This article is part of a series examining the competitive outlook for key global process industries and how they can prosper in an uncertain future.
As everyone in the industry knows, the immense amount of cement produced globally releases 3 gigatons of greenhouse gases (GHGs) annually into the atmosphere, and that amount is expected to increase significantly as demand for this critical material grows. The only realistic way to fully abate those emissions and meet the industry’s 2050 net zero goals involves scaling carbon capture and storage (CCS) to an industrial level. Industry experts expect this effort to require more than $1 trillion of capital deployment over the next 25 years.
For the industry to reach net zero in 2050, sufficient CCS capacity must be available to abate more than 35% of its GHG emissions.
For the industry to reach net zero in 2050, sufficient CCS capacity must be available to abate more than 35% of its GHG emissions—and its implementation will transform the industry’s cost structure and traditional sources of competitive advantage.
Today, most cement is consumed within 200 km of where it was produced, since the most cost-effective way to supply it is by serving local demand, thus minimizing transport costs. Only around 5% of the world’s total cement production is traded across country borders. The cost of CCS technology will change all that. Cement production costs will vary considerably depending on local access to CO2 storage capacity, proximity to industrial CCS hubs, and the cost and availability of the green energy needed to produce cement. This in turn will transform the industry’s global geographical footprint from an almost entirely local industry to one where the advantage goes to low-cost producers, wherever they are.
This article explores various factors that will determine the winners and losers in the cement industry of the future. (See the sidebar, “The Future of Process Industries.”)
The Future of Process Industries
Each article in the series will examine the nature of the new business reality faced by a particular process industry, and how the coming changes will drive technological progress, redefine the industry’s cost structure, and reshape its competitive landscape. The goal: to provide industry leaders with the data and guidance needed to ensure their companies can thrive in the coming years.
The Net Zero Timeline
The numbers are daunting. In the absence of any abatement action at all, global growth in demand for concrete is forecast to result in 3.8 gigatons of annual CO2 emissions by 2050. In the near term, to 2030, the industry will focus primarily on a variety of well-known decarbonization levers, including the gradual substitution of clinker materials (and their attendant process emissions), the use of alternative fuels, and a relative decline in demand for concrete as a result of greater design and construction efficiency.
In the absence of any abatement action at all, global growth in demand for concrete is forecast to result in 3.8 gigatons of annual CO2 emissions by 2050.
By 2050, however, more than a third of the industry’s emissions will have to be abated with CCS, according to the Global Cement and Concrete Association (GCCA), which will require an estimated 1.4 gigatons of CO2 in CCS capacity. (See Exhibit 1.) As of July 2023, however, the announced CCS capacity of GCCA members is just 19 million tons of CO2 a year. Making up the difference will not be easy, and the effects on the cement industry’s cost structure will be profound.
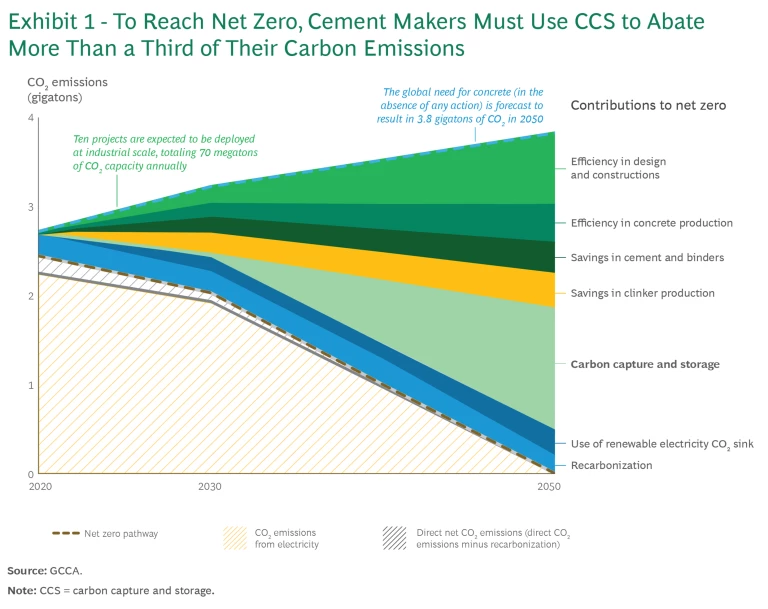
Today, the delivered cost of cement is determined largely by a plant’s proximity to limestone quarries and demand centers, its cost of energy (including the availability of alternative fuels), and the efficiency of its kilns. But the need for CCS, and the cost of implementing it, will change that dramatically.
Winners and Losers
The cost of CCS will drive a significant increase in the price per ton of delivered cement from a current $90 to $130 to at least $160 to $240 by 2050. The cost of the raw materials needed will be unaffected. But the cost of energy needed to make cement could rise by $20 to $30 per ton, after taking into account the energy cost required to capture CO2 emissions. And transport costs, including the cost of transporting CO2 to storage facilities, could triple and rise by another $20 to $40 per ton. (See Exhibit 2.) On the plus side, CCS costs will likely decrease as this technology matures and is deployed at scale.
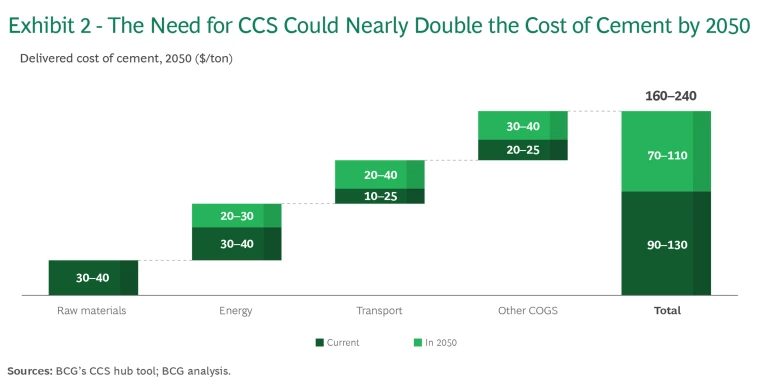
As the role of CCS in abating carbon emissions grows, benefiting from optimal CCS cost will become an increasingly important competitive factor. This is turn will realign who is advantaged and who isn’t, determining the extent to which cement plants are future proof.
A key competitive factor will be how close a plant is to CO2 storage locations. Proximity will affect the cost of transporting captured CO2, as well as a plant’s connection to large-scale industrial CCS hubs to support shared infrastructure costs. Our analysis shows that CCS abatement costs at plants within 200 kilometers of storage locations will be half that of plants located more than 750 kilometers away.
As the role of CCS in abating carbon emissions grows, benefiting from optimal CCS cost will become an increasingly important competitive factor.
Further advantage will come from a plant’s access to cheap renewable energy for capturing CO2. Likewise, plants with large kiln capacities will drive significant economies of scale in using CCS to capture CO2. (See Exhibit 3.)
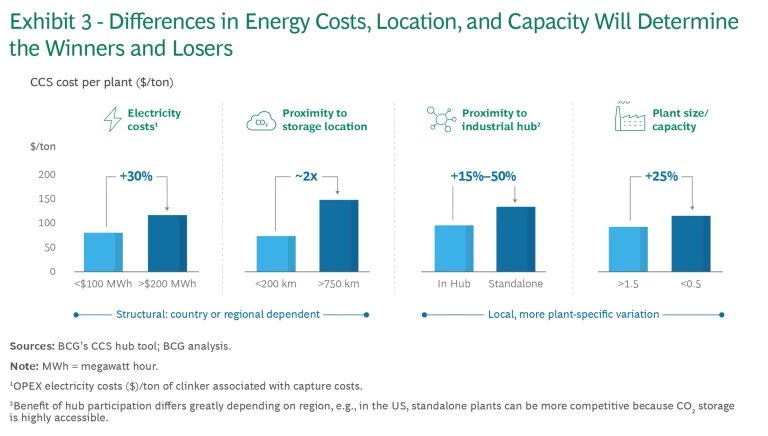
Moreover, what was once a strategic advantage for a plant, such as an inland location far from ports—and thus protected from import competition—could become a disadvantage in the future if it is located far from a CO2 storage site, as the high cost of transporting CO2 will impact the plant’s competitiveness within its historic market. On the other hand, plants near ports that once could export their marginal clinker production may no longer have a cost advantage over countries that once imported cement, after factoring in the cost of CCS.
Footprint of the Future
As all of these factors gain importance, five very different plant archetypes will emerge (see Exhibit 4):
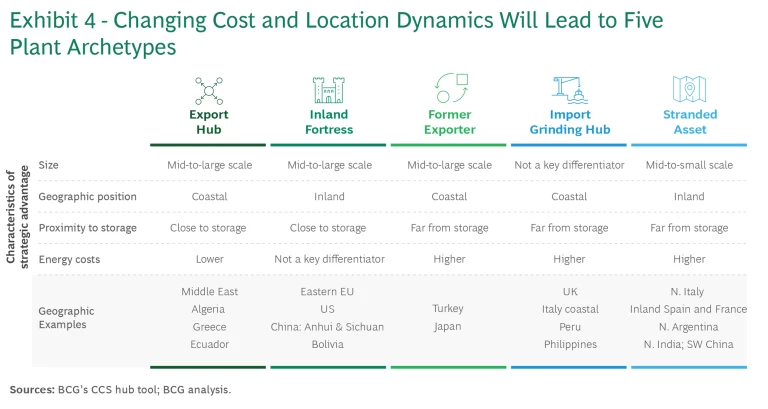
- Export Hub. Internationally cost competitive for CCS and located near a port for efficient export.
- Inland Fortress. Locally or regionally cost competitive due to onshore storage access and close to local demand centers.
- Former Exporter. Traditional exporter losing cost advantage due to high CCS abatement costs.
- Import Grinding Hub. No cost advantage for CCS but close to a port, allowing it to import cost-advantaged net-zero clinker and grind it locally to serve local markets.
- Stranded Asset. Limited structural cost advantage, at risk depending on cost of clinker transport.
Plants that can keep CCS abatement costs low and maintain outlets for their product will thrive.
These archetypes will determine the cement industry’s future local and global market structure and trade flows. (See Exhibit 5.) Plants that can keep CCS abatement costs low and maintain outlets for their product will thrive; those without competitive CCS abatement costs will likely become too costly and unattractive to investors, leading to plant closures.
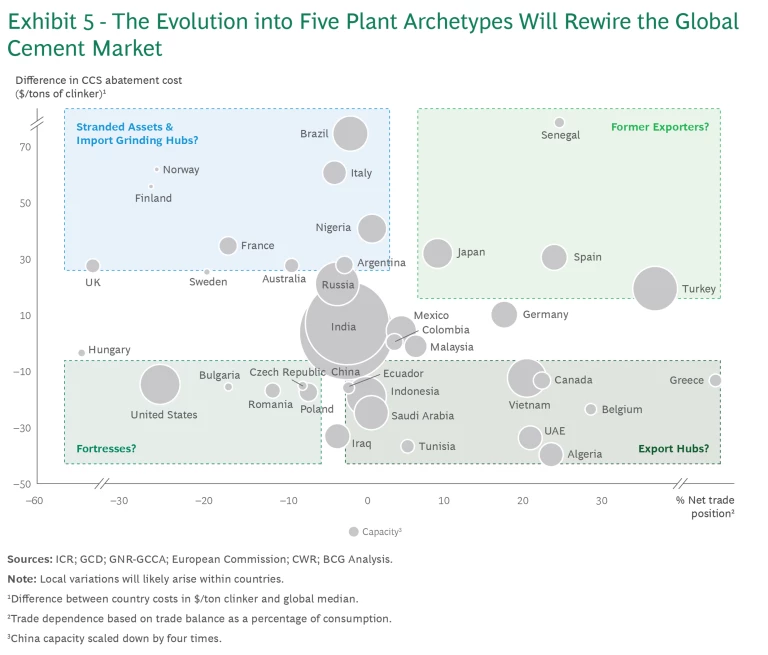
The competitive advantage for the Middle East, for example, lies in its structurally lower energy costs, which could lead to a $20 per ton advantage in CCS cost versus the global median. Saudi Arabia, in particular, could become an Export Hub.
Similarly, in the US and Canada, the distance to suitable CO2 storage such as saline aquifers and depleted oil and gas reservoirs is around 50 kilometers on average––eight times less than the distance in Europe, giving the two countries an advantage in the cost of clinker of $20 per ton. This should enable them to thrive as Inland Fortresses focused on their own internal supply-and-demand dynamics, and potentially leading to the reshoring of much of the 15% to 20% of clinker production that is currently imported.
In contrast, many parts of Europe face considerable competitive challenges because they have much higher energy costs and are located much further from suitable CO2 storage sites. In many European locations, producing clinker could become economically unattractive. However, this is highly variable locally: we anticipate a $70 to $100 per ton difference between first- and fourth-quartile EU plant abatement costs. In the future, it might become more economical to serve these markets with neighboring plants, both within Europe and elsewhere, that benefit from more competitive CO2 abatement costs and that are located in places that can export their excess capacity.
In many European locations, producing clinker could become economically unattractive.
The realignment of the disparities among cost and strategic factors at the country level will lead to further rationalization of production capacity, a rewiring and increase of regional and global trade flows, and a more globalized clinker market.
Three Potential Futures
Exactly how much realignment takes place among cement producers will depend on two factors: the availability and degree of regulatory and policy support, and the extent of innovation in the industry. Those factors in turn will determine the industry’s overall structure and competitive landscape.
The more local support that plants receive for CCS––including policies allowing for onshore storage, CCS investment, and the development of competitive green energy––the less the industry will rely on reducing the global clinker production footprint. (See the sidebar, “Regulating the Future.”)
Regulating the Future
Regulatory decisions regarding onshore storage of CO2 must also be made, as they can profoundly affect the cost of CCS. At present, CO2 storage in Europe is allowed only offshore. While Northern Europe benefits from proximity to the North Sea’s oil and gas reservoirs, areas such as southwestern France and Spain could be left significantly more isolated and face unviable CO2 transport costs.
Should onshore storage be allowed, however, the fate of many plants could be reversed. Onshore storage would enable Spain to increase its clinker exports further due to its favorable energy-cost position and excess capacity, for example. In Italy, local support of affordable green energy for industries would also reduce relative capture costs–– and change the competitive dynamic considerably.
The industry’s success in pursuing the innovations needed to develop cost-effective new supplementary cementitious materials (SCMs) to replace clinker, or even cement, will also impact its future footprint—but its ability to do so remains highly uncertain. The more that plants can use green alternatives, the less the industry will require abated clinker capacity in the future. This would drive further capacity rationalization and support cost-effective clinker capacity with CCS at the local rather than global level. (See the sidebar, “Innovation in the Mix.”)
Innovation in the Mix
The cement industry, therefore, faces a double innovation challenge: it must compensate for the drop in traditional SCMs by scouting new cementitious materials to reduce the use of clinker; and it needs to develop substitutes of cement itself.
The ability to develop credible alternatives, at scale, will depend on the evolution of cement and concrete product standards, the availability of alternative raw materials, and the capital needed to develop them. Recent recognition of low-emissions cement blends by the EU and investment in alternatives such as calcined clay, suggest the path forward in developing new lower-cost, sustainable cementitious materials.
Depending on the relative levels of the two factors, different plant locations will experience one of three potential futures (see Exhibit 6):
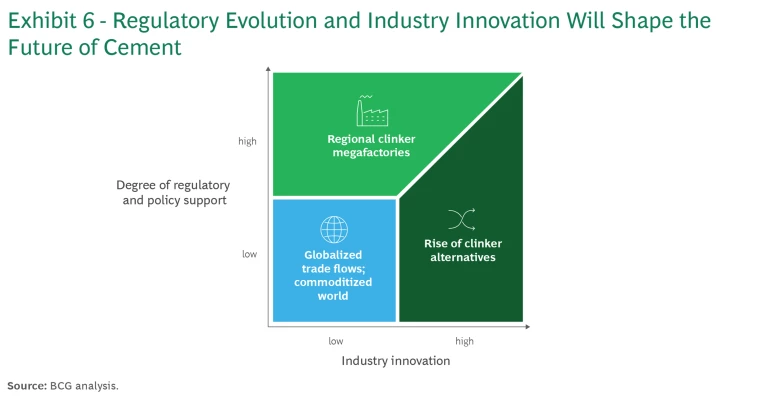
Globalized Trade Flows; Commoditized World. A lack of policy support and innovation would lead to both an increase and a rewiring of trade flows at a global level, due to significant regional differences in the cost of CCS. In the short term, local producers will continue to be favored as countrywide or regional markets maintain their own internal incentives to decarbonize. In the longer term, the industry’s production footprint will become more global, as more and more cement is exported from naturally advantaged CCS locations.
Regional Clinker Megafactories. Strong regulatory support across regions would lead to a future in which the equalized cost of CCS reduces global disparities. This would effectively drive a consolidation of clinker production at the regional level (rather than global) into fewer, larger regional factories. Clinker capacity would consolidate around locations with favorable CCS economics, notably Inland Fortresses and Export Hubs. Such industry rationalization will decouple clinker production from cement grinding, which will remain local and drive uneconomical assets out of the market.
Rise of Clinker Alternatives. Stepping up product innovation in the industry would drive the development of cost-effective alternatives to clinker, reducing its ratio in cement production to less than 50% and driving reduced clinker requirements. Innovative alternatives to cement would give rise to a range of new producers while benefiting admixture players. Reduced demand for clinker would force further rationalization of clinker capacity into fewer, more economical production hubs.
Call to Action
Cement producers looking to maintain or gain a competitive advantage in a changing industry must make critical decisions today regarding how they will allocate capital, innovate, and determine their strategies for success in a net zero future. Players should take the following key steps to navigate the transition.
Players must adopt a holistic approach in defining, delineating, and prioritizing decarbonization initiatives and a road map for implementation.
1. Develop a decarbonization road map. Pulling all currently available decarbonization levers will lay a crucial foundation for the CCS future. Players must adopt a holistic approach in defining, delineating, and prioritizing decarbonization initiatives and a road map for implementation.
2. Assess your footprint of the future. The most competitively advantaged plants of the CCS future—Export Hubs and Inland Fortresses—will claim an increased share of local and export markets. Assessing plant footprint in light of future industry evolution, determining your business model for competitive advantage, and conducting war games to test resilience are critical strategic imperatives for every cement maker.
3. Craft an innovation strategy. Cement makers should determine how innovation can best align with future strategy; assess their own R&D capabilities and potential ecosystem of partners; and allocate resources to support their innovation portfolio. Careful selection of which innovation areas to focus on and access to the enabling resources is critical.
4. Identify key policy needs and prepare for regulatory engagement. Local regulatory support for CCS will make or break the economics of many at-risk plants. Players should identify the most critical policy interventions, assess the viability of proposed policies, and prepare for how to engage with governments and other stakeholders, including industry associations such as the GCCA and regional and national associations.
5. Define how you will manage large capital projects. The scale of most capital expenditure projects—as much as $300 million or more—means that delivering them on time and within budget is critical. Players should identify and engage with the ecosystems needed to develop major CCS capital projects with industrial partners and develop large capital project management capabilities.
The scale of most capital expenditure projects—as much as $300 million or more—means that delivering them on time and within budget is critical.
6. Create a green go-to-market strategy. In the future, demand for sustainable construction materials will increase. To thrive, cement makers must be able to measure and report their product carbon footprint in order to guarantee the reliability of their green products. Moreover, players should rethink their go-to-market strategies to target new segments for their low-carbon products, and scout opportunities for capturing green premiums.
The competitive dynamics of the global cement industry are changing rapidly as the need to decarbonize becomes increasingly pressing. Cement makers should begin now to determine how CCS will affect their production and pricing, and how that will change their competitive position locally and globally—and to develop the winning strategies that will enable them to thrive.