Digital transformation is poised to promote a new era of growth in North American rail freight transport . The adoption of advanced tracking devices—known as telematics—has the potential to produce vast amounts of data on railcar location, condition, and health. Applying this data to improve the customer experience will help the rail industry grow its freight volumes after a decade-long decline in market share.
Leading industry stakeholders have formed a coalition, called RailPulse, to provide the shared infrastructure needed to capture, disseminate, and analyze data from telematics sensors. Application-layer developers will be able to tap into RailPulse’s data lake to provide shippers, railcar owners, and railroad operators with real-time visibility and insights to optimize their operations. Data-driven applications will augment the existing efficiency, sustainability, and safety benefits of rail shipping.
But realizing the full potential of telematics will require participation from across the industry. Shippers should explore the economic benefits of rail transport enhanced by data-driven visibility and insights. Railcar owners, railroads, hardware vendors, and application developers should collaborate to implement rail’s digital enhancements and create value. And all stakeholders can take steps to communicate the carbon-reduction benefits of shifting freight volumes from trucking to rail.
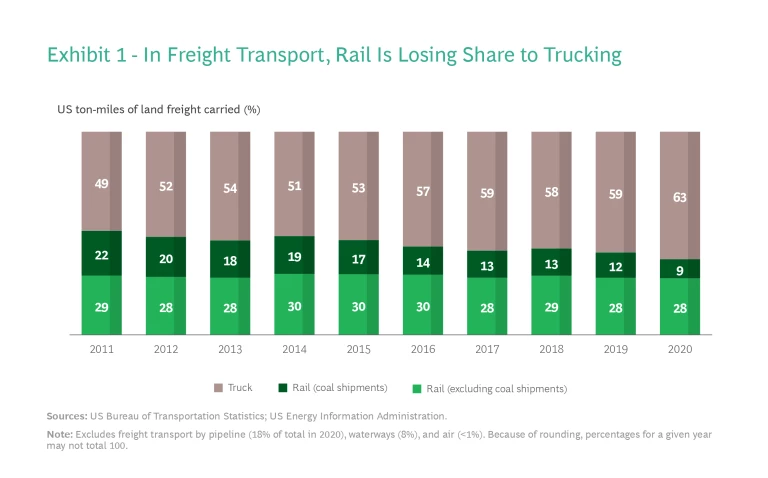
Freight Rail Is Losing Market Share, Despite Advantages
The rail industry’s struggles to maintain service levels as the US emerges from the pandemic have only aggravated the challenges that have suppressed its share of the land-freight market over the past decade or so. From 2011 through 2020, rail transport’s share of that market shrank from 51% to 37%, mainly owing to a sharp decline in coal shipments. In that same decade, truck transport’s market share grew from 49% to 63%. (See Exhibit 1.)
This trend underscores a more basic problem: many shippers view rail as simply too hard to use compared with trucking. A key advantage of truck transport is the ability to provide end-to-end shipping, limiting the need to coordinate first and last-mile handoffs. The trucking industry has increased this advantage by adopting untethered GPS tracking technology for trailers and containers, giving shippers real-time visibility into the location of shipments.
To close the performance gap and promote volume growth, the rail industry will need to relieve pain points experienced by participants across the value chain. (See Exhibit 2.)
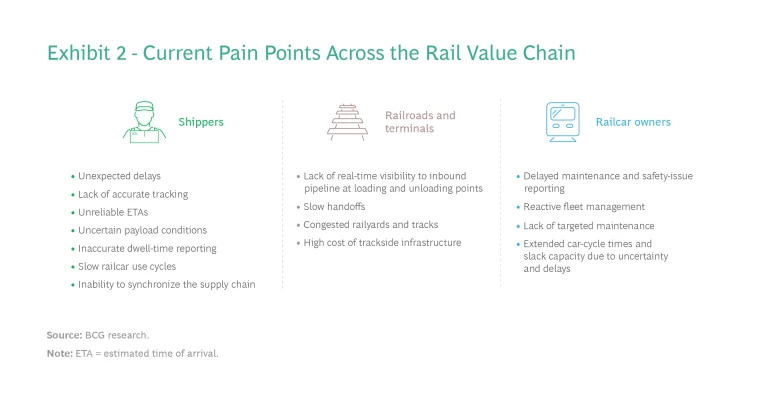
Shippers. In an age of nonstop, digitally enabled interconnectedness, rail transport often remains an analog experience for shippers. Supply chain managers may have limited, if any, visibility of the geographic location of their materials. The problem lies, to some extent, with the shortcomings of the Automatic Equipment Identification (AEI) tracking infrastructure used by North American railroads. There is considerable variation in the spacing of AEI readers across lines and regions. In some areas, the distance between readers is 50 miles or less, while in others they are hundreds of miles apart. Moreover, the system does not provide real-time location status—when railcars pass a reader, several hours elapse before updates appear in the system. Some areas lack tracking infrastructure altogether. At interchange points, particularly when cargo is moving from main lines to short lines, shippers typically lose the ability to track location.
The challenges arising from antiquated technology and fragmented data sources mean that supply chain managers must rely on estimated times of arrival (ETAs) based on data that is hours, or perhaps days, old. This makes it hard for supply chain managers to optimally coordinate last-mile logistics, which in turn undermines other efforts to achieve operational efficiency—such as scheduling production shifts according to when incoming raw materials are expected to arrive.
Railroads and Terminal Operators. Railyards and terminals are chokepoints in the rail network because managers lack real-time visibility of their inbound pipeline. This prevents them from using advanced planning to gain efficiency. Moreover, modal transitions are inherently unwieldy to manage—myriad shipments arrive from multiple directions and might be outbound via a truck, ship, or another train. The sheer complexity drives a significant gap in reliability. The planned movements of railcars might be delayed or eventually postponed, leaving them unprocessed in the yard overnight or perhaps for days, depending on several factors including frequency of service. Shippers know that railcars with their freight are heading towards them, but are unclear on how many will arrive and on what day.
Railcar Owners. Railcar owners—whether shippers, railcar lessors, railcar pool operators, or railroads—find it difficult to manage their fleets. Limited data on railcar utilization, location, and availability prevent greater precision in forward-looking fleet management. To absorb variances without sacrificing operations, owners must maintain significant slack capacity. And despite trackside infrastructure intended to sense potential maintenance issues, such problems can go unnoticed until they fully manifest, leading to unplanned downtime and costlier repairs. Even worse, potentially dangerous car conditions—such as excess pressure or temperature—may go undetected until accidents happen.
These pain points undermine what could otherwise be a desirable mode of freight transport. In fact, rail transport has several advantages that make it well suited to helping shippers meet the challenges of today’s economy:
- Efficiency. With extensive networks and trains that can carry the equivalent of hundreds of tractor-trailers, railroads can transport vast quantities of materials and products efficiently and economically. The significant cost savings give shippers opportunities to reduce the margin pressure caused by rising commodity prices and inflation. Depending on distance, payload, and cargo, the cost of rail transport can be 20% to 40% less than truck transport, according to the Journal of Commerce.
- Sustainability. The carbon footprint of rail shipments is 75% lower than that of truck shipments, according to academic and industry studies.
1 1 Texas A&M Transportation Institute, A Modal Comparison of Domestic Freight Transportation Effects on the General Public: 2001–2019, 2022; Association of American Railroads, Freight Railroads & Climate Change Policies, 2021. - Safety. Compared with trucking, freight rail transport is safer for society. Studies by the Texas A&M Transportation Institute have found that rail-related fatalities are almost five times lower per ton-mile transported, while the injury rate is twelve times lower. In addition, rail transport’s lower pollution rates make it better for public health.
Shifting freight volumes from trucking to rail could also benefit society by reducing road congestion and wear and tear on highway infrastructure—thereby decreasing government spending on maintenance.
The Opportunities: Transparency and Optimization
The rail industry is on the verge of a digital revolution that has the potential to fundamentally transform rail freight transport through unprecedented data-driven transparency and optimization. In doing so, it can solve the pain points that have impeded growth and enable more shippers to capture the advantages of rail transport.
The revolution begins with tracking technology. The technology required to implement telematics tracking devices for railcars is either available today or being tested in advanced pilot programs. These devices will soon be widely deployed to transmit critical data on railcar location, condition, and health to shippers, railroad operators, and railcar owners. (See the sidebar “Railcar Sensors Are Already Available, and Many More Are Coming.”)
Railcar Sensors Are Already Available, and Many More Are Coming
With the right infrastructure, analytics, and interfaces in place, these parties can use the data to optimize their operations. And society will benefit from a greener mix of freight transport and improved safety. (See Exhibit 3.)
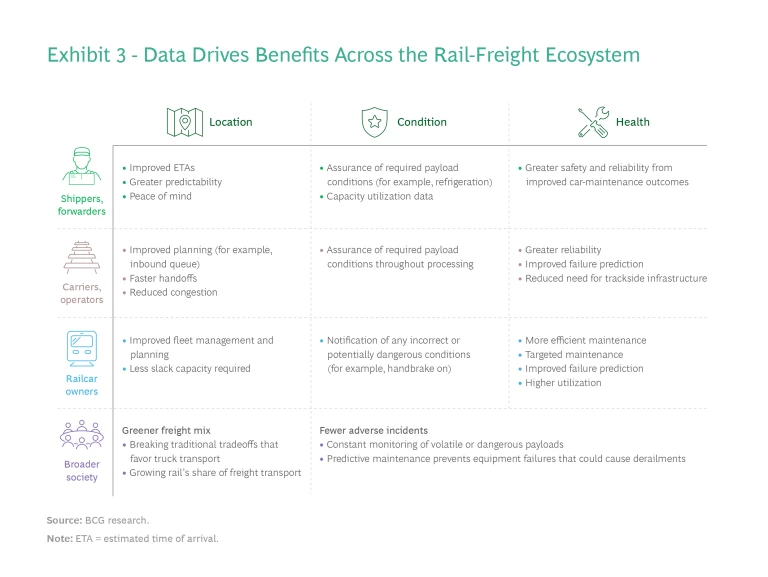
Location. Telematics devices that use GPS technology are currently available to transmit real-time information on train location. The information is more accurate and more frequently updated than that provided by trackside infrastructure. Once all fleets are equipped with these devices, coverage will be truly end-to-end—extending beyond the main rail lines to regional lines and yards where trains await processing.
With full deployment, shippers will gain greater transparency and far more accurate ETAs. They can apply the information to improve shipment management and operations, reduce cycle times, and synchronize their supply chains from end to end.
For railroads and operators of railyards, terminals, ports, and other modal handoff points, widespread adoption of telematics will allow for advanced visibility of the inbound pipeline as well as live in-yard location tracking. Operators can apply this visibility to optimize or even automate pipeline planning and receive AI-generated recommendations for sequential car movements. Digital twins—digital visualizations of highly complex operations—will facilitate these efforts.
Railcar owners will gain a far more accurate and up-to-date view of their fleet. They can apply this visibility to improve fleet management and, in time, may be able to reduce the need for slack capacity.
Condition. Other telematics hardware will transmit data regarding the condition of a railcar to stakeholders. This can assure a shipper that its payload has not been accessed via an open hatch by unauthorized parties, and that it is being kept at the required temperature or pressure if it is refrigerated or volatile. Condition data will enable automated corrective actions and dispatching of emergency personnel—fire, police, or medical—as the situation warrants. As more sensors become available to provide data from additional sources, companies will undertake even more valuable optimization efforts, such as improving car capacity utilization.
Health. Using telematics to report on railcar health is particularly valuable to railcar owners, who currently may only be able to perform occasional detailed checks on their equipment. Sensors will provide real-time visibility of damaged parts. Railcar owners will apply condition data to automatically schedule maintenance, including prioritization based on urgency. They will use machine learning to sense possible failures before they happen. This enables far more efficient, targeted, and predictive maintenance while improving reliability and dramatically reducing maintenance costs. Class I railroads also benefit, as they will no longer need to maintain trackside infrastructure for sensing maintenance issues and will gain more detailed visibility.
The Key Enablers: A Shared Data Ecosystem and Application Layer
Today, the transformative benefits of data collected by telematics devices are largely theoretical. To make them a reality, rail freight industry stakeholders must act collectively. Otherwise, industry participants could end up using dozens of incompatible sensors, each with its own data currency and standards, none of which can communicate with each other or a common data repository. Moreover, to go beyond mere visibility and capture the full benefits of optimization, the industry needs application layers that tap into a common data repository to provide customers with analytics and a visualization platform.
A Secure, Cross-Compatible Ecosystem
The industry needs to create a secure, cross-compatible ecosystem to prevent the proliferation of different standards that would hamper the digitization of rail and ultimately harm the industry. The RailPulse coalition of railcar owners (including lessors, shippers owning their own fleets, and Class I and short-line railroads) seeks to provide this ecosystem. The coalition’s objective is to set standards for telematics—including hardware, compatibility, and other specifications—and to identify technology vendors. It will also provide infrastructure to collect, harmonize, aggregate, and store railcar data.
As David Shannon, RailPulse’s general manager, explains: “Very simply, telematics technology is coming whether RailPulse exists or not. Without RailPulse, it will come in many different ways, with owners and operators each doing their own thing. Instead of the industry working together with a shared data set, its actors will be using the technology as a weapon against each other. We want this technology to be used collaboratively to benefit the entire industry.”
Current members of RailPulse are GATX, Genesee & Wyoming, The Greenbrier Companies, Norfolk Southern, Railroad Development Corporation, TrinityRail, Union Pacific, and Watco. TrinityRail CEO Jean Savage emphasizes that the coalition’s central focus is to seek products and services to improve the customer experience. “Our guiding question is, ‘What can we take to our customers to make their lives easier and better?’,” Savage says. “This customer-centric approach has started to reach all ecosystem members.”
The RailPulse coalition will make key data visible across industry participants.
Crucially, the coalition will make key data visible across industry participants. An initiative by TrinityRail has demonstrated the benefits of cross-party visibility even before the rollout of cutting-edge telematics. Traditionally, each railroad has provided ETAs to customers using AEI data solely from its own infrastructure. To gain a cross-industry perspective, Trinity developed an ETA prediction model that draws upon AEI data from all railroads. Trinity found that its model based on cross-industry data reduced the difference between predicted and actual ETAs by 25%, on average. The huge improvements in ETA accuracy from visibility across companies are promising and foreshadow the expected dramatic improvements from an upgrade to telematics.
Building on the industry’s existing capabilities is a key component of RailPulse’s strategy. Earlier this year, RailPulse announced a partnership with Railinc, a subsidiary of the Association of American Railroads that offers a variety of products and services to simplify administrative tasks. The RailPulse ecosystem will benefit from Railinc’s experience processing and safeguarding vast amounts of data and interacting with rail industry participants. Among its services, Railinc provides location data sourced primarily from the Car Location Message (CLM) system. Using GPS and telematics infrastructure will allow RailPulse to improve upon the offering associated with legacy data sources, such as the AEI and CLM systems, by providing real-time location updates, including from railyards and shippers.
As RailPulse evolves, it will establish the integrated ecosystem of technology necessary to provide key benefits across the value chain—including transforming how different parts of the value chain interact with one another. By aligning on standards for future technology and data, RailPulse will enable the adoption of telematics that can provide a far wider breadth of data at a much more granular level than legacy sources currently offer. The ultimate outcome will be a fully end-to-end solution that simplifies rail shipping.
A Transformative Application Layer
Collecting data and ensuring its compatibility across stakeholders is only the beginning. To create value for rail customers, stakeholders need to apply the data effectively.
This requires an application layer that utilizes techniques such as machine learning and predictive analytics to help companies improve operations and reduce costs. (See the sidebar “Telematics Applications in Action.”)
Telematics Applications in Action
Fleet Management Dashboard
Problem: The coordinator of a paper company’s railcar fleet spends three hours a day searching multiple railroad websites to determine the current location of the railcars.
Solution: A telematics-enabled dashboard shows the location of the railcars. The dashboard auto-refreshes every five minutes to provide updated information and facilitate planning. The fleet coordinator can redirect his time from gathering data to solving problems.
Self-Service ETA Dashboard
Problem: A customer representative at a large chemicals company spends most of his workday fielding questions from customers about the ETAs of rail shipments.
Solution: A dashboard designed for recipients is a self-service tool for checking ETAs. The ETA estimates are provided by artificial intelligence and refresh automatically.
Data Consolidation Platform
Problem: A logistics broker must go to the websites of multiple third-party logistics companies and GPS providers to access location information and ETA estimates.
Solution: A next-generation telematics application consolidates all data sources in one platform for ease of use and accessibility.
Tamper-Detection Sensors
Problem: A food processing company’s head of security, primarily concerned with safety and chain of custody, needs to review online data to spot-check car movements and investigate incidents.
Solution: GPS and tamper-detecting sensors send automated alerts if railcar doors are open inappropriately and provide proof of incident-free delivery.
Temperature Sensors
Problem: The manager’s team at a receiving terminal for refined fuels needs to heat railcars so the fuel reaches the optimal viscosity for unloading. However, the team must avoid overheating the cars and damaging their lining.
Solution: Temperature sensors can measure the fuel’s temperature so the heating process can be performed efficiently and safely. The data also provides evidence to refute any claims that the product or railcar has been damaged.
The base data is bound to be commoditized as market entrants access the data lake provided by RailPulse. That means the real value-creation potential will come from the application layer, where analytics and software are the differentiators for customers. Because the application layer will be the new customer interface, it must meet a high standard; indeed, given the potential for cost savings and reduced carbon emissions from shifting more land freight to rail transport, the application layer will be the hub for value creation in the industry.
RailPulse will soon be giving application-layer developers access to its data lake so they can provide real-time, end- to-end location, condition, and health data to shippers, railyard managers, and railcar owners. RailPulse will also enable other providers of real-time visibility and analytics to participate in the ecosystem. (All parties, of course, will require appropriate authorization from individual car owners to access their data.) Expect traditional providers of rail-tracking data—such as RSI Logistics, Quality Logistics, and IntelliTrans—to tap into the new telemetry data and expand their offerings to build on their existing customer bases. “RailPulse can be the single source of truth for railcars in the industry by merging the new telemetry data with existing types of railroad data,” explains Shannon.
New applications that leverage real-time, end-to-end location and related information are coming to market. We spoke with shippers using the Trinsight logistics platform, a platform launched by TrinityRail that combines traditional industry location information with newly available advanced datasets. These discussions provide insights into the transformative potential of such applications, of which Trinsight will be just one of many available to shippers. (See the sidebar “Voice of the Shipper.”)
Voice of the Shipper
The Mosaic Company
The Mosaic Company—the largest US producer of potash and phosphate fertilizer—makes considerable use of rail freight and manages its own rail yards. The company’s railyard management system entailed a significant amount of manual data entry relating to railcars’ availability, cleaning status, and inspection status. The company also manually tracked the number of “bad order” cars—that is, those awaiting or undergoing repairs. Staying current required constant input from crews around the yard.
“We didn’t have the complete visibility to aid in executing our daily plan,” said David Kirkpatrick, the company’s senior manager of rail transportation. “We hoped that telematics would allow us not only to eliminate manual data entry but also improve a variety of yard-management metrics.”
The company used the Trinsight logistics platform to implement a digital replica of its railyard. This digital twin enables yard managers to keep closer track of every car’s status and location and optimize operations.
“Since implementing the digital twin solution, we can see that the velocity of cars is improving,” says Kirkpatrick.
Beyond moving cars around the yard faster, Mosaic also saw improvements in several other performance measures, including reductions to the bad-order count and a decrease in dwell time.
Western Canadian Shippers’ Coalition
The Western Canadian Shippers’ Coalition (WCSC) is an industry group whose constituents collectively ship billions of dollars’ worth of cargo domestically and internationally. As the organization’s president, David Montpetit is deeply familiar with the status and potential of digitization in freight rail transport, as well as shippers’ pain points and expectations.
“Digitalization within the rail sector is still in its infancy,” he says. WCSC is among the early adopters. It has partnered with TrinityRail to stand-up performance dashboards that industry constituents can apply to make informed supply chain decisions and identify areas of opportunity.
Telematics is the ‘missing link’ that connects supply chain, production, and shipping models.
According to Montpetit, the first pain point that can be solved by digitization is a lack of information. Shippers that have GPS capabilities and automated alerts enabled by geofencing now have their own robust, real-time data and no longer must manually piece together location data from multiple sources. “Given the scope of the benefits, digitization is a huge priority for my organization,” he says.
Visibility is only the beginning. Montpetit sees a future in which shippers’ data systems fully integrate dynamic ETA data enabled by telematics. “Telematics is the ‘missing link’ that connects supply chain, production, and shipping models so that rail freight can move smoothly.”
The potential climate benefits add to the urgency. “Shippers are under a lot of pressure to reduce their carbon footprint,” Montpetit says. By implementing digital solutions to improve the customer experience, railroads could make it more feasible for shippers to gain the environmental benefits of rail transport versus other modes, such as trucking.
For these reasons, among many others, Montpetit’s industry constituents are pressing for service improvements. “There has to be a greater sense of urgency across the board to broadly roll out the benefits of telematics for shippers.”
Overcoming the Barriers to Digital Adoption
Better mobile connectivity, a new customer-centric mindset, and collaboration among participants are overcoming the traditional barriers to digital adoption in the rail industry.
Better Connectivity. The continued 5G rollout across North America is improving mobile connectivity. This is making it possible, and increasingly affordable, for sensors, railcars, and control centers to communicate seamlessly even across remote stretches of the railroad network.
Customer-Centric Mindset. Over the past two decades, the North American rail industry has emphasized innovating to improve operational efficiency. That focus made sense for railroads, which until a decade ago were maintaining freight share. It also worked for key customers, such as shippers of lower-value bulk commodities on main lines (for example, the coal industry), for which operational efficiency was a more pressing need than railcar-level visibility. For other customers, minimal visibility needs were already being met—for instance, unit-train shippers were satisfied with tracking locomotives and intermodal shippers could track their containers. Meanwhile, shippers that demanded better visibility could meet their needs by using truck transport with its more mature digital applications (albeit at a premium price).
In recent years, however, the customer base has shifted toward shippers with higher-value goods, more complex supply chains, just-in-time delivery requirements, smaller payloads, and/or railcar fleets dispersed over main and regional lines. These shippers have greater needs and expectations for the customer experience with respect to visibility and reliability.
After recent supply-chain disruptions and a year of particularly low service levels in North America, rail industry executives understand that they must adopt a more customer-centric mindset to grow volume. They recognize that digitization will be essential to improving the customer experience and achieving growth aspirations.
Collaboration Among Industry Participants. The new emphasis on digitizing to improve the customer experience is reflected in the growing number of Class I and short-line railroads participating in RailPulse. The collaboration will help the industry overcome technological barriers and demonstrate a return on investment.
By developing shared standards and serving as a clearinghouse for data and permissions, RailPulse is providing a universal “plug-and-play” architecture for rail users and vendors. Additionally, it is utilizing an initial set of pilots, vendor vetting, and bulk purchasing to jump start the use of sensors while keeping costs low and promoting supplier competition.
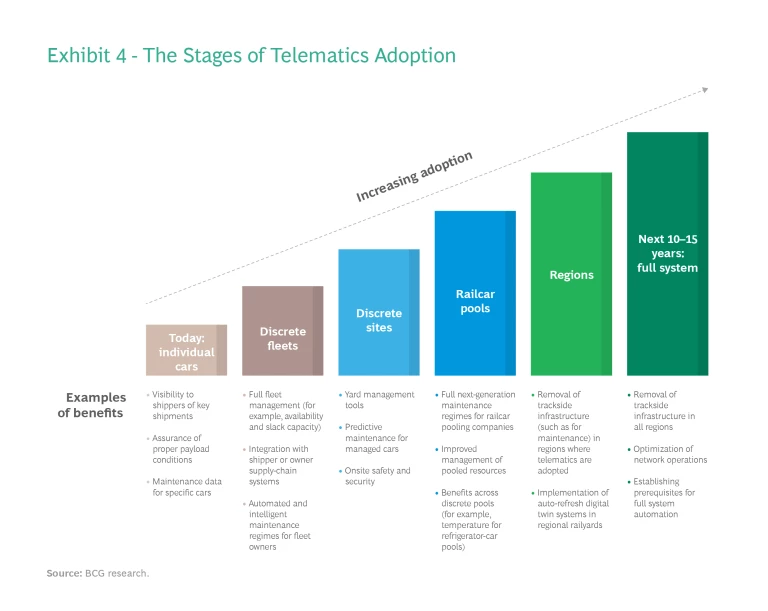
Early trials and proof-of-concept pilots are demonstrating the return on investment in telematics and laying the groundwork for wider adoption, flatter learning curves, and greater demand from shippers. As adoption increases, companies will capture benefits that require critical mass—such as improving the management of railcar fleets or pools or eliminating the burden of having trackside maintenance infrastructure—allowing them to create additional value. (See Exhibit 4.)
The result will be a virtuous cycle. Continued adoption by users with the greatest need and sophistication will increase incentives for technology providers to offer the application layer that transforms data into insights for optimizing operations. In turn, as greater scale increases the value of benefits, other industry participants will be motivated to invest in digitization.
Accelerating Adoption Across the Value Chain
By preparing for this digital revolution, shippers and other rail industry stakeholders can accelerate adoption and enhance the value created.
Shippers. Current rail customers should continue to press railroads to give them better visibility and insights. This could include, for example, access to RailPulse equipment and the necessary analytics platforms. Shippers not currently using rail transport should reconsider using rail to capture the benefits of safety, efficiency, and sustainability as enhanced by telematics.
To prepare for discussions with railroads, shippers should explore the potential economic benefits of digitization for their own business, including the return on investment. Shippers can already access some digital insights, most notably real-time location data, from some railcars and suppliers. In the coming years, however, shippers will benefit from the technology and data standards set by RailPulse, including an expanded suite of sensor data (such as for monitoring on-board payload conditions and railcar health) across railcars participating in the coalition. By understanding the business benefits, shippers can also gain confidence to lease or own their railcars.
To realize value from rail’s digital innovation, shippers must raise the sophistication of their supply chain function. This includes installing tech-forward solutions (such as an adaptable enterprise resource planning system), hiring staff with skills to use digital applications, and retraining current staff. They also need to decide on their preferences for communication and data sharing (one-way versus two-way). As an alternative to maintaining in-house capabilities to use digital innovations, shippers could consider working with third-party logistics providers that have the required capabilities.
Railcar Owners, Lessors, and Class I Railroads. For these companies, accelerating adoption is crucial to growing freight volumes and winning back market share from truck transport. Actions include deeply understanding the benefits of telematics and collaborating with industry players to develop standards, applications, and interfaces (such as through participation in RailPulse). To demonstrate the benefits to shippers, the rollout of telematics should begin with high-value cars (for example, refrigerated cars carrying perishable goods), discrete fleets where utilization can be improved, or specialized fleets where condition and/or health visibility is critical.
Hardware Vendors. Providers of sensor hardware should continue innovating and can be assured that RailPulse supports an “open source” platform to accommodate new sensor and communications solutions. This digital revolution is still in its infancy and the potential exists for new types of sensors that can solve key pain points in railroad operations.
Application Layer Developers. Potential developers of the application layer include not only software companies but also railroads, railcar lessors and manufacturers, and third-party logistics providers seeking a new revenue stream. They will play a key role in ensuring that industry participants can extract value from the vast amount of data that becomes available instead of being overwhelmed by the abundance. To enable this, developers need a deep understanding of operators’ and shippers’ pain points. The applications designed to address customer needs should use cutting-edge analytics, such as machine learning, to maximize sophistication and value creation.
All Stakeholders. Finally, when weighing the benefits of telematics, all stakeholders should consider that shifting freight volumes from trucking to railroads can improve safety and reduce carbon emissions. Shippers must be able to measure the reduction in their carbon footprint, identify the potential for further improvements, and share this information with their shareholders, customers, and the public. To accomplish this, shippers will need to build new or additional analytics capabilities and, potentially, implement a new approach to data management. To facilitate sustainability analysis and reporting, other rail industry participants must be able to furnish the required data with the appropriate granularity, frequency, and accuracy.
The stars are aligned for the rail freight industry to reclaim market share. The benefits of rail transport are especially valuable for shippers today, while imminent digital innovations promise to ease longstanding pain points for all stakeholders. Railcar owners, railroads, and other industry participants have abundant incentives to join forces to accelerate the adoption of these innovations. Simply put, now is the time to bring more freight volumes off the asphalt and back onto the rails.
BCG prepared this publication in collaboration with TrinityRail. The authors thank the company’s leaders for contributing insights into the rail industry and telematics technology, facilitating discussions with their customers and the leaders of the RailPulse coalition, and providing data for analysis.