The Middle East is among the world’s fastest growing regions economically, with many ambitious infrastructure and development projects forecasted to attract close to $1 trillion in investment by 2030.
Most real estate developers today still view transformational sustainable practices as economically unattractive, but the work BCG has conducted with large-scale urban regeneration projects in the Gulf Cooperation Council (GCC) region has shown just the opposite. Almost half of a project’s carbon abatement practices can create cost savings or are zero cost—and innovations such as biogenic construction technologies are emerging to solve the most difficult abatement issues.
Focusing Abatement Efforts
Our work on a recent large-scale real estate decarbonization strategy began with a detailed baselining of the project’s environmental footprint across the different asset categories, including buildings, road infrastructure, landscaping and water features, and utilities. (See Exhibit 1.) The baseline was conducted over the full lifecycle of the development, accounting for design, five years of construction, and 50 years of use, including the end-of-life of the project. Our work identified the overall footprint across Scopes 1, 2, and 3 to provide a holistic picture. Frequently developers only focus on Scopes 1 and 2 (direct and indirect GHG emissions that occur from sources controlled or owned by the project—such as burning natural gas on-site vs. purchasing electricity), while a large part of their footprint is located in Scope 3 (emissions linked to the project’s activities, but from sources in the supply chain not owned or controlled by it).
Two insights emerged from our analysis. First, in terms of asset categories, we found that buildings account for the lion’s share of emissions at about 66%, while landscaping and water features account for 20%. Second, in terms of lifecycle assessment, we found that the manufacturing of construction materials (i.e., embedded carbon), and operations and maintenance account for about 90% of lifetime emissions—approximately 25% and 65%, respectively.
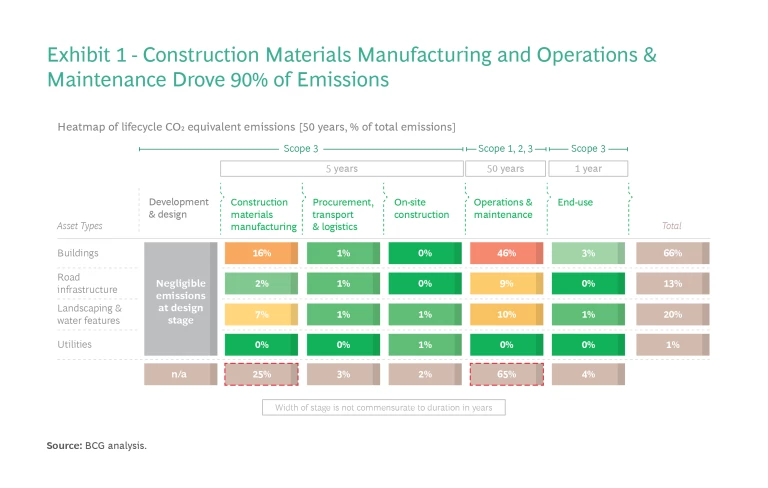
Unfortunately, manufacturing construction materials is among the most difficult carbon-emitting activity to abate because GHGs are still a fundamental part of the process (such as CO2 released from limestone used in cement production ). Meanwhile, electricity consumption accounts for a hefty proportion of operational emissions—but is only partially within a typical project owner’s control since it is still very much dependent on the power generation mix within the region or country.
But there is good news. Indeed, the economics of decarbonization in the region are encouraging and rapidly changing for the better. During our conversations with several regional material manufacturers, we learned that their investments in decarbonization-related technologies are beginning to pay off. Demand for greener construction materials (such as recycled steel, low-carbon cement, and low-carbon aluminum) is growing, and the price premium these materials command today is rapidly declining. For instance, Emirates Global Aluminum, a regional aluminum producer, has developed solar-powered aluminum smelting and won multiple contracts for its sale, including the sale of 40k tons of renewable aluminum to BMW Group in February 2021.
The First 50% Is Almost Free
The implications for the abatement efforts of mega projects are not theoretical. In a large-scale regeneration project in the GCC, the project owner managed to abate about 52% of GHG emissions even within the constraints of the project design, which had been mostly finalized by the time of our analysis. Had design incorporated green best practices from the start, we estimate the project could have abated 70% of GHG emissions. (See Exhibit 2.)
Here’s how we get to that 70%. Developers can abate approximately 37% of lifecycle carbon emissions using technologies and design principles that actually generate cost savings over a 50-year lifecycle. For example, savings in power consumption are possible using passive design principles, such as building orientation on the site, building layout, window design, insulation, and ventilation. Using mature technologies, such as replacing traditional lighting with LEDs or using smart thermostats, provides additional savings by reducing the overall cooling load in buildings.
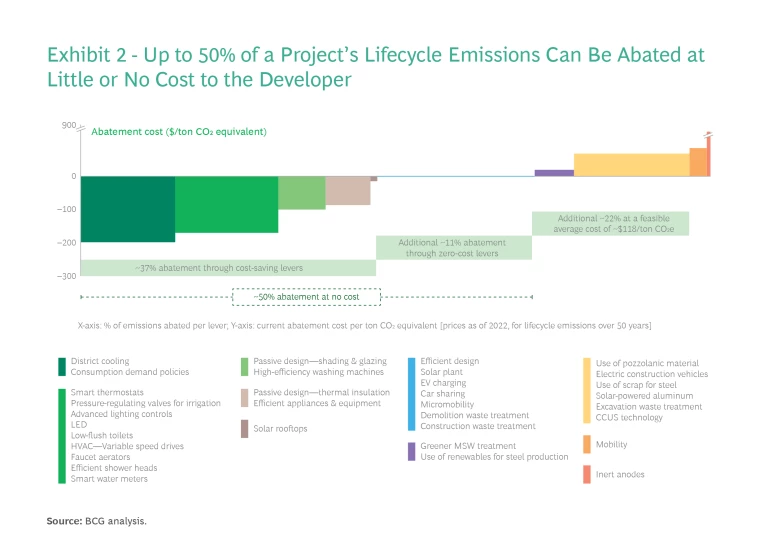
Moreover, the Middle East has yet to fully tap into the huge potential for district cooling. The technology, which relies on a centralized cooling plant to circulate chilled water to cool buildings, is 50% more energy efficient than traditional decentralized heating, ventilation, and air conditioning (HVAC) units. District cooling is a very feasible option for large-scale developments and has already been used in many master-planned GCC developments (including Business Bay, Dubai Downtown, Festival City in Dubai, and The Pearl Qatar). The scale of upcoming mega-developments could provide that extra push to make district cooling a standard for new projects.
In addition to the 37% of emissions abated through cost-saving levers, another 11% of abatement levers costs the developer little to nothing. Examples include greater use of solar power (such as leasing available land to solar plant operators for a lifecycle of 25 years, a common practice in mega-developments,) and incentivizing greater electrical vehicle (EV) adoption with a well-designed charging network.
Getting Closer to Zero
Beyond the first 48% of emissions abatement described above, costs begin to rise. Our research shows that the next 22% is economically feasible at an average price of ~$118 per ton of CO2e
In the short term, the costs of these green technologies might seem to outweigh their benefits, but we expect them to become increasingly cost competitive in the next five to seven years. Indeed, other factors could make additional abatement measures financially feasible in the more immediate future. Green buildings, for example, can directly contribute to the top line of developers, particularly in commercial real estate. A recent study by Knight Frank
On the funding side, it is also increasingly possible for sustainable developments to access financing earmarked for green/ESG-compliant projects, which can be 20–70 bps less expensive than traditional financing, according to a study conducted by finance company MSCI.
Looking to Biogenic Abatement Innovations
While the abatement levers discussed so far are possible within the current construction paradigms, getting closer to zero emissions will require that innovators test new solutions that challenge existing approaches. One particularly promising area is biogenic construction materials such as cross-laminated timber, bamboo, straw bales, and hempcrete.
In fact, some biogenic materials have been deployed successfully around the globe—and with increasing frequency. For example, the tallest mass timber building in the world, Ascent, opened in Milwaukee, in the midwestern US, in 2022. Glue-laminated timber beams and columns carry cross-laminated timber floors, with two concrete cores providing lateral stability. The 25-story mixed-use building is 86.6 meters (284 feet) tall, with a total floor area of approximately 45,800 square meters (493,000 square feet). It includes residential apartments, retail space, an elevated pool, and a sky-deck. All timber used in the structure was imported from Austria.
While wooden buildings are rare in the Middle East, the technology is highly adaptable to a wide range of weather conditions, including arid conditions. For example, The Beam on Farmer is a 17,000 square meter, five-story building completed in 2022 in the Southwest US city of Phoenix. The city has temperatures comparable to the GCC, with maximum temperatures of more than 54 degrees Celsius in summer. Buildings made of timber are beginning to appear in the GCC, including the first in the United Arab Emirates, the Skyway Innovation Center in Sharjah.
These are promising examples, but for widespread adoption to occur in the region, innovators will need to fight several preconceptions associated with timber, including fire resistance (ironically, timber structures suffer more from water than fire). At the same time, they will need to launch a completely new industry, one that can procure material at a competitive cost, identify capable contractors, and push for changes in local building codes. In terms of fire resistance, for example, there are precedents for ensuring timber has similar requirements as standard buildings. The good news is that the technology exists, but legislators and contractors will need to break free of established practices and actively support new and innovative building methods.
We expect these issues will be addressed and biogenic construction will become more prevalent in the region in the coming years, most likely in a hybrid form with traditional materials. What’s especially exciting is that because biogenic materials can store carbon, they can help reduce the overall carbon footprint of our planet. Someday these technologies might take buildings beyond carbon neutral to carbon negative, removing more carbon from the atmosphere than the buildings put into it.
Spurring Green Adoption
Decarbonizing mega projects is a challenge that requires the coordinated efforts of various stakeholders, including governments, developers, and material suppliers. The role of the government is essential in setting policies, building codes, and providing subsidies that incentivize sustainability—and many regional regulators are taking action. But private or semi-private entities can start driving change by developing full-fledged sustainability strategies for ventures, such as mega projects, that include some quick wins and some medium-term actions.
In addition, the importance of design choices cannot be overstated. By designing with sustainability in mind from the start and prioritizing circular practices, such as reuse and recycling, it is possible to create structures that are low emission and also easier and less costly to maintain over time.

Finally, it is imperative that project owners work across the entire value chain to foster green building practices. Supplier framework agreements can provide a volume guarantee for more sustainable materials, while sustainability requirements in requests for proposal (RFPs) and contractors’ agreements can drive the demand for low-carbon building practices. There are two broad approaches to promoting sustainability in contracting: outcome-focused and prescriptive. The choice of approach depends on the operating model and stage of construction, but both require integration with “standard” RFPs. (See Exhibit 3.)
In the outcome-focused approach, the developer spells out the objectives and expected outcomes in the design or construction RFP. The developer might also modify technical evaluation criteria to include sustainability credentials and performance criteria. In this approach, suppliers and/or internal designers have the flexibility to find solutions to meet these objectives—such as which low-carbon materials to use.
Subscribe to our Climate Change and Sustainability E-Alert.
In a prescriptive approach, the developer issues an RFP to potential suppliers that specifies sustainability targets and specific low-carbon materials or technologies to be used. Any supplier’s proposed plan undergoes a technical evaluation to ensure it adheres to these targets and directives. The strength of this approach is that it establishes clear directions for sustainability, but some suppliers might object because the approach is less flexible than the outcome-focused approach and permits less creative problem solving.
An outcome-focused approach is most appropriate for designers, developers, and contractors so they can creatively use their know-how—whereas the prescriptive approach is preferable when a detailed design is completed and contractors need to execute the work exactly as stated in the RFP. Also, the approach might differ depending on the operating model. If the company is pursuing self-development, then taking an outcome-focused approach to design makes sense. But if a company is using a third-party developer, combining an outcome and prescriptive approach to design might be necessary to avoid the loss of control.
The Middle East is undergoing momentous change. Regional governments are committed to diversifying economies away from oil, many ambitious mega-projects are in the works, and a young, environmentally conscious population is entering the workforce. For these reasons, the region has a unique opportunity to spearhead sustainable development—an opportunity it should seize not only to reduce the footprint of its very ambitious projects but also to become leaders in technologically advanced solutions. Governments, developers, and the entire real estate ecosystem should keep their eye on the prize, incorporating sustainable development principles within their overarching strategies early on, highlighting clear targets, and laying out actionable implementation roadmaps. At such a pivotal moment, this approach is not just the right thing to do for the environment, it’s also the best way to guarantee the project’s long-term value.