Global demand for batteries is rising, but not as fast as market experts anticipated. As a result, the announced global cell production capacity could outstrip demand by as much as twofold over the next five years, driven primarily by overbuilding in China. The overcapacity and low utilization rates will drive intense price competition, especially from low-cost Asian producers, making operational efficiency essential for maintaining competitiveness.
To optimize efficiency, cell producers can transition to the factory of the future, potentially reducing conversion costs by up to 30%. This transformation involves retrofitting existing plants and designing new facilities that incorporate next-frontier technologies, such as the latest advancements in automation and
artificial intelligence
, along with proven lean process enhancements.
Cell Makers Must Reduce Conversion Costs
In their efforts to enhance efficiency, cell makers should prioritize reducing conversion costs—that is, production costs excluding material costs—which constitute 20% to 30% of total battery production costs. Exhibit 1 highlights two notable trends. First, as material costs decrease, conversion costs become more significant. Conversion costs account for about 20% of production costs for nickel manganese cobalt (NMC) batteries, versus approximately 30% for lithium iron phosphate (LFP) batteries. Second, the highly asset-intensive nature of battery production, with equipment depreciation and amortization contributing significantly to conversion costs, underscores the importance of maximizing factory utilization.
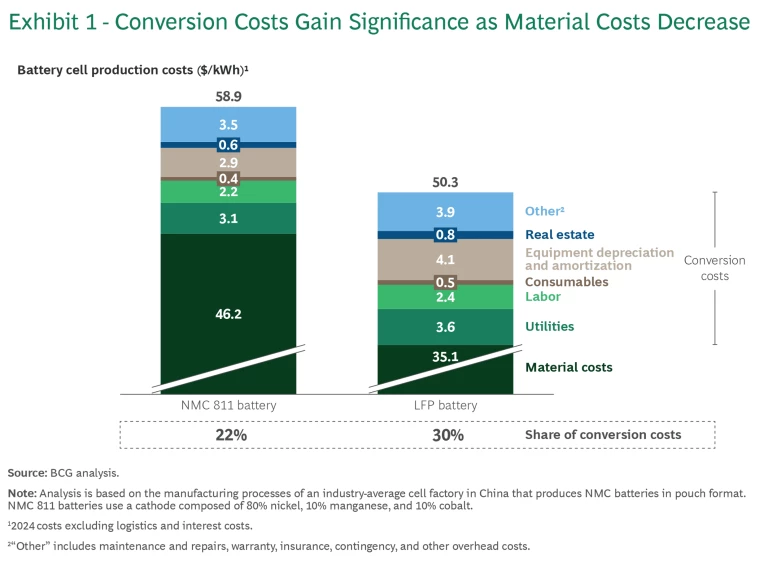
Regional differences in utility and labor costs create a further imperative to address intensifying global cost competition. Lower utility and labor costs in China result in conversion costs for NMC pouch batteries of approximately $13 per kilowatt-hour (kWh), compared with $17 per kWh in the US and $22 per kWh in Germany. (See Exhibit 2.) To counteract their structural disadvantage, manufacturers in high-cost countries must explore strategies to reduce costs and improve efficiency.
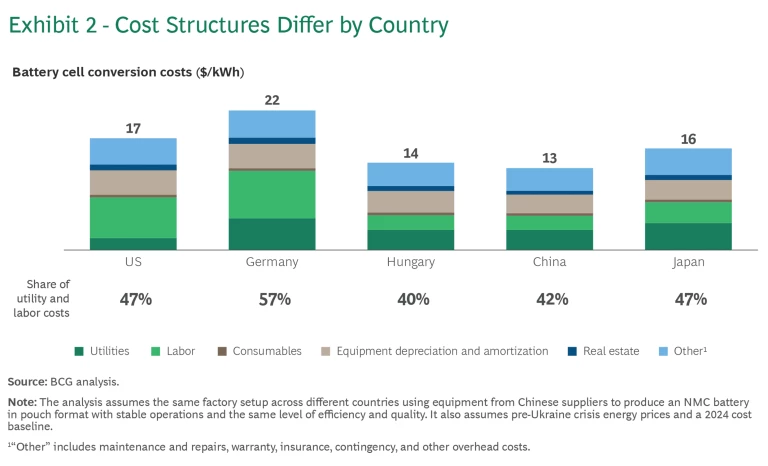
The Battery Cell Factory of the Future Offers Solutions
The battery cell factory of the future addresses the challenges of cost optimization through improvements in four dimensions. (See Exhibit 3.)
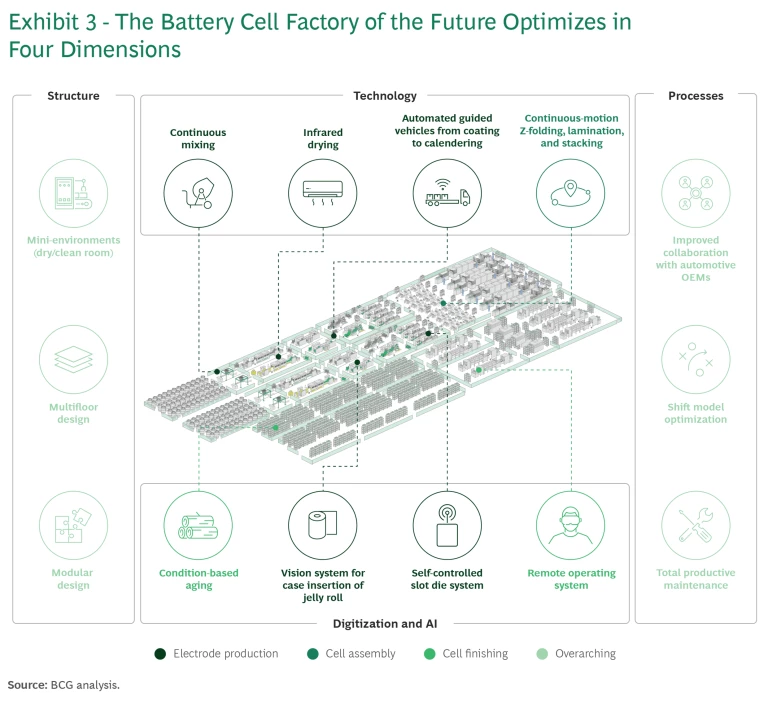
Each dimension encompasses a variety of innovative measures, spanning different levels of technological maturity. (See “Technology Maturity Levels.”)
Technology Maturity Levels
- Research Phase. New concepts are tested and refined in a controlled laboratory environment to validate their feasibility and potential benefits.
- Pilot Phase. Technologies are tested on a small-scale pilot production line in a real manufacturing environment to assess their performance, scalability, and integration with existing systems.
- Ramp-Up Phase. Techniques are deployed in incremental stages for large-scale production, focusing on scaling operations, optimizing processes, and addressing any operational challenges.
- Large-Scale Deployment. Measures are fully integrated into mass production, operating at full capacity with proven reliability, efficiency, and maturity.
1. Structure
Optimizing factory layouts and battery-specific infrastructure can significantly reduce operational costs and the physical footprint. Valuable measures include the following.
Mini-environments. Conventional factory setups typically rely on large, costly dry or clean rooms that can account for up to 30% of total utility costs. Mini-environments offer a more efficient alternative by maintaining controlled conditions around specific equipment, allowing the surrounding area to operate under normal conditions. This targeted approach reduces operational costs by minimizing the volume of air that requires management. However, mini-environments introduce maintenance complexities and necessitate integration with automation systems, such as automated guided vehicles for material transport. Although mini-environments have been deployed for electrolyte filling, this technology is still in the pilot stage and large-scale deployment remains unproven.
Multifloor Layouts. Multifloor layouts can reduce the environmental footprint of a factory while shortening in-plant logistics pathways. Notable examples include Tesla's facility in Berlin and LG Energy Solution's plant in Poland. However, the advantages of this layout must be carefully balanced against challenges that include load-bearing limitations, increased vibration, and higher construction costs.
Modular Design. Modular design enhances factory flexibility by decoupling production steps, such as electrode coating, drying, calendaring, and slitting. It allows changes to be implemented independently, facilitating the replacement of production equipment with new machinery or technologies as needed.
2. Technology
Technological advancements can improve yield while reducing utility and labor costs. We assessed more than 30 technological innovations, ranking them by maturity and business impact. (See Exhibit 4 for a selection.) Three examples of highly valuable measures include the following.
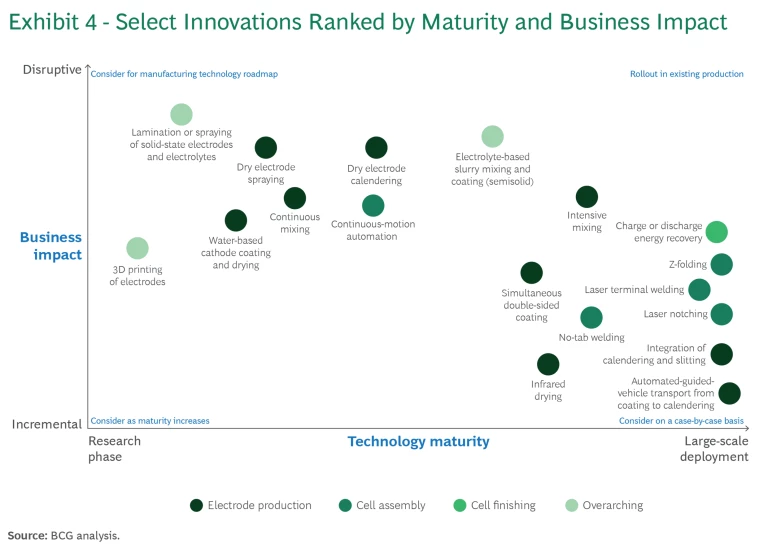
Continuous Mixing. Conventional double planetary mixers produce slurry in batches. This process has drawbacks, including the need for buffer tanks and machine stoppages to remove material, which reduces efficiency. Continuous mixers provide an alternative by blending materials in a steady flow using an extruder. This approach has the potential to significantly increase throughput—up to 3,000 liters per hour compared with the 1,000 liters per hour typical of conventional batch mixing—while eliminating the need for buffer storage. In addition, extruders have the ability to knead materials, a critical process for breaking apart powder agglomerates; in theory, this allows extrusion mixers to achieve slurry quality superior to that of traditional mixers.
However, several challenges must be addressed before continuous mixing can transition from its current pilot stage to large-scale adoption. Above all, ensuring a consistent feed flow of powdered material remains a challenge, requiring advanced quality control systems to maintain reliability.
Infrared Drying. Conventional convection ovens used for drying electrodes have several drawbacks, including safety concerns from potential leaks in hot-oil ovens (operating at 200°C to 300°C), long startup and cool-down times, and high maintenance costs. Infrared drying presents an alternative, utilizing infrared radiating panels to rapidly evaporate solvents. This method can reduce both energy and space requirements. However, precise control of energy density is crucial to prevent issues such as binder segregation or, in extreme cases, solvent ignition. To address these risks, some battery manufacturers combine infrared drying with convection ovens. While infrared drying is widely available from equipment vendors, its adoption by battery producers is still in the ramp-up phase.
Electrode Dry Coating. Conventional wet-coating processes rely on solvents to help mix active material particles and binder. A significant portion of the subsequent drying phase is dedicated to removing these solvents, requiring large ovens and solvent recovery systems. Electrode dry coating eliminates the need for solvents by directly mixing the binder with active material powder. This approach promises substantial benefits, including the elimination of ovens and solvent recovery systems, as well as a potential increase in mixing yield by up to 30% owing to the absence of solvents.
Technological advancements can improve yield while reducing utility and labor costs.
Given its potential, most battery manufacturers are actively developing this technology and have demonstrated its feasibility on pilot lines. For example, LG Energy Solution plans to commercialize dry coating by 2028, estimating that it could reduce production costs by up to 19%. Yet applying the technology in large-scale operations, particularly at coating speeds of 60 meters per minute or higher, remains a significant challenge. Key hurdles include preventing holes in the powder film, ensuring edge consistency, and maintaining uniform film thickness. Notably, cathode dry coating poses even greater challenges than anode dry coating. As a result, the large-scale viability of this technology is still under debate and it remains in the pilot phase.
3. Digitization and AI
Digital tools and the latest advancements in AI can enhance machine uptime and reduce manual labor. Leading examples include the following.
Self-Controlled Slot Die System. Conventional coating systems require manual adjustments to slurry parameters, such as thickness, each time a new foil coil is loaded. With typical coils spanning 10 kilometers and coating speeds averaging 60 meters per minute, this adjustment process is needed roughly every three hours, often wasting 15 to 20 meters of foil per adjustment. Self-controlled slot die systems address this issue with machine learning, leveraging advanced measurement tools—such as beta gates and vision systems—to provide real-time feedback on profile and edge consistency. The system adjusts the lip angle and flow width of the coating unit automatically based on the data, reducing foil waste and improving the overall efficiency of the coater. This technology is currently in the ramp-up stage.
Digital tools and the latest advancements in AI can enhance machine uptime and reduce manual labor.
Condition-Based Aging. The aging process for battery cells at the end of production can take up to three weeks, during which time cells are stored under predefined conditions, monitored, and graded based on their performance. Advanced analytics using inline data can significantly shorten this process through early identification of high-risk cells. Only these cells undergo the full aging process, reducing the aging time for low-risk cells by up to 80%. This approach lowers capital expenditure for equipment and facilities by minimizing storage space requirements. The technology is currently in the ramp-up phase.
Remote Operating System. Conventional factory setups assign one operator per machine. Remote operating systems enable a single operator to manage multiple machines by providing real-time operational data, such as coating thickness and live images, while alerting the operator when action is needed on a specific machine. This approach significantly reduces operator idle time but requires upfront integration of all equipment with the supervisory control and data acquisition system. The technology is fully mature for large-scale
operations
.
4. Processes
Improving processes for production and manufacturing engineering boosts overall efficiency and safety. Notable measures include the following.
OEM Collaboration. To implement major changes to the so-called 4M components—man, machine, material, and method—battery manufacturers currently require up to 18 months owing to the need for approval from automotive OEMs. Closer collaboration between OEMs and cell manufacturers can streamline this process, enabling faster factory improvements and shared benefits.
Total Productive Maintenance. Battery cell manufacturing is an asset-intensive industry, making it crucial to maximize equipment utilization to spread fixed costs over high production volumes. Total productive maintenance measures can help minimize downtime. A critical aspect of total productive maintenance is autonomous maintenance, which empowers operators to perform basic equipment care independently. This reduces reliance on dedicated maintenance teams and prevents deterioration of equipment by maintaining it in optimal condition.
Assessing the Economic and Environmental Impacts
We estimate that the factory of the future will reduce conversion costs in battery cell production by 20% to 30% from the 2024 baseline. (See Exhibit 5.) Cost savings can be achieved across the entire production process, with the most significant impacts on electrode production. The economic impact in specific cases depends on several factors:
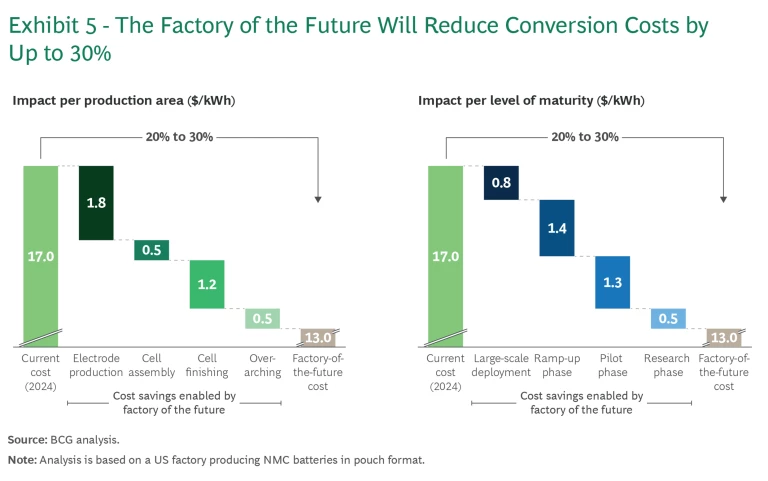
- Factory Setting. The extent of savings depends on local labor and utility costs and on whether the factory is a brownfield (existing) or greenfield (new) setup. Factories in high-cost locations will benefit the most from the factory of the future, as it reduces both labor and utility requirements. Brownfield sites may need to approach the factory of the future differently than greenfield sites, because they have already invested in existing technologies. Replacing current equipment may not be financially feasible unless it removes operational bottlenecks. However, brownfield factories can still benefit by optimizing labor models (for example, shift systems), reducing overhead, and deploying digital technologies .
- Technology Alternatives. The choice of technology will influence cost savings. For example, dry coating and simultaneous double-sided wet coating have different risk and maturity profiles, and they are mutually exclusive.
- Timing of Adoption. Immediate adoption of mature technologies can yield cost reductions of approximately 5 percentage points, while technologies available within the next five years may offer savings of an additional 10 to 15 percentage points. Longer-term innovations, available beyond five years, could bring another 5 to 10 percentage points in savings.
Because the economic feasibility of investing in innovations varies significantly depending on the specific technology and factory setting, manufacturers must make context-specific assessments. (See “Case-by-Case Evaluations of Cost Efficiency.”)
Case-by-Case Evaluations of Cost Efficiency
- Intensive Mixers. Although intensive mixers require higher capital expenditures per machine than conventional planetary mixers, they offer up to twice the throughput. This means that the overall capex requirement is lower per unit of output for intensive mixers. In a greenfield setup, this makes them an obvious choice. However, in a brownfield setup, where mixing may not be the bottleneck, replacing well-functioning planetary mixers with intensive mixers is often not an economical solution.
- Laser-Welding Equipment. These machines can require up to 50% more capex than ultrasonic-welding equipment. However, ultrasonic-welding tools need regular replacement (approximately every 100,000 cycles, or once per week), while laser welding is virtually maintenance free. The savings in operational expenses reduce the payback period for laser-welding equipment, making it a cost-effective investment despite the higher initial capex.
In addition to cost reductions, state-of-the-art technologies can decrease the substantial environmental footprint of battery cell factories. (See “The Environmental Impact of Battery Cell Factories.”) Operational efficiency improvements—such as automated slot die systems, dry coating, and mini-environments—can lower a battery cell factory's scope 1 and 2 emissions with a positive business case.
The Environmental Impact of Battery Cell Factories
- Energy Consumption. A 30 GWh battery cell factory consumes electricity equivalent to the amount consumed by a US town with approximately 90,000 residents.
- Emissions. Scope 1 and 2 emissions from an industry-average 30 GWh battery cell factory are estimated to be 150,000 to 240,000 tons of CO2 equivalent annually. These emissions are largely determined by the energy mix and drying technologies employed. Fully offsetting these emissions with wind power would require a wind farm with 160 to 250 turbines.
Emerging technologies will also help reduce factories’ physical footprint. For instance, continuous mixing increases throughput, dry coating eliminates ovens and solvent recovery systems, and condition-based aging shortens formation and aging times. As a result, the factory of the future may be up to 40% smaller than today's facilities while maintaining the same production output.
However, these efforts alone may not be sufficient to achieve net-zero targets because the factory of the future will still rely on electricity as its primary energy source. As a result, additional environmental measures—such as sourcing renewable electricity or generating power on-site through photovoltaic systems—will be necessary to promote
carbon-neutral factories
.
Overcoming the Main Obstacles
To successfully adopt emerging technologies in the factory of the future, battery cell manufacturers must address several challenges.
Scale. Transitioning from lab scale to mass production remains a significant challenge. For instance, dry coating has proven effective at lab speeds of 15 to 20 meters per minute, but mature levels of at least 60 meters per minute have not yet been demonstrated.
Know-how. Newcomers and tier two battery cell manufacturers often lack the internal expertise needed to adopt advanced technologies. As a result, they tend to rely on proven technologies that are often five to ten years behind the state of the art. Although European companies have historically excelled in production technology, they now find themselves playing catchup in battery manufacturing. Joint ventures and partnerships with established players could provide a way to accelerate their technological capabilities.
Cost Pressure. Tight industry margins limit producers' ability to invest in capital-intensive technologies, making risk taking less feasible. For example, annealing—a heat treatment process used in electrode production—can improve the quality of cylindrical cells for winding, but it requires significant additional investments in heating and cooling systems.
Volatile Demand. The gap between forecasted and actual market growth, particularly in Europe and North America, has led to project cancellations and growing uncertainty. However, this presents an opportunity to rethink factory designs in light of recent technological advancements.
Dynamic Environment. The future dominance of specific battery chemistries and form factors is uncertain, adding complexity to investment decisions. Transitioning to new chemistries or cell formats can be expensive. For example, switching from pouch to cylindrical formats could necessitate replacing 50% to 60% of equipment—when moving from stacking systems to winding stations for compound generation, for example.
Setting the New Vision for Battery Cell Factories
To navigate these challenges and capitalize on the benefits of the factory of the future, battery cell producers should take the following steps:
- Evaluate optimization levers. Assess the business maturity and financial implications of optimization measures across each dimension of the factory of the future.
- Assess fit. Consider employee capabilities and specific factory conditions, such as location, format, cell chemistry utilized, and whether the factory is a brownfield or greenfield site. In addition, gauge the company’s risk appetite for adopting new manufacturing technologies .
- Develop a roadmap. Create a customized technology roadmap and factory configuration that aligns with the company’s profile and strategic goals.
By adopting this approach, battery cell producers can improve cost efficiency by up to 30% compared with the current industry average. As price pressure builds amid overcapacity, this is a pivotal moment for decision makers to define their vision for the factory of the future. Ensuring that cell factories are optimized for next-generation technologies and strategically positioned in an increasingly competitive market will be essential to long-term success.