Since the start of the COVID-19 pandemic, airline maintenance has deteriorated across key performance metrics. Technical dispatch reliability has declined by as much as 50%, while average maintenance-related delays have increased by a factor of two to three. Most critically, maintenance-related cancellations per thousand departures have risen by two to three times, ranking among the top three causes of controllable cancellations. Despite some improvement, progress remains slow and performance has plateaued in many cases.
Although these issues do not affect operational safety, the cost of deteriorated performance is severe and far-reaching. Flight disruptions caused by maintenance issues lead to lost revenue and higher compensation costs, with cascading effects on fleet utilization, crew scheduling, and overall network stability. Frequent cancellations erode customer trust, weaken loyalty, and expose airlines to regulatory scrutiny, potential fines, and competitive disadvantages. For larger carriers, the financial impact can exceed $100 million to $200 million annually.
In our work with airlines across the globe—spanning various sizes, business models, and degrees of network complexity—we have observed a consistent set of challenges affecting maintenance performance. Workforce constraints, parts shortages, and outdated planning systems are straining maintenance operations, making it increasingly difficult to meet the demands of today’s high-utilization schedules.
Addressing these challenges requires a strategic, technology-enabled approach that shifts maintenance operations from reactive problem solving to proactive execution. By implementing interconnected initiatives focused on workforce readiness, operational efficiency, infrastructure optimization, and supply chain resilience, airlines can significantly improve maintenance performance and reliability.
The Root Causes of Declining Performance
Several root causes are the most critical factors affecting airline maintenance efficiency and reliability.
Workforce Challenges. The aviation industry faces a severe shortage of qualified technicians, as the current pipeline of new workers is not keeping pace with retirements in an aging workforce. The median age of US aviation mechanics is 51, nearly a decade older than the broader workforce. In North America, the supply of aviation mechanics is expected to fall short by 20,000 to 25,000 workers in 2025, with the deficit potentially exceeding 40,000 by 2027.
Many carriers report that 15% of technicians have less than a year of experience, and 25% have less than three years. Since a technician typically needs three years to become fully productive—and even longer for specialized tasks such as sheet-metal work—this inexperience significantly hampers productivity. The problem is compounded by the loss of experienced mentors, making it harder for junior technicians to develop critical skills.
Parts Shortages. The aviation sector is grappling with challenges in the parts supply chain. Contributing factors include reliance on historical demand-forecasting systems, the exodus of senior supply chain talent, and the misalignment of parts distribution with evolving airline networks. Together, these issues make parts shortages the leading cause of maintenance-related cancellations at many airlines.
The aviation industry faces a severe shortage of qualified technicians.
Multigeneration Fleets. Airlines are operating aging fleets with diverse configurations across different generations of aircraft. By 2027, 58% of the global fleet will consist of newer aircraft, requiring technicians to possess skills applicable to both new and older models. This diversity complicates maintenance demands, increasing the need for specialized knowledge and the ability to manage multiple aircraft systems effectively.
Robust Demand. Air travel demand remains robust and is expected to stay well above prepandemic levels, even amid economic uncertainty. At the same time, constraints in new-fleet availability have tightened schedules, shrunk maintenance windows, and added to congestion at hubs and major stations. As a result, maintenance planning has become more complex, and the need for high levels of productivity within limited timeframes is greater than ever.
Inadequate Planning Systems. Historically, maintenance planning has relied heavily on tribal knowledge and personal networks within carriers. Pandemic-driven workforce reductions led to the loss of much of this institutional expertise, exposing the inadequacies of legacy planning systems. As maintenance environments become more complex, the limitations of these outdated systems have become clear, underscoring the need for more advanced, technology-driven planning solutions.
Subscribe to our Industrial Goods E-Alert.
A Vicious Cycle of Compounding Challenges
The pressures on airline maintenance operations are not isolated issues—they are compounding challenges that are making reliability harder to restore. Across the carriers we have studied, a pattern is emerging: more work is required within ever-shrinking maintenance windows, leading to schedule disruptions that further erode the ability to get ahead. There are numerous drivers of this self-reinforcing cycle, which makes planned maintenance more difficult and reactive work the norm. (See the exhibit.)
- Poor Fleet Health. Across many carriers, aircraft are operating with significantly higher levels of open minimum-equipment-list (MEL) deferrals. In recent years, MEL deferrals during critical periods have surged, with two-day deferrals up 40% to 60%, one-day deferrals rising 60% to 75%, and overdue deferrals increasing 70% to 90%. This means that more aircraft require urgent attention within shrinking timeframes, further straining already limited maintenance resources.
- More and Older Outstanding MELs. As the backlog of deferred maintenance builds, addressing overdue MELs takes priority over scheduled work. This forces carriers into a reactive maintenance mode, with immediate operational needs pushing out planned inspections and preventive maintenance tasks. The result is an increasingly fragile fleet, with maintenance decisions driven by urgent needs rather than strategic considerations.
- More Flights and Compressed Maintenance Windows. Tightening flight schedules, constrained aircraft availability, and high travel demand mean that the gaps during which work can be completed are shorter than ever. With more tasks falling into these compressed windows, execution becomes harder and inefficiencies accumulate.
- Late Arrival for Maintenance. Worsening on-time performance across many carriers has delayed arrival times at maintenance stations by 10% to 15% from prepandemic levels. This further reduces the already limited time available for maintenance, squeezing productivity even more.
- Lower Workforce Productivity. A junior workforce—with less experience and lower productivity—adds another constraint. Across the carriers we studied, 10% to 15% less work is being completed by the same number of technicians as before the pandemic. Combined with higher workloads and shrinking windows, this exacerbates the backlog.
- More Unfinished Work. More tasks, less time, and reduced workforce efficiency lead to a growing pile of unfinished work. Increasingly, aircraft are coming out of maintenance late in the morning, affecting downstream operations. More work is being deferred and MELs continue to accumulate, pushing the problem further down the line.
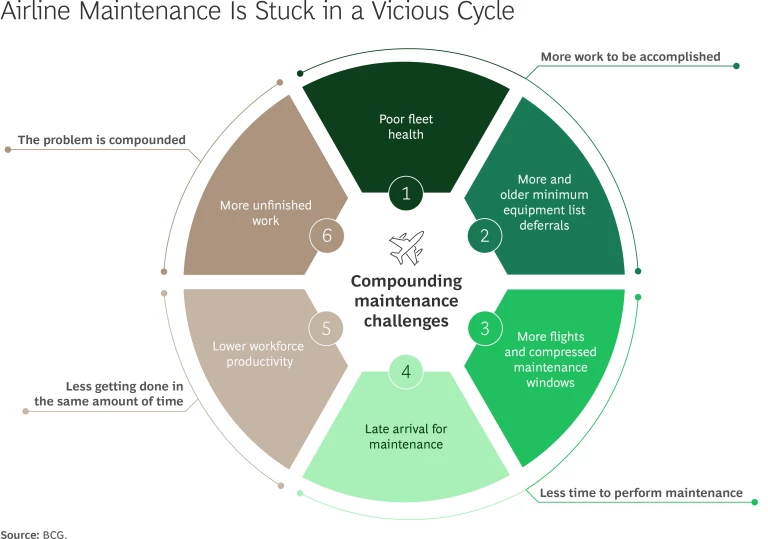
As maintenance becomes more reactive, planning becomes increasingly difficult. Work is being assigned in shorter bursts, without the ability to properly sequence and optimize it across the network. As a result, maintenance planners are constantly firefighting rather than executing a well-coordinated strategy.
Breaking the Cycle: Strategies to Restore Maintenance Efficiency
We have identified six strategies that, when executed together, can meaningfully improve maintenance performance and help airlines break free from the current cycle of inefficiency.
Strengthen workforce training and retention. A skilled and experienced maintenance workforce is the backbone of airline reliability. To bridge the growing experience gap, airlines must invest in fast-track training programs that accelerate skills development.
Beyond formal training, airlines must ensure that supervisors spend more time mentoring technicians while they are working on aircraft. Administrative tasks often dominate supervisors’ schedules, limiting opportunities for hands-on coaching. By freeing up supervisors’ time for mentorship, airlines can improve efficiency and accelerate knowledge transfer. Pairing new hires with experienced mentors further strengthens this process, helping to retain valuable expertise as senior technicians retire.
Optimized shift scheduling is also critical. Without careful planning, shifts become imbalanced, with too many inexperienced technicians working at the same time. Airlines must prioritize experience-balanced scheduling to keep maintenance operations running smoothly.
A skilled and experienced maintenance workforce is the backbone of airline reliability.
Finally, technology can play a key role in fostering technician proficiency. AI-driven troubleshooting tools can help mechanics quickly diagnose and resolve complex issues, flattening the learning curve and significantly reducing the time taken up with troubleshooting. By developing and deploying these tools, airlines can boost productivity and ensure that less experienced technicians perform at a higher level sooner.
Enhance maintenance planning and execution. Effective maintenance planning is essential to maintaining smooth airline operations, reducing delays, and maximizing aircraft availability. Poorly coordinated maintenance tasks can lead to unnecessary deferrals, operational bottlenecks, and last-minute disruptions that affect both efficiency and the passenger experience. To enhance maintenance effectiveness, airlines must take a proactive approach in key areas, including the way they package tasks, manage deferred maintenance, and allocate work between line and base maintenance.
One key step is packaging overnight maintenance tasks more effectively. By bundling tasks strategically and aligning technician workloads, airlines can increase completion rates and reduce deferrals, ensuring that aircraft start the day flight-ready.
Another critical action is enhancing MEL and clearance procedures. When aircraft operate with MEL deferrals, they often face routing restrictions and operational inefficiencies, limiting scheduling flexibility. By improving MEL clearance rates—ensuring that deferred maintenance issues are resolved faster—airlines can prevent scheduling bottlenecks, reduce last-minute disruptions, and keep more flights on schedule.
In addition, airlines must optimize task assignments between line and base maintenance to reduce turnaround pressure. Not all maintenance work belongs in line operations, where time constraints are tight. By shifting certain tasks to base maintenance and making full use of available ground time, airlines can increase flexibility, minimize last-minute delays, and keep aircraft in top condition.
Improve maintenance station footprints and capabilities. The footprints of major carriers’ maintenance stations have often failed to keep up with the dramatic evolution of their fleets, fleet sizes, networks, and schedules. Many hubs and other key line stations are overburdened, and maintenance work is not always assigned to stations with the capabilities best suited to the task. There are several practical steps to better optimize the footprint.
First, airlines must rationalize their network of line maintenance stations by using operational data, flight schedules, and maintenance demand patterns to determine the best locations. Stations should be positioned to maximize maintenance output during available ground time.
Airlines should also reassess ground time requirements. The effort to maximize flight hours can lead to overly aggressive scheduling that leaves too little time for necessary maintenance. Finding the right balance between flying and scheduled maintenance will reduce unexpected delays and last-minute cancellations.
The capabilities at key line stations must also improve. Investing in better tooling, materials, and infrastructure will allow stations to handle more complex repairs on-site, reducing the need to send aircraft on to larger maintenance hubs.
Effective maintenance planning is essential to maintaining smooth airline operations, reducing delays, and maximizing aircraft availability.
Finally, aligning maintenance station capabilities and capacity with airline operations can reduce overreliance on hubs. A well-distributed, well-equipped maintenance network will enable airlines to resolve issues faster by leveraging specialization or matching capabilities with planned work.
Align engineering, reliability, and predictive maintenance. Airlines must ensure that engineering, reliability programs, and predictive maintenance work in unison rather than in silos. Coordination allows insights from real-world fleet performance to directly inform maintenance strategies, preventing reactive decision making and unnecessary downtime.
AI and machine learning can enhance this process. By analyzing vast stores of fleet and task data, airlines can evaluate the effectiveness of specific maintenance tasks—identifying what truly prevents failures as opposed to what adds unnecessary cost or complexity. With these insights, they can optimize maintenance programs to strike the right balance among frequency, cost, and aircraft availability.
Predictive maintenance is a key enabler of this shift. Airlines that leverage AI-driven analytics can anticipate failures before they happen, reducing unexpected out-of-service events without disproportionately increasing maintenance workloads.
Fix the parts supply chain. No maintenance strategy can succeed without the right parts in the right place at the right time. Yet parts shortages are now one of the leading causes of maintenance-related cancellations. To regain control, airlines must take a more proactive and resilient approach to parts allocation, stocking, and sourcing.
They should start by aligning parts distribution with fleet needs at each station, ensuring that parts are always where they are needed most. Another key step is stockpiling high-failure, high-impact components. Instead of relying solely on real-time sourcing, airlines must anticipate common failures and maintain strategic reserves to avoid costly repair delays.
In addition, AI-driven inventory tracking can help airlines predict supply gaps before they occur. By analyzing usage patterns and supply chain trends, predictive analytics can alert airlines to potential shortages in advance.
Diversifying suppliers is also essential. Many airlines are too dependent on single-source providers, leaving them vulnerable to delays and price volatility.
Tightly integrate operations and maintenance control. Airline flight operations and maintenance are deeply interconnected, yet often they are not sufficiently aligned. By integrating operations and maintenance control more tightly, airlines can improve decision making, enhance fleet availability, and minimize disruptions.
It’s essential to establish fully integrated operations control towers and centralized maintenance control centers that use AI and machine learning for real-time decision support. These systems can analyze aircraft status, maintenance needs, and operational constraints to help airlines make smarter, faster routing and repair decisions.
Real-time digital tracking across all maintenance operations is also critical. Many airlines still rely on delayed reporting, making it difficult to anticipate issues before they disrupt schedules. By implementing continuous, real-time visibility into maintenance status, airlines can proactively reduce out-of-service time.
In addition, improving alignment between maintenance teams and operations control ensures that aircraft routing decisions are optimized to match maintenance needs. Finally, introducing performance-based metrics will help drive accountability and efficiency. Clear KPIs focused on technical dispatch reliability, deferred maintenance rates, and out-of-service event reductions can provide the necessary structure to improve overall performance.
Restoring and enhancing airline maintenance efficiency and reliability are within reach. While there is no single solution, airlines can make meaningful progress by systematically addressing root causes and tackling each challenge in a structured, deliberate manner. Measured steps—whether optimizing workforce planning, leveraging predictive maintenance, or improving supply chain resilience—will drive continual improvement. Airlines that act now will not only stabilize maintenance performance but also set themselves apart in an increasingly competitive industry.