Why is it so hard for Western countries to build new nuclear power plants? After all, the need is great: Nuclear energy can be a key source of low-carbon baseload power to support the energy transition and increase energy independence. As a result, public support for nuclear power has increased in recent years. Meanwhile, China has managed to complete and commission more than 34 gigawatts (GW) of new nuclear power over the past ten years, with continuously improving time and budget performance.
In Europe and the US, however, no Generation III reactor has come online on time and within budget yet. The reasons vary. Some are typical of the problems many organizations encounter in completing major capital projects , such as poor project management and lack of collaboration among stakeholders. Others are specific to nuclear plants, including complex and immature designs and lack of the robust supply chains available to support this once-thriving industry.
If nuclear power is to support Western countries’ energy transition ambitions, project owners will have to drastically improve their capabilities in all these areas. In this article, we examine the factors that hold back efforts to efficiently build new large-scale nuclear plants and offer detailed suggestions for overcoming the challenges.
Power Failure
Recent efforts to build and commission nuclear power plants in countries such as China, South Korea, and the UAE have been completed far more quickly and efficiently than those in the US and Europe. (See Exhibit 1.) The first Hualong reactors, for example, were built in China in just six to seven years, and the UAE’s four Korea-designed APR-1400 reactors were built in less than ten years. In fact, the first UAE reactor, Barakah-1, started commercial operation just 12 years after the country’s publicly announced plans to study the peaceful use of nuclear power.
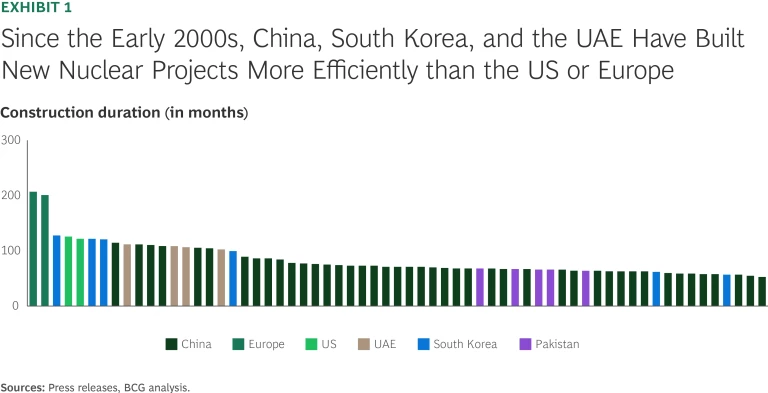
In contrast, recent attempts in the US and Europe have experienced extensive delays and overruns. Construction of the first EPR reactor at France’s Flamanville site began in 2007, with plans to start it up in 2012 at a cost of €3 billion. According to the French utility company EDF’s 2023 estimate, the reactor was connected to the grid in December 2024 at a total cost of €13 billion. While the initial estimates were arguably ambitious, if not impossible, to achieve for a first-of-a-kind (FOAK) project, the final cost is probably far more than it should have been.
In the US, construction on the third and fourth reactors at the Vogtle power plant in Georgia began in 2009, at an estimated cost of $14 billion. By 2021, the estimated costs had risen to more than $28.5 billion. Once both reactors were operational in 2024, the cost totaled $36 billion.
The causes of these time and budget overruns vary from project to project, but they can be grouped into three main types: structural factors, underperformance, and external factors. (See Exhibit 2.)
- Structural factors. These include the impacts the design will have on construction volumes and quantities (such as the volume of concrete or the number of valves) and the complexity and risks to be addressed during construction. Issues that are beyond the control of project owners, such as local labor laws and regulatory constraints, can also affect how projects are carried out.
- Underperformance. The bulk of construction roadblocks involve performance-related issues such as poor-quality construction or parts and low productivity. There can be a range of causes for these issues, including problems in specifications, manufacturing , and construction, all of which can be exacerbated by immature design and inexperienced suppliers.
- External factors. These cover further delays not directly related to execution of the project, such as lawsuits involving the project and disruptions such as the COVID-19 pandemic.
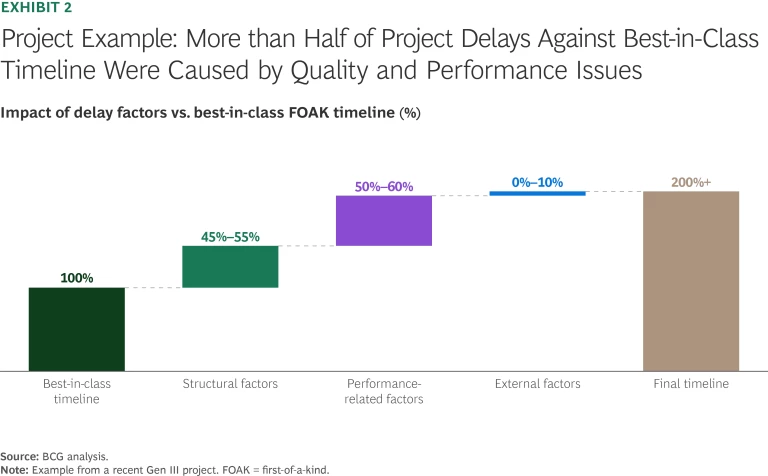
We believe there are four key factors that, if managed properly, can dramatically increase the speed and lower the cost of completing new plants and bringing the valuable power they generate to market. They include promoting design simplicity and maturity, supporting supply chain robustness, fostering stakeholder collaboration models, and securing strong and efficient project management.
Design Simplicity and Maturity
For nuclear facilities, the simpler the design the better. More complex designs make it more difficult to manage the project and meet cost and schedule ambitions.
Certain features of the design, for example, can lead to major differences in the associated bill of quantities of nuclear projects. The volume of concrete and the number of cables, pipes, and valves per megawatt-electric (MWe) in the bill of quantities for two major Generation III designs differed by a factor of two, with the inevitable impact on construction time and budget.
One solution is to take a “design-for-manufacturing” approach to the process of building reactors, which has delivered compelling results in other industries such as aerospace and defense . This approach is intended to optimize the entire design and construction process, including standardization of components and material needed and reductions in the number of construction steps required, promoting modularity.
Efficient design development can also be fostered with the deployment of agile development methods tailored to complex systems design. Success will be dependent on five imperatives:
- Optimize the initial architecture. Take the time needed, early in the process, to focus on the architecture of each product and system, even if it means delaying the start of the detailed design. An optimized architecture is driven by modularity, limiting interdependencies between its components and thus maximizing the ability to develop each one more efficiently. Remember: 80% of the success of any project depends on how well it is structured from the start.
- Focus on value. Pay close attention to what clients actually ask, while avoiding a deep dive from the start into hundreds of technical requirements. Doing so requires that 100% of the “client asks” be captured from the start, which typically results in around 40 high-level value attributes. These attributes must then be prioritized. This will help teams decide upfront where to start digging into the details and avoid working at too granular a level when the full specifications are not yet clear.
- Simplify the process. Progress incrementally through design development and testing, decoupling the design of subsystems to simplify the larger process. Conduct client demonstrations of results achieved, typically quarterly. This helps to proceed step-by-step toward the most economically viable design while focusing ruthlessly on value maximization: What matters most for clients comes first.
- Empower individual teams. Give each subsystem design team at the lowest levels of the organization the autonomy needed to make important decisions and design tradeoffs while ensuring consistency across the entire design. Maintaining consistency requires considerable effort. First, be clear upfront on the acceptance criteria for each upcoming increment of work, which will determine how to measure precisely that the job is done. Second, ensure full system integration at the end of each work increment, typically by incorporating model-based systems engineering and dynamic planning protocols.
- Track and engage. Monitor progress through regular touchpoints and ongoing testing of each element in the system. This should include involving contractors and construction trades early in the design and planning phases to ensure simplicity, constructability, and maintainability, while boosting the ability to integrate efficiencies from their experience with previous projects.
Agile development can have a tangible impact on the speed and cost of complex designs. We have seen 30% to 50% reductions in the time it takes to deliver complete designs, with a 15% to 25% decline in total development costs. Technical concerns can be detected months or even years earlier than with traditional design processes. Increased interactions with clients, both internal and external, help find solutions faster and overcome problems, and design teams are far more engaged in the process.
These agile development methodologies, while powerful, require a step-change in ways of working with nuclear safety authorities. Validating design changes through traditional waterfall cycles—from full specs to full development to full integration—is not compatible with agile development. Instead, safety authorities should be encouraged to carry out more frequent interactions, quarterly or even monthly, to both validate the most recent work increment and confirm acceptance criteria of the next increment.
It is also critical to ensure that the design is sufficiently mature before construction starts. Moving forward while significant uncertainties remain about the design is a recipe for delays and cost overruns. (See Exhibit 3.) It’s only a matter of time before construction progress outruns the design. This can result in construction and manufacturing teams having to redo what’s been done because of design changes, leading to additional material costs, and forcing other teams to pause their activities, creating excess lost opportunity costs and rework costs.
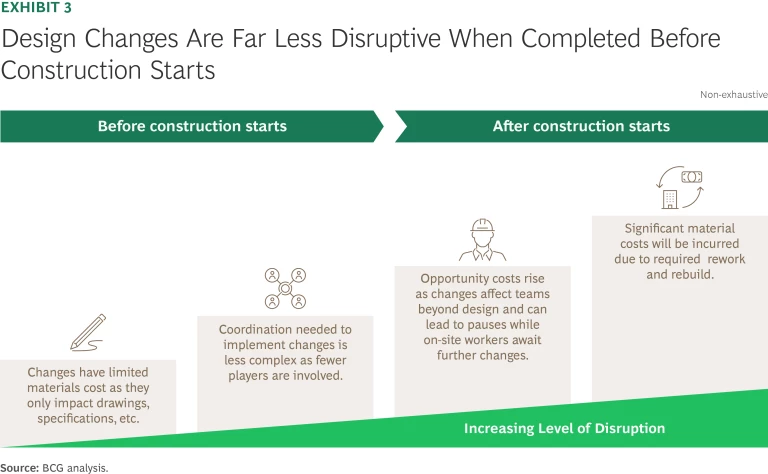
Design maturity can vary considerably across projects. While some projects poured the first concrete with around 80% of the detailed design ready to go, others have started with less than 40%. It will come as no surprise that projects with the highest design maturity have often shown far better time and budget performance. To ensure readiness, it is critical to impose stage gates that make sure construction does not move forward while design uncertainties remain. In addition, the robustness of the design must be regularly measured, and a well-designed change management process must be put in place to ensure the flexibility needed to handle the design changes that will inevitably occur.
Supply Chain Robustness
Among the causes of the delays and cost overruns at several projects was the lack of experience on the part of the many suppliers it takes to build a major nuclear power plant. The Flamanville-3 project in France was begun in 2007, eight years after the country’s last major project, Civeaux 2, was completed in 1999. In the US, 13 years passed between the completion of Watts Bar-1 in 1996 and the start of construction on Vogtle in 2009. The significant gap between these projects led to a loss of capabilities and limited supplier choices across the nuclear industry in both countries.
The experience of the supply chain supporting nuclear new builds can have a substantial impact on the overall performance of a project. Supply chain maturity matters because project management and oversight of construction activities isn’t just the responsibility of the project owner, but also of the project’s suppliers, beginning with the principal contractor and tier 1 suppliers. How this responsibility is allocated, however, depends on the robustness of the supply chain. Mature suppliers should be able to coordinate their internal activities, perform quality oversight, and manage their subcontractors, with the project owner supporting only the management of the various suppliers’ interfaces.
Given the current state of supply chains in the West, they will need to be nurtured during the course of each new project to support their development, and the process used to integrate each supplier effectively into the full project will depend on the maturity of individual suppliers and of the entire supplier ecosystem. Project owners must be ready to play a more engaged role in managing their suppliers’ activities. This includes active project management and quality oversight, including with tier 2 and lower suppliers, as well as supporting the growth and maturity of the suppliers so that they can progressively take over such activities.
Over the long term, supply chains can also be nurtured and maintained through the mobilization of public authorities and private players to provide visibility into future nuclear investment needs. Public authorities can play a key role in gaining insights into the overall industry by clarifying their general energy mix objectives and energy roadmap and, more concretely, by engaging in the planning of actual projects. A favorable regulatory environment that encourages the overall market for nuclear can also help encourage investments in the nuclear supply chain’s capabilities and workforce.
Subscribe to our Energy E-Alert.
Stakeholder Collaboration Models
Successful completion of a nuclear facility requires a collective commitment from all stakeholders, including the owner and the most strategic suppliers. A collaboration model reflecting the specific supplier expertise available must be designed to share the project’s risks and benefits so that all stakeholders—including the owner, developer, designer, builder, and suppliers—have “skin in the game.” This will ensure that the overall financial success of the project as a whole is more important than each stakeholder’s individual benefit. The UAE’s four Korea-designed APR-1400 reactors at Barakah, for example, benefited from the so-called “Team Korea”—an ecosystem of suppliers developed over more than 50 years—aligned around a common objective.
As such, contractual frameworks with builders, suppliers, and others should combine pricing strategies adapted to the project’s context, with strong incentivization mechanisms. These can range from motivation mechanisms offering future work, such as a series of projects and maintenance contracts, to hybrid incentives such as profit pools.
The Integrated Project Delivery (IPD) model is an example of a highly collaborative model being used in the construction of the first Western small modular reactor (SMR) in Darlington, Ontario, Canada. It relies on the involvement of all stakeholders as a joint steering group from the project’s inception. The IPD depends on three key principles: a so-called “best athlete” logic for determining the roles and responsibilities of each stakeholder; a joint model for risk sharing; and financial incentives designed to ensure success for all players embedded in a shared contract.
Risk-sharing is a necessary condition for successful collaboration, but it isn’t sufficient on its own. Creating a team spirit fostered by transparency and trust is key if stakeholders are to deliver the project on time and on budget. Doing so requires the implementation of tailored and agreed-on ways of working that concretely shape how stakeholders work together, including joint processes and methodologies, and information sharing. Project management must be clearly separated from any contractual issues that might arise to avoid getting caught up in a frenzy of claims and counterclaims that could disrupt the smooth completion of the project. The goal: to create a culture in which all issues are discussed openly in order to achieve the best possible solutions and outcomes.
It is also imperative to foster collaboration with local safety authorities. Safety will always be paramount, of course, but safety authorities should also work hand in hand with the project owner regarding project deadlines and costs. The Canadian SMR project offers a good example of pragmatic collaboration, with the Canadian safety authority making a point of stating its wish not to be on the critical path, but rather to work with the project owner to ensure its prompt completion.
Strong and Efficient Project Management
Without proper project management, no major nuclear power plant can be built efficiently. Factors include effective cost and planning management, a powerful and dedicated project team with the right delivery model, and the appropriate tools and data management systems. Yet few projects actually succeed in jointly securing these factors.
Effective cost and planning management
An all-too-common project pitfall is the desire to keep up the impression that the project is on track—initiating project phases simply because a milestone has been reached by a certain date, for example, not because the next step is ready to begin—to give external stakeholders a sense of progress being made. This practice can significantly disrupt projects, increasing complexity and adding to the workload needed to manage the extra interfaces and processes needed. This could potentially include yet more design changes during construction and additional construction steps that must take place under the especially stringent conditions of a plant already in operation.
To address this pitfall, the project team should provide an ambitious but realistic working plan to guide the suppliers’ teams while also providing a high-confidence plan to external stakeholders based on thorough risk analysis. The plan should pre-empt the need to publicly announce delays during the construction process, avoiding the disruptions that this would create on the construction site.
Strong project team
A project team must take control of the planning, design, and construction of nuclear new builds early in the process, with as much as a quarter of upfront funding devoted to project planning and workforce development. This should include mobilizing and training specific operational teams, engaging vendors, and developing preliminary budgets and schedules. This ensures that the project team is prepared to execute the project from the onset.
Past projects have suffered from overly centralized decision-making, leading to bottlenecks and delays in execution. To address this, it is critical that organizations include clearly defined responsibilities and accountabilities for decision-making. Otherwise, they run the risk of diluting accountability across teams and can suffer from the lack of a single point of decision-making and having to escalate every decision to the project’s top management, or making decisions without accountability for the full impact of potential quality, cost, and delay issues.
While the level of delegation given to operational teams for project decisions can vary depending on context—whether it is a first-of-a-kind or nth-of-a-kind project—operational teams should be empowered through incentives and accountability at the lowest level possible. Projects otherwise run the risk of creating high-level decision-making bottlenecks, while operational teams may lack a sense of ownership and responsibility for the timely and efficient delivery of the project.
Supporting tools and data management systems
Successfully steering the nuclear new build to completion cannot be achieved without data management systems that provide a high-quality “single source of truth” that is available to and usable by all project stakeholders, including local project teams and relevant suppliers. The systems should cover all key project information, including scheduling, change management, configuration management, construction progress, and tracking of open points.
Without master data management, poorly integrated systems can lead to multiple databases (including private Excel files on personal laptops), inaccurate or out-of-date information, and different versions of documents. This fosters the making of ill-advised project decisions based on incorrect information, such as initiating the closure of concrete shafts too soon or wrongly assuming all electric cables have been installed. And it can lead to a vicious circle of loss of confidence in central databases, the creation of yet more local databases, and the accelerating loss of overall data quality and reliability.
Sharing lessons learned across projects
To foster a culture of openness and collective sharing in the nuclear power sector, mechanisms should be established that require owners, execution partners, and OEMs to share honest lessons—and not just marketing materials—across projects and sites. This includes using general nuclear project insights from established industry groups (including lessons learned from past projects) and technology-specific lessons from owners who use the same designs.
Arguably, this level of sharing involves a step change in how many stakeholders—companies and governments alike—think about nuclear new builds. After all, the hard-won lessons learned during the course of a complex project are often viewed as highly valuable intellectual property. Nevertheless, sharing these insights is critical. Otherwise, organizations run the risk of repeating the same mistakes over and over, at a time when the industry as a whole needs to demonstrate quantifiable performance improvements if it is to foster the public acceptability and generate capital investments it needs to fuel its ongoing renaissance.
No nuclear construction project is exactly alike. Given the impact of local constraints, various supply chain starting points, and different designs and degrees of past experience, each nuclear new build encounters its own particular challenges, delays, and cost issues for a range of different reasons. And they must be overcome on a case-by-case basis.
In our experience, however, these difficulties arise for similar overarching reasons: an overly complex and immature design, a supply chain with limited experience and scale, a lack of collaboration among stakeholders or the right incentives to ensure the project’s success, and weak project management.
In this context, capturing lessons learned from past projects is key. It should be part of an upfront conversation between owners, designers, construction teams, and the broader supply base. This is inherently difficult, since individual construction teams obviously cannot be part of every new nuclear project, and because many view the construction methods and lessons from their previous projects as core IP. Winners will have to find a way to solve such conundrums, either contractually or through alliances, for example.
Working on these common pitfalls greatly improves the chances of bringing nuclear new build projects to completion on time and at a reasonable cost. Success, in turn, will help boost the share of power from this critical low-carbon source, which is key to the ongoing energy transition and to increasing energy independence.