Rail infrastructure maintenance is essential for ensuring the capacity, reliability, and safety needed to sustain modern rail networks . At the same time, it represents a major financial commitment, accounting for 30% to 40% of operational expenses, on average, in Europe. As aging infrastructure and surging demand push rail systems to their limits, optimizing maintenance strategies has become a business imperative for railway operators striving to maintain their efficiency and resilience. (See “Key Challenges in Rail Infrastructure Maintenance.”)
Key Challenges in Rail Infrastructure Maintenance
Overreliance on Reactive Maintenance. Limited data accuracy and inadequate asset management systems hinder effective maintenance planning. This forces a reactive approach that disrupts service and raises operational costs.
Aging Infrastructure. Decades of underinvestment have resulted in aging rail networks that require more frequent maintenance and renewal activities. Increasing constraints on track capacity exacerbate the problem.
Lack of Strategic Focus. Maintenance prioritization often follows inconsistent and ad-hoc processes, leading to inefficient resource allocation. These shortcomings prevent networks from optimizing operations.
Lengthy Modernization Processes. Low-tech legacy components with long lifespans delay modernization efforts. Fragmented systems, diverse software tools, IT platforms, and digital solution, and a lack of standardization across regions further complicate change management and impede the transition to modernized systems.
Increased Political Scrutiny. As state funding priorities shift from new construction to maintenance, infrastructure managers face mounting political pressure to achieve goals and translate funding into tangible results. Effectively utilizing these funds requires a deep understanding of the current state of infrastructure and well-structured processes to plan strategically, tactically, and operationally. Compounding the challenge is the significant time and effort needed to scale up the supplier base to meet increased maintenance demands—often outpacing the availability of government funding.
To address their maintenance challenges, infrastructure managers must move away from outdated, overly reactive practices and inconsistent local approaches. Instead, they should embrace proactive and data-driven strategies that combine standardized processes with a differentiated approach tailored to specific infrastructure components. This approach considers factors such as criticality, likelihood of failure, and repair and maintenance costs, while allowing for reactive measures when necessary.
By increasing the maturity of maintenance processes and embracing digitization, infrastructure managers can reduce manual workloads and improve workforce planning so that the use of skills is optimized. Improved maintenance strategies also contribute to sustainability efforts by extending the lifetime of assets and reducing unnecessary track inspections. Using the frameworks outlined below, infrastructure managers can increase maintenance productivity by up to 20% while improving operational stability by up to 15%.
Approaching Maintenance Processes as an Integrated Cycle
To transform rail maintenance from a reactive necessity into a strategic function, infrastructure managers need to adopt an integrated, life cycle approach. Rather than focusing on isolated tasks, they must ensure that all phases of maintenance are interconnected in a seamless cycle.
Each of the maintenance phases described below feeds into the next, creating a structured, data-driven system that enhances overall performance. (See Exhibit 1.) Achieving high reliability and meeting acceptance criteria require prioritizing the right work and executing it efficiently—both of which depend on strong planning and accurate data capture. Effective implementation, reporting, and analysis provide the insights needed for continuous improvement.
- Setting Goals and Acceptance Criteria. Establish the key indicators for monitoring the program’s success and set the standards or requirements that maintenance work must meet to be accepted.
- Designing the Maintenance Program. Define the tasks to be performed, including their frequency and means of execution, to ensure alignment with the specified acceptance criteria.
- Planning. Develop detailed plans for executing maintenance tasks, including the allocation of resources and materials.
- Implementation. Focus on the actual performance of all infrastructure maintenance tasks according to the plan.
- Reporting. Document and register the work performed, highlighting any issues or deviations discovered during maintenance.
- Analysis. Evaluate data and results to identify trends, problems, or opportunities for improvement in maintenance.
- Making Improvements. Implement measures to refine maintenance practices, optimize processes, and minimize errors.
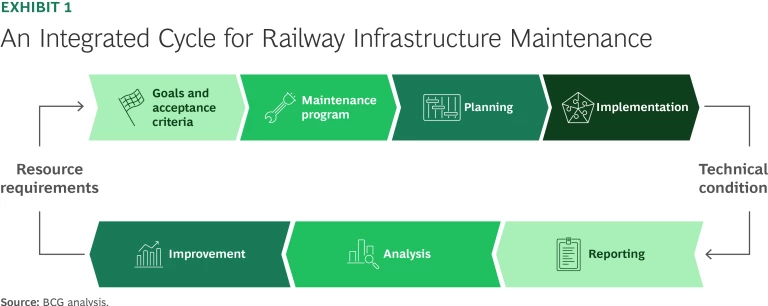
Over time, the technical condition of infrastructure changes, reflecting wear, damage, or improvements. This process is captured through reporting and analysis, informing future actions. Similarly, the resources needed for maintenance shift in response to those changes, with resource allocation defined and adjusted through the maintenance program and planning phases.
Although outsourcing can play a role throughout the cycle, infrastructure managers must act as orchestrators, ensuring that all processes are interconnected and aligned with overarching asset management objectives. (See “Ownership of the Maintenance Cycle.”)
Ownership of the Maintenance Cycle
Goals and acceptance criteria must always remain within the infrastructure manager’s control, ensuring that maintenance efforts meet strategic and performance expectations. The maintenance program, planning, implementation, and reporting may follow different outsourcing models, varying by region, asset type, or maintenance category (for example, preventive versus corrective).
The maintenance program serves as the foundation for structuring all maintenance activities, making it essential that the responsible party is highly competent, regardless of who carries out the work. Analysis and improvement must remain within the infrastructure manager’s steering capabilities. Even if analytical work is outsourced, the insights must be transparent, reliable, and readily accessible to support data-driven decision making.
Ultimately, ownership of the maintenance cycle is about orchestration, not execution. Whether tasks are handled in-house or by external providers, infrastructure managers must ensure a fully integrated system in which insights flow between processes, enabling continuous improvement and long-term network resilience.
By viewing the cycle as an integrated system of strategic and operational processes, infrastructure managers can optimize the value derived from their assets. This requires setting differentiated goals for specific areas, lines, or sections, as well as focusing on robust planning, detailed analysis, and continuous improvement.
Subscribe to read our latest insights on Travel and Tourism.
Assessing the Maturity of Maintenance Levers
BCG’s maintenance framework for rail infrastructure is designed to evaluate the maturity of maintenance levers grouped into three dimensions: basic, productive, and digital. (See Exhibit 2.)

Some basic levers can be applied at the component or function level, while others require company- or infrastructure-wide implementation to ensure consistency and efficiency. In contrast, all productive and digital levers can be tailored to specific components or disciplines, allowing for targeted enhancements to deliver the greatest impact.
As shown in Exhibit 2, the three dimensions build on one another, emphasizing the need to have the foundational levers in place before progressing to more advanced practices. The framework enables a detailed assessment of maturity within each group of levers, providing a clear picture of the current state and a guide for targeted improvements.
Basic. These foundational levers ensure reliable and consistent rail infrastructure maintenance and execution. They can be grouped into three subcategories:
- Infrastructure. Developing and documenting a comprehensive asset catalogue provides a clear and detailed overview of all assets, which can then be addressed through maintenance processes, such as planning, material management, and execution. Conducting criticality analyses identifies risks and prioritizes care for key components based on their cost and operational impact.
- Processes. Standardizing and documenting processes across the entire maintenance cycle, from planning to execution and feedback, facilitates their tight integration with infrastructure and resource planning. This yields a streamlined operation that minimizes delays and inefficiencies.
- People. Allocating staff to the right tasks optimizes both efficiency and quality. For example, rail workers should focus on executing maintenance tasks, while planners should specialize in creating schedules based on accurate data. This clear division of roles ensures that each team member contributes effectively to the maintenance effort.
Productive. These more advanced practices focus on enhancing the effectiveness of rail maintenance. A key lever is performance management, which involves establishing clear KPIs and regularly tracking progress to measure productivity and operational outcomes. Autonomous maintenance plays a crucial role by equipping operators with the skills needed to perform basic tasks such as inspections and adjustments, accelerating problem resolution and increasing equipment uptime.
Systematic problem solving strengthens maintenance effectiveness by making root cause analysis a standard practice in addressing recurring issues and preventing future failures. Work process optimization and standards further improve efficiency by refining workflows, ensuring consistency across teams, and facilitating the sharing of best practices. Finally, contractor management ensures that external providers meet performance expectations and organizational standards.
Digital. Leveraging cutting-edge technologies enhances maintenance strategies and promotes superior outcomes. A key lever is machine data collection and analytics, where sensors and monitoring systems provide real-time insights into rail infrastructure conditions. This continuous data stream enables predictive analytics, which allows infrastructure managers to detect potential issues before they escalate. Predictive maintenance applies these insights to the development of proactive strategies. By analyzing data trends, managers can anticipate equipment failures and schedule interventions before disruptions occur.
Another transformative innovation is additive manufacturing, which integrates 3D printing to produce spare parts on demand. This approach not only lowers lead times and costs but also enhances flexibility in repairs, ensuring that essential components are available when needed. Although not suitable for all parts owing to safety requirements, additive manufacturing is already in use for rolling stock and holds untapped potential in infrastructure maintenance, such as in the production of spare parts for maintenance machinery.
By focusing on the highest-priority levers, infrastructure managers can significantly enhance performance across the maintenance cycle for key sections of the network. These efforts can also serve as lighthouses for broader improvements, showcasing the tangible benefits of strategic, prioritized investment in maintenance capabilities.
Importantly, achieving progress does not require uniform maturity across all areas, nor does it necessitate perfecting every basic lever before advancing. Instead, infrastructure managers can selectively move toward best-in-class maturity for levers affecting the components, functions, or geographic areas that have the greatest impact on their goals and concrete use cases for improvement.
Subscribe to read our latest insights on Travel and Tourism.
The Approach in Action: Track and Switch Maintenance
Track and switch maintenance illustrates how infrastructure managers can apply our strategic approach to high-value components to maximize operational stability and optimize resource use. (See Exhibit 3.)
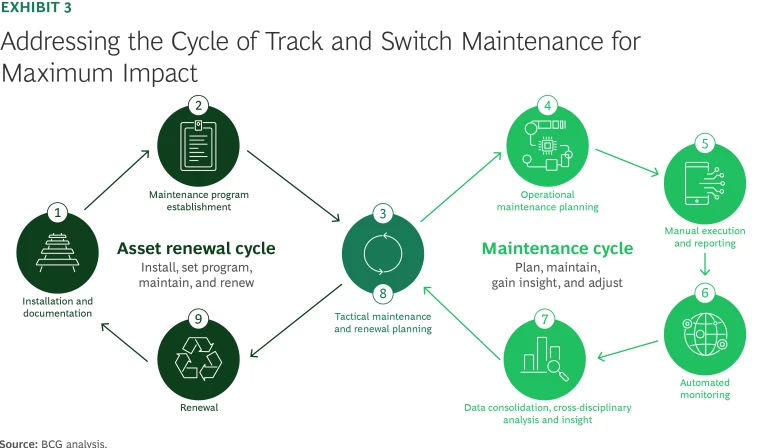
Installation and Documentation. The cycle begins with the installation of new infrastructure, with every detail—from configurations to work history—documented in a unified platform. This foundational step ensures a consistent, accurate record that will guide future maintenance and planning efforts.
Maintenance Program Establishment. The next step is creating a comprehensive maintenance program tailored to the infrastructure’s specific needs. For tracks and switches, this program is informed by a reliability-centered maintenance analysis, taking into account factors such as criticality and traffic strain. This increases reliability while avoiding unnecessary maintenance. The program outlines recurring preventive tasks, such as inspections and track grinding, aligned with standardized processes to ensure routine care and minimize reactive maintenance. Additionally, basic visual inspections are streamlined by grouping, or bundling, them within specific operational zones. Bundling not only enhances efficiency but also lays the groundwork for future automation using cameras and image recognition.
Tactical Planning for the Maintenance Cycle. The maintenance program allows managers to develop a multiyear rolling tactical plan for the maintenance cycle. Using criticality analysis and historical failure data, they identify high-priority areas, allocate resources effectively, and create a framework for long-term efficiency.
Operational Maintenance Planning. Operational plans break down the strategic goals into actionable tasks and schedules, ensuring alignment across teams and smooth execution. Digitization plays a crucial role by leveraging machine-to-machine interactions to support maintenance-related decisions. This is achieved through an integrated ecosystem of asset management tools that connect analysis, planning, and execution. Predicting future maintenance needs can be improved by incorporating AI, particularly machine learning. To minimize disruptions, maintenance planning must remain dynamically aligned with train operations—from the initial capacity strategy through the day of execution—ensuring optimal use of available downtime.
Manual Execution and Reporting, On the ground, frontline teams carry out inspections, grinding, and other maintenance activities, documenting their work in real time through a user-friendly system. QR codes on components provide access to critical data, allowing workers to retrieve information on-screen.
For systems that are challenging to navigate—where it is difficult to input data or to access work orders or guidance documents—an added layer of generative AI can streamline interactions. By providing voice control and intuitive search capabilities, GenAI can act as a bridge between workers and complex systems, making it easier to retrieve instructions, log maintenance activities, and ensure accuracy. While highly beneficial in legacy or poorly integrated systems, this layer is less critical when the maintenance system is already well aligned with operational processes.
Automated Monitoring. High-resolution video inspections from automated measurement vehicles supplement manual efforts, with advanced algorithms detecting potential issues. This integration of manual and automated monitoring represents a pivotal shift toward condition-based maintenance.
Data Consolidation and Cross-Disciplinary Analysis and Insight. As data from inspections, sensors, and maintenance logs flows into the system, a multidisciplinary team consolidates and analyzes it to generate actionable insights. By tracking KPIs such as downtime, resource utilization, and work order completion rates, the team identifies areas for immediate operational adjustments and long-term changes in maintenance processes.
A robust analysis environment provides better data for decision making, enhancing the value of every step in the maintenance cycle, particularly the maintenance program and tactical planning phases. This creates a self-improving cyclical process, as standardized processes are refined through deeper insights from manual and automated data capture.
These insights allow the manager to identify components for which maintenance can be deferred or is required and components that must be replaced. This decision-making process, informed by criticality analysis and performance data, ensures that resources are focused where they will deliver the greatest impact.
Tactical Planning for the Renewal Cycle. As part of tactical planning, teams assess whether to prioritize maintenance or renewal in the context of other renewal activities or planned track closures in the area. This process involves two evaluations: first, determining whether continued maintenance or immediate renewal is more cost effective and, second, deciding whether to proceed with renewal regardless, given the efficiencies to be gained from aligning it with other scheduled work.
For the initial assessment, teams estimate the remaining lifespan of components, compare maintenance and renewal costs, and analyze criticality and failure risks, drawing on insights from a cross-functional analysis team. For the second, they examine historical pricing data to predict cost savings from bundling renewal tasks, rather than managing them as standalone projects later on.
Renewal. Given these cost considerations, renewal plans are designed to bundle tasks geographically, minimizing disruptions and maximizing efficiency. To prevent cost escalation, infrastructure managers need long-term predictability in the supplier market and well-structured, bundled work packages adapted to the market’s capacity. This approach is particularly critical when funding increases, as it helps suppliers scale efficiently to meet higher demand. Once executed, the renewal plan feeds into the next cycle, aligning with long-term asset care strategies.
By embracing a strategic approach to rail infrastructure maintenance—one that integrates foundational and advanced management practices and cutting-edge digital tools—managers can effectively address their network’s most essential components. This includes prioritizing maintenance and renewal efforts for high-value assets based on factors such as remaining lifetime, criticality, and cost effectiveness. Addressing the full maintenance cycle with precision and prioritization not only enhances reliability and performance but also creates a self-improving system that feeds better insights into every step of the process. As the demands on rail networks continue to grow, those that take decisive action today will be best positioned to deliver the capacity, safety, and innovation needed to power tomorrow's transportation systems.
The authors thank Thea Rostrup for supporting this study.