The following insights are part of BCG’s Build for the Future series, based on three years of research conducted on digital transformations at major organizations around the world.
The supply chain has become a leading topic of boardroom discussion, amplified by pandemic-related raw-material shortages and cost increases. Simultaneously, CEOs have been speaking to investors about the supply chain, not only as a potential source of risk but also as a driver of innovation and competitive advantage. These conversations are inspiring many companies to bet big on the supply chain of the future—investing in digitization, resilience, and sustainability. Those that succeed will build supply chains that can withstand a variety of disruptions and lead the way to the future. (See “Build for the Future.”)
Build for the Future
Our latest survey asked all participants about:
- Five areas that are fundamental to success
- The emphasis of transformation efforts
- How successful transformation efforts have been
- The degree to which each of more than 50 potential influencing capabilities were in place
From this research, we identified the path that companies must take to become built for the future. We’ve reconciled the challenge of what these companies need to do (identifying which initiatives drive the most value by sector) with the challenge of how to do it (determining which capabilities drive success and how to build them fast). CEOs can tailor this new playbook to their company-specific change agendas. Learn more about our Build for the Future campaign here.
Successful supply chains will be able to withstand a variety of disruptions, such as fluctuating demand, high interest rates, trade actions, natural disasters, and labor shortages. They will weather micro trends around make-versus-buy decisions, internal risk assessments, internal digital maturity, and vendor partnerships. And they will spur innovation, inspire new business models, and provide significant competitive advantage. Here’s what our research shows.
- The supply chain is one of the biggest cost drivers in capex-heavy industries such as health care, industrial goods, consumer packaged goods, and energy; therefore, it holds tremendous potential for unlocking value.
- Three key components spell future success for supply chains: digitization (including AI and machine learning [ML]), resilience (the ability to both absorb shocks and recover quickly), and sustainability (including ESG and net zero commitments). Nonetheless, traditional supply chain priorities such as cost reduction, agility, and service quality remain vital to success.
- Digitization is especially important for companies looking to become supply chain leaders, and they must overcome barriers to scaling that effort. Many companies invest heavily in an AI and ML transformation but fail to fully realize its potential value at scale. In addition, advanced companies are rapidly adopting generative AI for use cases throughout the supply chain.
- The resilient supply chain requires a comprehensive program to better handle shocks. Such a program comprises network and product design, sourcing strategy, and planning. And it must be able—through monitoring, prediction, and crisis response—to move quickly when disruption occurs.
- Supply chains are essential to ESG and net zero commitments. Eight of the world’s aggregated industry supply chains are responsible for more than 50% of global carbon emissions.
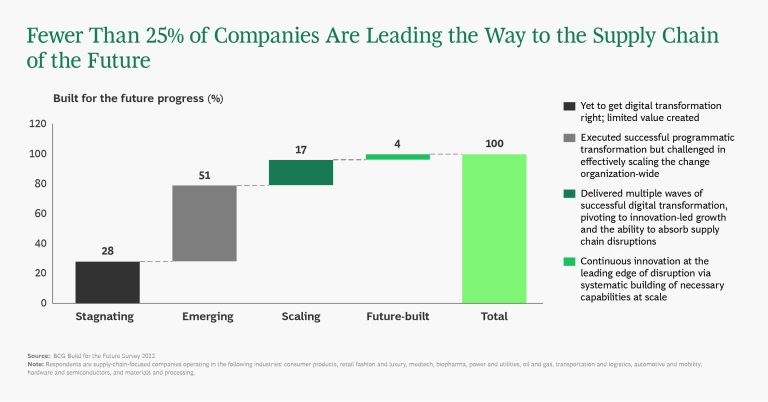
By the Numbers
Building a future-ready supply chain is a complex, multilevel process. As the exhibit shows, relatively few of the companies we analyzed have made substantial progress on that journey.
The Steps to Supply Chain Leadership
To create a digitized, resilient, sustainable, and cost-effective supply chain, businesses need to further invest in digitization in order to support agile decision making and adaptability through tools such as AI and machine ML. They should create a sustainable supply chain that meets the demands of today’s universal humanitarian challenges. And they should always keep an eye on costs, reducing them throughout the transformation where possible.
Build foundational capabilities. Organizations at the beginning of their journey must first create a data-driven supply chain strategy. They should start with a diagnostic of the supply chain—focusing on its financial and operational performance and including internal and external benchmarking exercises that use best-in-class examples where available. The results will help them set targets and then define and prioritize next steps. As a key part of this process, organizations should identify use cases that will generate strong value and develop new digital ways of working—including the hiring and training of digital talent.
Develop a digital ecosystem. For those further along and beginning to scale the transformation, we recommend developing a data-driven supply chain ecosystem. Supply chains are complex, and the optimal ecosystem should feature extensive collaboration among internal and external stakeholders. The development of digital channels within the supply chain will greatly support that collaboration; these channels should also create 360º visibility into all aspects of the value chain by aggregating data from across the ecosystem.
Innovate continually. As companies progress from scaling their digital transformation to creating a truly future-built supply chain, we recommend building a decision intelligence system. Such a system would use AI and ML to absorb data and patterns. provide recommendations, and support rapid decision making—thereby helping to ensure a resilient and sustainable supply chain.
Real-World Examples of How Successful Supply Chains Were Built
Meeting Critical Demand. A global medtech business saw exponentially increased demand during the pandemic for some of its key products; consequently, it needed to scale production quickly. But limited visibility into raw-material inventory and inventory at its tier one suppliers and contract manufacturing organizations restricted its ability to do so. The company clearly needed both risk alerts about potential supply bottlenecks and constraints and real-time visibility.
Three control-tower-enabled solutions provided the solutions. The business now receives smart alerts based on demand signals and bill of materials expansion, allowing it to optimize component allocation and generate a 12-week forecast for any production-limiting elements. And it incorporates the sales and operations planning data of tier one suppliers into its own data, generating visibility into potential constraints.
Managing a Complex Production Network. A large industrial goods business faced siloed operations between teams that were located in different places and had different priorities. The result: excess inventory, service challenges, and production losses across the network. The company resolved the issue by creating “digital twins” that provide a detailed digital representation of all aspects of the supply chain along with a simulation of full system flows (up to 12 weeks in advance) and a menu of mitigation actions.
As a result, the company now has advance data about potential congestion, production losses, stock reductions, and personnel needs, allowing it to make better-informed decisions and receive AI-based decision support as required.
Learn More
The slideshow below describes what it takes to build a future-ready supply chain.