Rail operators are ramping up their procurement of rolling stock to accommodate surging demand. Many of these railway-vehicle acquisitions are supported by capital from government agencies that recognize the importance of modernizing and expanding rail transport to fuel economic growth and achieve climate goals.
Historically, rolling stock acquisition has focused primarily on minimizing initial expenses. But such an emphasis often led to higher operating costs, which already accounted for 70% to 80% of total lifetime costs. Today that tradeoff is unsustainable against the pressure rail operators face to enhance reliability and cost-effectiveness to compete with alternative transport modes.
The value at stake is substantial. One rail operator we worked with saved $5 billion in lifetime costs by employing the TCO model to develop and procure a new high-speed train.
It is time for operators to adopt a total cost of ownership (TCO) model that considers the full range of costs—including maintenance, energy, and administrative expenses—over the lifespan of their rolling stock.
To implement the TCO model, operators should incorporate it in all phases of the asset life cycle: from procurement preparation and supplier negotiations to bid selection, contracting, and fleet performance management. The value at stake is substantial. For example, one rail operator we worked with saved $5 billion in lifetime costs by employing the TCO model to develop and procure a new high-speed train.
Rolling Stock Procurement Is Gaining Steam
The challenges arising from rail transport’s unprecedented growth require rail operators to expand capacity and make better use of infrastructure . New operators are actively procuring fleets of railway vehicles. Asian rail systems, in particular, are expanding rapidly, as exemplified by India’s proposed high-speed rail line. At the same time, established operators are procuring new rail vehicles to replace old equipment, implement new capabilities (such as enhanced efficiency and higher speeds), serve new routes, and offer more frequent service. Operators also seek to introduce environmentally friendly rolling stock into their systems.
Our research indicates that approximately 45% of train procurement projects experience delays.
These objectives, coupled with an influx of capital for rail operators from the public sector, are catalyzing a substantial surge in the procurement of rolling stock. Indeed, DWS Group projected that the total market size for original equipment manufacturers (OEMs) of rolling stock will increase by 60% from 2020 through 2030. Examples of this trend include the following:
- The Federal Transit Administration granted $200 million in public funding to the Chicago Transit Authority for the acquisition of new rolling stock.
- Amtrak ordered rolling stock valued at $7.3 billion from Siemens.
- Deutsche Bahn allocated approximately $2 billion for the procurement of 73 high-speed rolling stock units.
Procuring rolling stock is inherently complex, owing to a variety of technical, financial, regulatory, and logistical factors. In today's landscape, this complexity is compounded as rail operators grapple with acute financial constraints, heightened scrutiny of reliability, and competitive pressure. Our research indicates that approximately 45% of train procurement projects experience delays. More than 30% of all projects have experienced delays exceeding one year, and this figure rises to more than 50% in the high-speed sector. Cost overruns are also common.
Nevertheless, rail operators must excel at rolling stock procurement, given its significant impact on an operator’s long-term cost position. Rolling stock not only constitutes a substantial portion of bound capital but also affects operational performance, such as maintenance expenses, over the train vehicle’s lifespan. Moreover, given heightened expectations around the customer experience, new train cars provide a key enhancement.
TCO Promotes Effective Procurement Practices
Three criteria define an
effective rail procurement process
:
- On-Time Delivery. Considering the large share of procurement projects that experience long delays, it is crucial to ensure that deliveries of railway vehicles are punctual and meet expectations.
- Optimized Total Life-Cycle Costs. Minimizing operating costs, which account for 80% to 90% of the total life-cycle cost of trains, should be a primary focus.
- Flexibility in Customer-Facing Components. The ability to easily update parts that affect the passenger experience, such as signage and seating, helps differentiate individual rail operators and reduces the costs entailed in replacing these items.
Shift away from a traditional working model in which operators provide detailed and prescriptive specifications. Instead, adopt a collaborative model.
To achieve these criteria in the procurement process, especially for highly specialized trains, operators should employ several guiding principles:
- Make the transition from a buyer role to a partnership. Shift away from a traditional working model in which operators provide detailed and prescriptive specifications. Instead, adopt a collaborative model in which operators and OEMs work hand in hand, capitalizing on the OEM’s expertise and the operator’s knowledge of its own capabilities and passenger needs.
- Test innovative train concepts early in the process. Develop digital and physical testing environments that allow for faster design iterations and validation throughout the procurement process. By doing so, key concepts can be evaluated and refined as early as possible.
- Ensure excellence in process management. Establish a clear governance structure that includes representatives from the operator and OEM. This structure should have well-defined decision-making authority to keep the project on schedule and effectively manage cost and time overruns.
The TCO model promotes the successful application of these principles. This approach lays the foundation for fostering a synergistic partnership between an operator and a rolling stock manufacturer. It allows operators to harness their insights into their own infrastructure and passenger requirements to devise robust functional specifications. At the same time, it empowers the OEM to fulfill these specifications in the most cost-effective way possible. Thanks to rapid acceleration in the availability of data, today’s operators can rethink their procurement processes to capture this opportunity.
What Does the TCO Model Encompass?
The TCO model incorporates all major cost categories incurred throughout an asset’s lifespan:
- Initial Acquisition. The upfront purchase cost (including prototypes) and associated infrastructure investments.
- Maintenance and Cleaning. Expenses for scheduled preventative maintenance, inspections, repairs, and cleaning. These costs are affected by the expected component lifetime, component availability, supplier risk, preventative maintenance needs, diagnostic capabilities and needs, and facility equipment cost.
- Energy and Fuel. Costs for energy usage will depend on the use of fuel-efficient rolling stock.
- Personnel. Labor cost is determined by the number of individuals needed to operate the trains, as well as by the required skill levels.
- Administrative. This category covers contract management costs and other fees, such as those for track access.
To facilitate meaningful comparisons across bids and design choices, the TCO model normalizes total costs per lifetime mile and seating capacity, accounting for depreciation and net present value.
Benefiting from the TCO Model
Operators who use TCO to procure rail rolling stock have much to gain, including the following:
The TCO approach, in contrast, sets reliability and cost targets for each system instead of exhaustive technical specifications.
Enhanced Design Flexibility. Traditionally, rail operators have given OEMs excessively detailed design specifications. This approach has escalated costs by forcing OEMs to rely on historical designs rather than applying new, more creative design capabilities. The TCO approach, in contrast, sets reliability and cost targets for each system instead of exhaustive technical specifications. OEMs gain the flexibility to employ their specialized design knowledge (which operators may lack), while still ensuring that the designs fulfill the operator’s objectives. This flexibility promotes reliability and efficiency throughout an asset’s lifespan. (See “Using Modular Design to Improve Cost-Efficiency and Reliability.”)
Using Modular Design to Improve Cost-Efficiency and Reliability
Leveraging the TCO model, the operator and an OEM collaborated to modularize the design of these components. This redesign facilitates rapid replacements when breakdowns occur, paving the way for potential long-term savings and reductions in downtime—all unlikely outcomes had they used a traditional procurement approach.
Transparent Cost Management. M&A activity in the rail supply sector surged by 33% in 2021 and 2022 relative to 2019, particularly among rolling stock OEMs and parts suppliers. Examples include Alstom's acquisition of Bombardier, and Wabtec's purchase of GE Transportation. The consolidation has curtailed competition and made it harder for operators seeking to improve designs and pricing to find points of comparison. By providing additional transparency, TCO gives operators clear guardrails for cost management and facilitates direct comparisons between vendors, even in a market with limited competition.
TCO aligns incentives among operators, OEMs, and suppliers to ensure spare parts availability, quality, and affordability over the long term.
Improved Comparability Among Proposals. Rail operators often face challenges in comparing costs across various proposals due to disparities in specifications—relating to, for example, lifespans, seating capacities, and the number of cars. By normalizing total costs, the TCO model ensures effective comparability across different bids. In addition, when evaluating bids, operators often overlook the extensive range of costs associated with rolling stock maintenance and operation. This includes costs for adapting infrastructure to accommodate different train models, disassembly, overhead, and depreciation. By incorporating all cost elements within a single model, the TCO approach ensures the thorough evaluation of bids and designs. The approach also aids in pinpointing costs that can be influenced by OEMs versus those inherent to operators.
Enhanced Spare Parts Availability. Many suppliers do not maintain spare parts availability throughout their assets’ lifespans, or they develop custom parts that are hard to replace. For example, a major rail operator told us that it needs to manufacture some legacy parts in-house because no suppliers can provide them. TCO aligns incentives among operators, OEMs, and suppliers to ensure spare parts availability, quality (including upgrades and modifications), and affordability over the long term.
Optimized Maintenance Equipment and Practices. During the design and procurement process for rolling stock, suppliers and operators often fail to consider what equipment they will need to test and maintain railcars or what the appropriate maintenance standards and practices should be. This arises from the challenges of coordinating a wide variety of suppliers. Making suppliers responsible for TCO encourages collaboration during the design phase, which helps to ensure that the operator’s maintenance staff has the necessary training and tools before the rolling stock's arrival.
Maintenance processes also become more efficient and adaptable with the TCO model, allowing the operator and suppliers to minimize lifetime cost and downtime. (See Exhibit 1.) Moreover, TCO enables all parties in the process to incorporate new approaches and technology to improve performance over time.
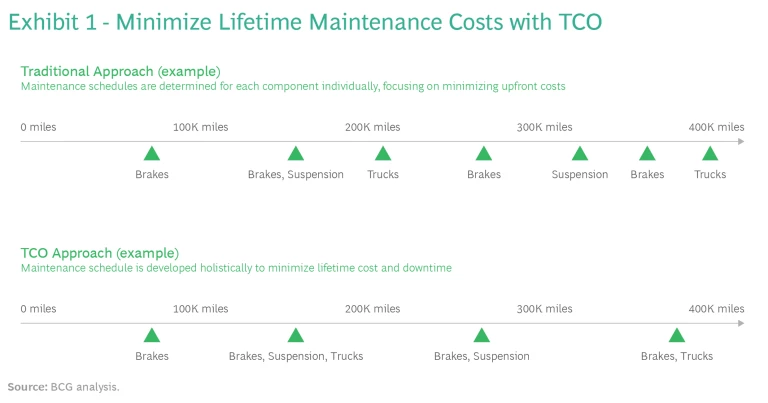
More Effective Strategic Planning. Rail operators experiencing unanticipated maintenance cost overruns for aging assets often must divert resources from discretionary projects at the last minute. The TCO model helps make maintenance costs and requirements (such as facility upgrades) more predictable year over year, especially when incorporated into contracts. This improves an operator’s ability to allocate investments to other areas reliably and consistently.
Developing and Implementing TCO
The TCO model should motivate and support actions before, during, and after procurement. (See Exhibit 2.)
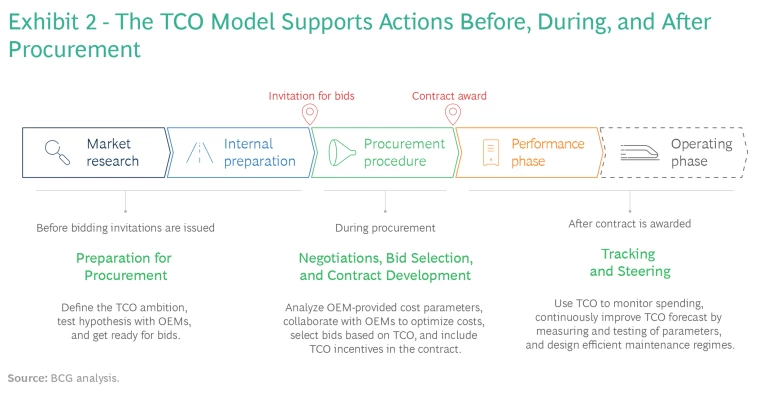
1. Preparation for Procurement. Effective upfront planning and modeling of expected costs across various factors provides the foundation for an effective TCO approach. Begin by defining the TCO objectives and setting specific targets, considering internal planning goals. Formulate hypotheses regarding objectives and validate these with OEMs. Such market exploration provides valuable insights into the feasibility and practicality of the objectives. Once the hypotheses have been tested, prepare for the bidding process by establishing procurement protocols and documentation. This phase also includes using historical data to build the initial TCO model.
2. Negotiations, Bid Selection, and Contract Development. During the negotiation phase, collaboratively refine the TCO model with the OEMs under consideration. Analyze the cost parameters each provides by benchmarking them against historical or comparable data, for example. Discuss cost parameters with the OEMs and critically evaluate the underlying concepts. Note that some costs, such as overhead and track-related expenses, are driven by the operator, not the OEM. Once these steps are complete, the operator is ready to select an OEM among competing bids.
Apply the TCO model to monitor and control expenditures, such as each asset's lifetime maintenance costs and labor hours. Continuously refine the TCO forecast by measuring and testing parameters.
The TCO model also helps operators develop contract terms that ensure the effective management of lifetime costs (for example, cost per mile over a specified number of years). Incorporate mechanisms into contracts that align incentives with suppliers and manage cost overruns through penalties or other measures. Companies can choose among several different contracting models:
- Availability Based. Suppliers are responsible for any servicing or maintenance costs that operators incur because of failures or downtime that exceed the agreed-upon thresholds.
- Cost Based. Suppliers are responsible for any maintenance costs that operators incur beyond a predetermined threshold or expected lifetime ownership cost.
- Traditional Purchase. Operators buy the trains, and suppliers commit to certain target ranges for performance parameters. If the rolling stock underperforms, the suppliers pay a penalty; if it exceeds expectations, they receive a bonus.
3. Tracking and Steering. Apply the TCO model to monitor and control expenditures, such as each asset's lifetime maintenance costs and labor hours. Continuously refine the TCO forecast by measuring and testing parameters. Rail operators must also identify deviations from planned costs and prioritize areas requiring attention or adjustment.
As rail operators seek to boost their reliability and cost-efficiency, enhancing the way they procure rolling stock is one piece of a broader transformation that includes improvements to infrastructure, operations , and maintenance. Integrating the TCO model into procurement enhances all aspects of rail operations . To embark on this effort, rail operators should begin by assembling the necessary data and facts to develop and evaluate bids on the basis of TCO. This foundational step sets the stage for applying TCO throughout the design, contract development, and operating phases. Companies that succeed in adopting a life-cycle perspective on costs will reap the rewards of stronger supplier relationships, better cost management, and more effective decision making.
The authors would like to thank Maximilian Roth for his contributions to this article.