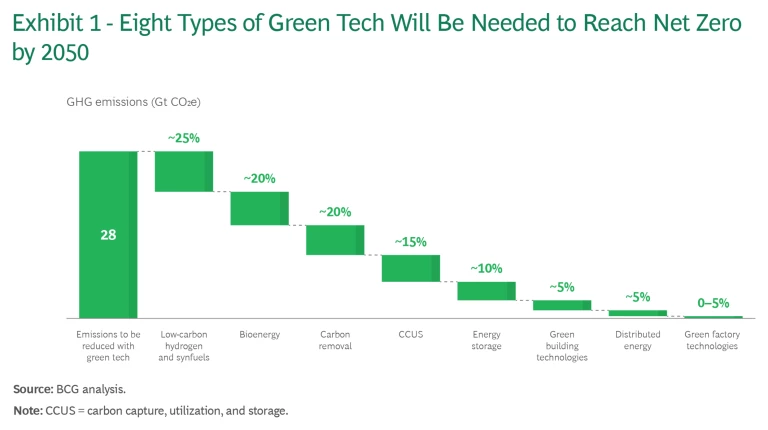
Each of these technology categories holds considerable promise for carbon reduction. For example, low-carbon hydrogen, when fully adopted, has the potential to reduce around 25% of the total gap through a range of applications, including heavy road transport, mining equipment, aviation, and steel. (See Exhibit 1.) These applications are at different stages of maturity, but none of them are mature enough to support mass industrialization. Bioenergy and green building technology, for example, have already reached the early adoption stage, while carbon removal and most green factory technologies are still at the prototype stage. (See Exhibit 2.)
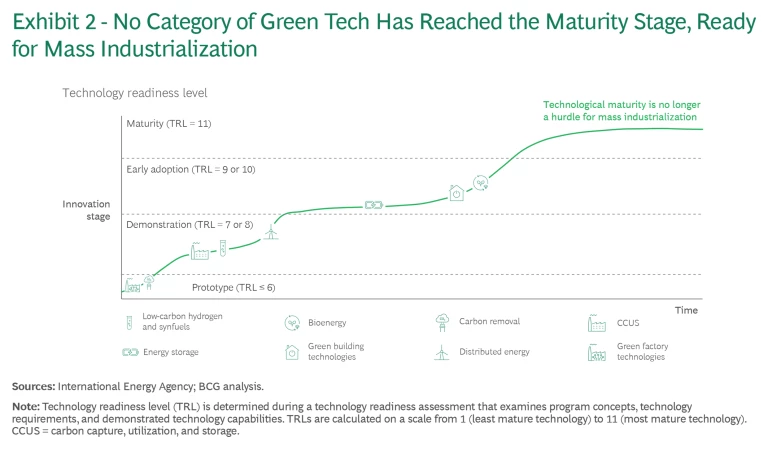
The path to mass industrialization will be rough, especially for the least mature technologies. If these technologies are to play a meaningful role in reducing GHG emissions by 2030, they must be scaled up to achieve capacity levels far greater than they currently possess. And they must reach those capacity levels and be brought to market within the next three to seven years—a time interval two to four times shorter than the ones previous green technologies required.
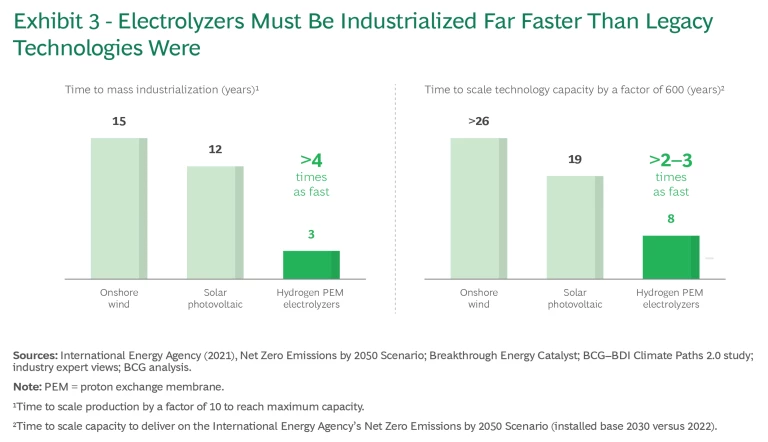
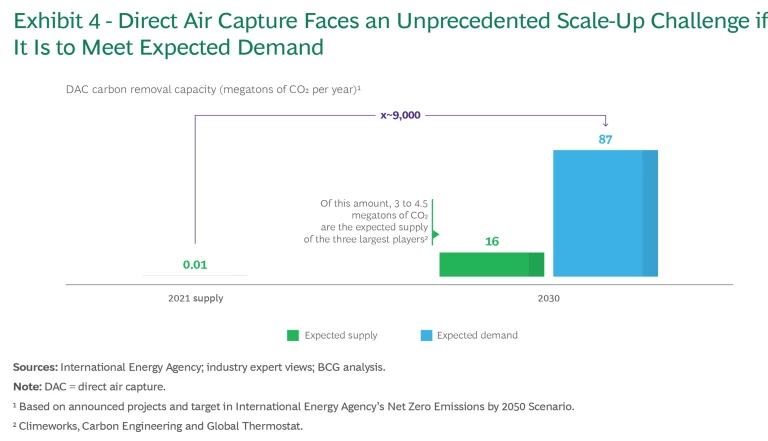
As an example, consider electrolyzers, which are essential for producing the low-carbon hydrogen needed as an input in refining, fertilizers, iron and steel manufacturing, as a feedstock for the fuel cells and synfuels needed to transform the transport sector, and elsewhere. If this technology is to contribute significantly to meeting the Paris Agreement targets, it must achieve mass industrialization within the next three years—more than four times as fast as the time needed to bring solar power to market. And by 2030 it must expand its hydrogen production capacity to an amount 600 times greater than its current level. (See Exhibit 3.) By comparison, solar power took 19 years to achieve that level of increased capacity, and onshore wind took more than 26 years.
Direct air capture (DAC) technology—a method of capturing CO2 directly from the atmosphere and then storing or using it in industrial processes—presents an even greater challenge. DAC has the potential to massively reduce the quantity of GHGs already present in the atmosphere. According to the International Energy Agency, DAC must be ready to capture about 87 megatons of CO2 every year by 2030, and 983 megatons by 2050, to meet global carbon abatement goals. But DAC is still in its infancy, and reaching the projected figures would require scaling deployment over today’s levels by a factor of about 9,000 by 2030. (See Exhibit 4.) Even factoring in the commitments that the largest DAC players have made, the effort would fall short by roughly 70 megatons. So to reach the goal, DAC must be industrialized at five times the pace currently anticipated.
What stands in the way of mass production and market acceptance of these new technologies? And how can countries reduce mass industrialization enough to slow the rate of global warming?
The Journey to Industrialization
The critical green technologies must clear six key hurdles in order to achieve industrialization at scale (see Exhibit 5):
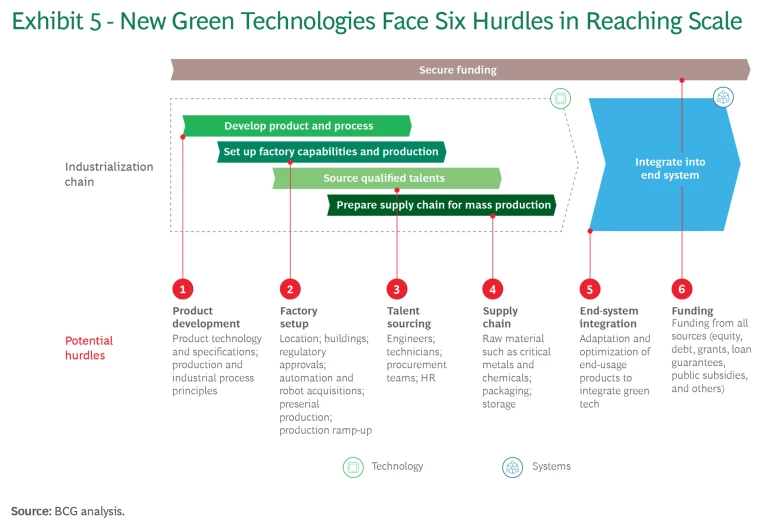
- Product and Process Development. Planners must ensure that the technology is ready for industrialization and that the manufacturing specifications and industrial processes needed are ready for production at scale. At this stage, they should determine the production objectives and carry out product tests.
- Factory Setup. Essential infrastructure, regulatory approvals, and manufacturing equipment and tools—including automation and robotics tools—must be secured. As production begins and ramps up, quality checks must be carried out.
- Talent Sourcing. Ensuring access to participating engineers, technicians, and procurement teams is critical, as is having an effective human resources function.
- Supply Chain. Companies must source and secure regular access to the required raw materials, components, packaging, and storage facilities, and must implement the supply chain systems needed to ensure their timely delivery.
- Integration into End Systems. Planners must determine how to integrate each green technology into final products and uses—for transport, buildings, industrial processes and the like—including any adaptations needed to ensure demand for the technology. They must also obtain the appropriate regulatory approvals.
- Funding. Participants must secure the capital—including equity funding, loans, and public subsidies—necessary to initiate and complete the industrialization of each green technology.
For an example of the specific industrialization challenges that must be overcome, consider hydrogen proton exchange membrane (PEM) fuel cells. While the technology underlying PEM fuel cells is almost ready for mass production, automating the labor-intensive production process remains to be worked out, and production capacity will continue to be limited until it is resolved. Challenges also persist in recruiting qualified process and electrical engineers, and electrochemists. The supply chain, especially for the metals—including iridium and platinum—needed to make the membrane electrode assembly must be strengthened. And matching specific fuel cells to the requirements of the end products in which they will be used remains uncertain, complicating efforts to predict the shape of future cell demand.
The Ecosystem Alternative
Under ordinary circumstances, the industrialization process would occur sequentially, beginning with launching the product development process, setting up production facilities, and initiating the commercialization process.
Yet if companies adopt this approach to industrializing innovative green technologies, they will have no chance of reaching their net-zero goals. For example, it typically takes up to five years to bring a single factory for producing PEM electrolyzers into operation; so to reach capacity goals, the mass industrialization process would have to have begun two to three years ago.
In short, the green tech revolution must begin now and achieve mass industrialization as soon as possible. The only way to accomplish this is through parallelization—that is, by simultaneously building the multiple factories needed, finding the talent to run them, setting up the supply chains to provide source materials for them, and working with end users to identify and meet customer demand. No single organization—no matter how vertically integrated across the value chain—can overcome all of the hurdles standing in the way of mass-producing any of these technologies within the required timeframe.
Quickly scaling up to mass production will require establishing ecosystems of companies and economic stakeholders that provide essential capabilities and supplies to the task of bringing a specific technology to market. Such ecosystems can take full advantage of the high degree of modularity that these new technologies possess, enabling different stakeholders to manufacture the many separate parts needed and to overcome different hurdles impeding full industrialization. They also permit strong coordination and oversight of the process, coordinating stakeholders along the value chain in the effort to stimulate demand from end users by enabling green tech manufacturers to work directly with end users to resolve “chicken or egg” problems that threaten to increase industrialization risk. Joint ventures between auto companies and electric-vehicle battery makers, for example, match OEMs’ needs at a particular scale with battery makers’ ability to optimize product development and the manufacturing supply chain.
Setting up the many factories needed will necessitate collaboration by product developers, manufacturing process engineers and tool designers, and even government regulators and real estate developers. Creating a secure and resilient supply chain will entail working closely with potential suppliers and with providers of supply chain software. The process of integrating the new technologies with end users must begin early, through partnerships for the codesign of the final product and the use of such tools as digital twins. And securing the capital needed to fund the industrialization effort must begin early, too, through the combined efforts of all players in the ecosystem, potentially leveraging public subsidies as well. Coinvestment schemes can lower the investment burden and generate the necessary funds more quickly, as they did in the case of South Korea’s HyNet, a network of hydrogen refueling stations funded by a consortium that includes Hyundai, KoGas, Air Liquide, Nel, and several other local companies.
Each ecosystem must include, in addition to the technology’s manufacturer, various complementors and suppliers and catalysts and an orchestrator. Complementors include providers of manufacturing machinery and technology, suppliers of green tech raw materials and components, providers of initial product research and personnel training programs, and companies that plan to use the green tech in their own products.
Suppliers and catalysts include companies that provide the technology and software needed to make the product—including AI , data-sharing platforms, and collective simulation and digital twin software—to other partners in the ecosystem to ensure that they cooperate seamlessly, and organizations that promote the green tech and provide funding.
The orchestrator federates and connects the other members, driving the ecosystem toward its common goal and helping attract the upfront investment needed for the effort. The success of the ecosystem depends heavily on the quality of the orchestrator, which must be fully acceptable to all other players in the ecosystem. Criteria for choosing a successful orchestrator include whether it will play a significant role in the technology’s development and industrialization, sit at the center of the ecosystem blueprint, benefit significantly from the ecosystem’s success, and appeal to other participants as a fair and neutral player, with a track record of past success and a strong reputation.
In the case of hydrogen PEM fuel cells, the necessary ecosystem would include seven key complementors in addition to the fuel cell manufacturers themselves. Codesign efforts must engage both the OEMs of the propulsion systems that use the fuel cells—which might also serve as orchestrator—and the manufacturers of end products such as heavy and off-highway vehicles and trains. Automotive suppliers could share best practices for factory-level productivity; industrial automation providers could collaborate on developing robots to automate production; and the new process should be tested in a pilot factory. Educational bodies and research centers would be enlisted to create dedicated schools or programs to train the necessary talent. And mining, refinery, and recycling companies could partner to supply the needed raw materials and components and to manage the recycling of end-of-life vehicles and fuel cells. (See Exhibit 6.)
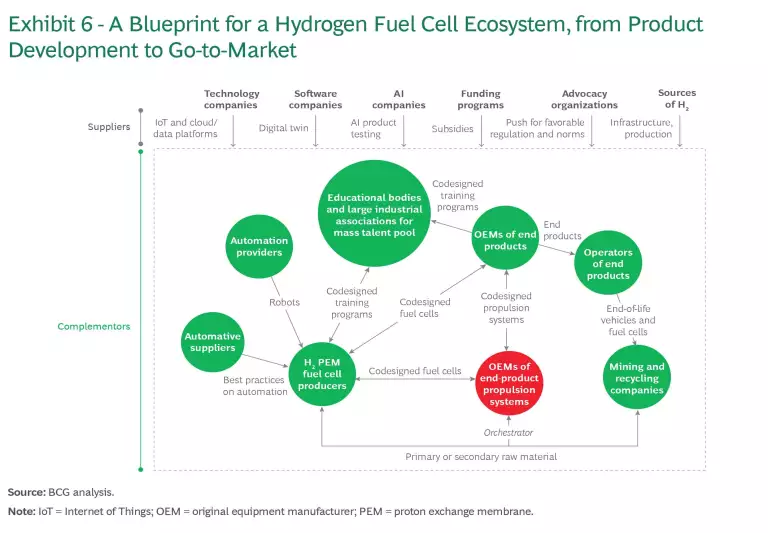
Like any other green tech ecosystem, the hydrogen PEM fuel cell network requires a number of key suppliers. Providers of data sharing platforms, collective simulation software, digital twins, and other cutting-edge technologies are essential to support the collaboration process. An advocacy team for the technology can promote development of necessary manufacturing and product standards and push for favorable regulation. A second team can oversee efforts to find and develop funding to make the industrialization process a reality. Finally, the ecosystem must source the hydrogen that goes into the fuel cells, including connecting with hydrogen suppliers and the providers of the infrastructure needed to deliver the hydrogen.
Such ecosystems, we believe, are the only viable path to industrializing new green technologies at the speed and scale necessary to limit global warming to 1.5°C. Creating them will also unlock enormous business value—an estimated $25 trillion between now and 2040, according to our estimates, along with an aftermarket worth another $10 trillion. (See “Powering Ecosystems.”)
Powering Ecosystems
In 2019, in an effort to achieve its ambitious 2030 CO2 reduction targets, mining company Anglo American set out to develop a proof-of-concept hydrogen-powered fuel cell and battery power system for ultra-class trucks that would demonstrate a pathway to decarbonizing haulage for the mining industry. No such system existed in the market, and Anglo American did not have all of the internal capabilities needed to design it and to create the infrastructure for the necessary supply of hydrogen, so Anglo American assembled a complete ecosystem of companies to develop an onsite green hydrogen solution and carry out the pilot project.
Anglo American’s primary partner, First Mode, a global carbon reduction company founded in Seattle, handled the initial design, build, and testing of the system, including the software needed to manage it. Acting as co-orchestrators, Anglo American and First Mode brought in additional suppliers to support the retrofit power module, including off-the-shelf components for fuel cells, batteries, and onboard hydrogen storage tanks.
A key challenge proved to be ensuring a regular onsite supply of green hydrogen for the truck, which Anglo American and First Mode overcame by collaborating with Engie to install the electrolyzers and fueling systems needed for the proof-of-concept at the mine site. An onsite solar photovoltaic system provides renewable electricity for a 3.5 megawatt electrolyzer that can produce up to 1 ton per day of hydrogen. There is also a 350 bar refueling system with 800 kilograms of onsite hydrogen storage.
Critical to the project’s success was the high level of cooperation that the co-orchestrators maintained during the design and piloting stages of the project. “Our innovative operating model changed the contracting ecosystem,” said Julian Soles, now CEO of First Mode and former head of technology development, mining, and sustainability at Anglo American. “This allowed First Mode and Anglo American to develop, demonstrate, and deploy the technology far faster than we could have otherwise.”
Following the successful deployment of the proof of concept in May 2022, Anglo American and First Mode entered a business combination to commercialize the system under the First Mode name. The two companies also entered into a global supply agreement to implement the system across seven Anglo American mines, including retrofitting approximately 400 ultra-class trucks, starting with 40 diesel trucks at the company’s mining operations in South Africa. Its hydrogen-powered trucks are expected to be cost competitive with diesel at most of the selected sites by 2030.
Catalyzing the Team
The ecosystems that will be needed to facilitate rapid industrialization of green tech call for a wide range of players with distinct roles, capabilities, and technical expertise, united on the basis of mutual trust and belief in a common goal. Their operating models will likely demand new ways of working together, sometimes far from traditional practices.
In light of these challenges, every ecosystem will need an independent, external player to develop the initial design, identify required partners and capabilities, and bring them together. To perform the designer role well, an organization should possess three key characteristics.
Subscribe to our Climate Change and Sustainability E-Alert.
First, it should have experience in a range of sectors, contacts in multiple industries, the ability to identify best-in-class stakeholders, a thorough grasp of their reasons for participating, and the ability to maintain the ecosystem’s cohesiveness. Second, it should have experience in facilitating collaboration among multiple stakeholders, building partnerships, and combining the overall effort’s industrial and technological aspects. Third, it should have links to public authorities to help it secure public funding and the capacity to articulate the ecosystem’s value in the context of existing public green tech initiatives.
Successful Ecosystems
Ecosystems have a strong record of producing significant benefits, in terms of both time to market and financial results. For example, by partnering with a range of global automakers and suppliers, VinFast, a Vietnamese carmaker launched in 2017, brought its first car to market in just 24 months, compared to the more typical four years. And according to our research, banks that engage in ecosystems for developing new fintech services achieved annualized total shareholder returns of 8.2% from 2016 to 2021—almost twice that of banks that didn’t. Their net income, too, outperformed their rivals, growing at an annual rate of 9.9% versus 6.3%.
Putting together the right mix of stakeholders is of course necessary to the creation of a successful ecosystem, but it isn’t sufficient. Several additional factors must be taken into account to ensure that the ecosystem achieves its stated goals:
- Clear Purpose. Every member of an ecosystem must fully understand the problem that it is designed to solve, across all six industrialization hurdles, and the value proposition that it offers to each participant. This knowledge must also take into account the anticipated demand for the ecosystem’s products.
- Proper Configuration. All members must agree on a detailed blueprint for all required activities along the entire value chain, the actors involved, their roles, and the links between members.
- Adequate Governance Model. The ecosystem’s governance model must be clear, simple, and consistent over time and across partners. To build trust, it must be fair to all partners, compliant with laws and norms, and unbiased in providing access to data, for example. It must effectively foster collaboration and alignment between participants, encouraging participation in and growth of the ecosystem. And it must be flexible enough to adapt to changing circumstances, such as shifts in the market or the development of relevant new technologies.
- Aligned Contribution and Benefits. The ecosystem must be designed and managed so that members benefit proportionately to their investment in time, money, and expertise. The value-sharing model should encourage active participation in the ecosystem, and the investments required of partners should be proportionate to their capabilities and expected reward.
The absence of any of these factors can severely hamper an ecosystem’s ability to carry out its mission.
No Longer Business as Usual
We firmly believe that creating and sustaining ecosystems for every critical new green technology is a key component of a concerted effort to mitigate the effects of climate change . And time is running out—substantial progress on this front needs to happen now. Getting it done requires rapid and concerted action by every participant, the ability to reinvent how they do business, and a willingness to collaborate with others throughout their respective ecosystems.
Industrial Leaders. Every ecosystem needs a game-changing company to initiate and oversee the ecosystem. To perform this role effectively, it must first identify the technology problem to be solved, the value proposition for the technology’s industrialization, and the differentiating capabilities needed to overcome obstructions and bottlenecks on the path to mass industrialization. These obstructions may involve such things as problems in automating labor-intensive manufacturing activities, difficulty with recruiting qualified engineers and technicians, and the challenge of sourcing the raw materials and components needed to manufacture the technology.
The leading company must then initiate connections with other industrial players and suppliers while clarifying its own role in the ecosystem—whether orchestrator, complementor, core technology provider, or some other role. Once the ecosystem is in place, the leading company must collaborate with the other players to define the ecosystem’s operating model. Finally, it must mobilize all essential nonindustrial actors, including providers of cutting-edge technologies and educational and public bodies that are essential to supporting the ecosystem’s goals.
Providers of Cutting-Edge Digital Technology. The role of these companies—to support collaboration among all players in the ecosystem—is critical, given the potential of their offerings to accelerate the process of green tech industrialization. They should participate in codesigning a customized digital collaboration environment to foster innovation and improve operational efficiency across the ecosystem’s entire value chain. This should encompass day-to-day collaboration tools—including data sharing platforms—to exploit and share data across the ecosystem, digital-twin technology to assess and optimize the performance of the ecosystem’s product once it has been developed, and any other virtual tools needed to improve product efficiency, such as 3D modeling, digital factories, and collective simulation software. It should also identify high-potential AI use cases, such as in product testing.
Industry Associations and Educational Bodies. These players will help define skill catalogues needed throughout the ecosystem, design and implement necessary training programs to promote these skills, identify skills that will be outmoded by the new technology, and provide a path to retraining for workers whose skills are likely to become obsolete.
Public Bodies. Governments will probably have to generate the massive shocks needed to jumpstart the creation of the necessary ecosystems, first by dedicating funding on the scale of the $369 billion devoted to climate change mitigation in the US’s Inflation Reduction Act, and then by building the momentum needed to ensure the willing participation of all players. Public bodies must also, of course, help design and implement schemes for funding ecosystems and promoting their growth, through innovation-enabling regulations and investment mechanisms. And they should take a lead role in educating citizens about the benefits of the new technologies and their industrialization.
But half-measures are inadequate. Governments must advance stringent regulations to phase out fossil fuels and mandate the use of new technologies as soon as these are ready. The EU’s plan to stop production of ICE vehicles by 2035, for example, has caused carmakers, automotive suppliers, and battery manufacturers to focus on ensuring compliance with the new rule.
Bringing to market all of the varieties of innovative green technology needed to meet the international community’s net-zero goals will require massive acceleration of the industrial processes involved in developing, manufacturing, and implementing any new technology. This in turn will require parallelization of each step—from devising the manufacturing processes to building the factories to finding the necessary talent and supplies to integrating the new green tech into end users’ products and processes. The task will likely require an ecosystem of complementors, suppliers and catalysts, and other stakeholders, led by an orchestrator and guided and managed by an external designer experienced in and capable of working with all parties.
Can all of this be accomplished in time to ward off the most extreme impacts of global warming? That depends on the determination of the various players, governments, and society at large to succeed—and on their willingness to start on the path now.