As the fully electric vehicle (EV) continues to make inroads with consumers, heading towards a projected 40% of global car sales by 2030, securing sufficient battery materials—especially for the cathode of Lithium-Ion (Li-Ion) batteries—is taking on increased urgency. For battery manufacturers and automotive OEMs, potential supply chain disruptions and price volatility that reduce the availability of these materials or make them overly expensive are worrisome roadblocks to a fast expansion in EV battery production. Moreover, the carbon footprint of EV batteries is a concern for environmentally conscious potential buyers, which could also negatively impact EV uptake.
Faced with these uncertainties, automotive and battery companies are increasingly pinning their hopes on the emergence of EV battery recycling as a solution. Under this approach, recyclers recover a large share of the materials in aged-out EV batteries or from manufacturing scrap—and this reclaimed “secondary” content is then used in new batteries. From an economic perspective, this is a compelling idea if undertaken at scale.
Today, only China has a recycling industry large enough to harness these cost advantages, whereas in the EU and the US, the industry is still in the build-up phase. However, by varying degrees policymakers are pressuring the EV sector to ensure that batteries are designed for circularity, that new batteries contain recycled content, and that recyclers recover larger shares of materials. (See “Global EV Battery Recycling Regulations.”)
Global EV Battery Recycling Regulations
European Union
The EU Battery Regulation adopted in July 2023 is an ambitious set of rules that covers the entire battery life cycle. Among the key components:
- Transparency on a battery’s content, design, and recyclability through a virtual, unique Battery Passport (required for all EV and industrial batteries greater than 2 kWh on the EU market as of February 2027).
- Recycling targets by the end of 2027 of 50% for lithium, 90% for cobalt, and 90% for nickel. Percentages increase at the end of 2031.
- Recycled material targets for new batteries by August 2031 of 6% for lithium, 16% for cobalt, and 6% for nickel. Percentages increase in August 2036.
China
Since 2018, China’s Ministry of Industry and Information Technology has placed the responsibility to establish a recycling system for end-of-life batteries on electric vehicle manufacturers through its “Provisional Measures for the Management of Recycling & Utilization of Power Batteries for Electric Vehicles.” Through subsequent financial and fiscal policies, China, which leads the world in the production and ownership of EVs, has continued to encourage the development of a network of collection outlets and recycling plants to handle an anticipated barrage of depleted batteries in the coming years. Official government guidance for recovery targets is generally higher than in the EU, with 98% recovery rates for cobalt and nickel and 85% for lithium.
United States
The US has no regulations to manage Lithium-Ion battery recycling. However, the 2022 Inflation Reduction Act contains domestic sourcing requirements for battery materials, encouraging recycling to limit the need to import materials. In addition, the IRA, the Investment Infrastructure and Jobs Act of 2021, and the Loan Programs Office are providing financial support for qualified battery recycling projects.
Recycling is just one circularity option. Battery repair and re-use in electric vehicles—or giving them a second life in a related application, such as stationary energy storage—are other possibilities. But the economics of these alternatives are not favorable, especially for batteries that are dominant today, which are high in nickel and cobalt. We believe that technological improvements and economies of scale will continue to favor recycling as the preferred circularity strategy.
In this article, we provide a window into the landscape, profit pools, value chain, risks, and uncertainties for companies in the EV battery ecosystem—including mining businesses, battery (cell) manufacturers, automotive OEMs, and recyclers. Our message is clear: for all of these companies, this is a period of significant opportunity to take advantage of a growing market and attractive profit pools.
EV Battery Recycling Is on the Rise
Globally, EV battery recycling capacity is expanding. Battery cell manufacturers are building recycling facilities on-site or close-to-site. Independent recyclers are starting to invest in their own Li-Ion battery recycling plants. Over the past two years alone, more than 20 companies in the automotive and recycling sectors have announced plans for new partnerships.
The overall capacity of EV battery recycling is difficult to assess because details about the size and scope of new recycling facilities are often incomplete. However, our best estimate is that China now has the capacity to recycle over half a million metric tons per year. The US and Europe trail, with about 200,000 metric tons of annual recycling capacity each. The EU hopes to double that by 2025.
Of course, with few electric vehicles currently on the road and almost all of them relatively new, EV battery recycling is not as necessary now as it will be in the next decade. Demand for cathode materials is expected to more than double between 2025 and 2030 due to a steep increase in EV sales, while batteries generally are not retired until after 10 years of use or more. Thus, most of the material available for recycling will be production scrap until 2035. The share of available secondary material compared to overall cathode material demand will be low throughout the decade (about 16% by 2035). (See Exhibit 1.) Beyond 2035, substantial volumes of post-consumer scrap (from retired EV batteries) will overtake production scrap as the most important source of secondary material.
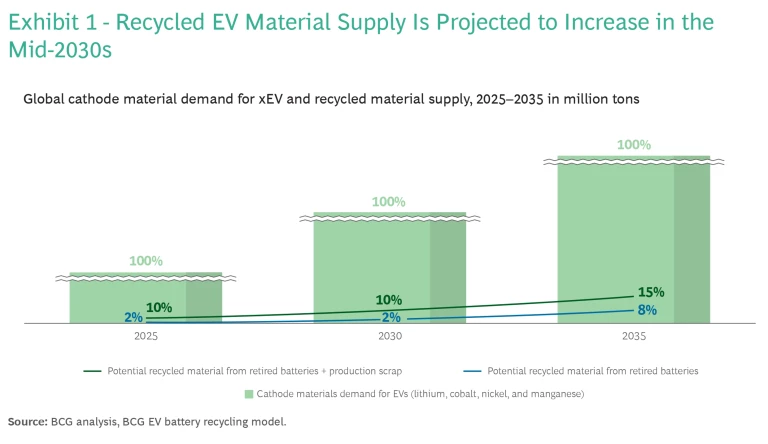
Given this timeline, in the EU scrap from retired EV batteries alone will likely be insufficient to meet the regulatory quotas for lithium and nickel established in 2023. (See Exhibit 2.) Only cobalt might have ample post-consumer volumes if EV battery cell manufacturers can tap into recycled cobalt from batteries in consumer electronic products. With these looming shortfalls, EU authorities are allowing production scrap to be counted towards meeting recycled content quotas.
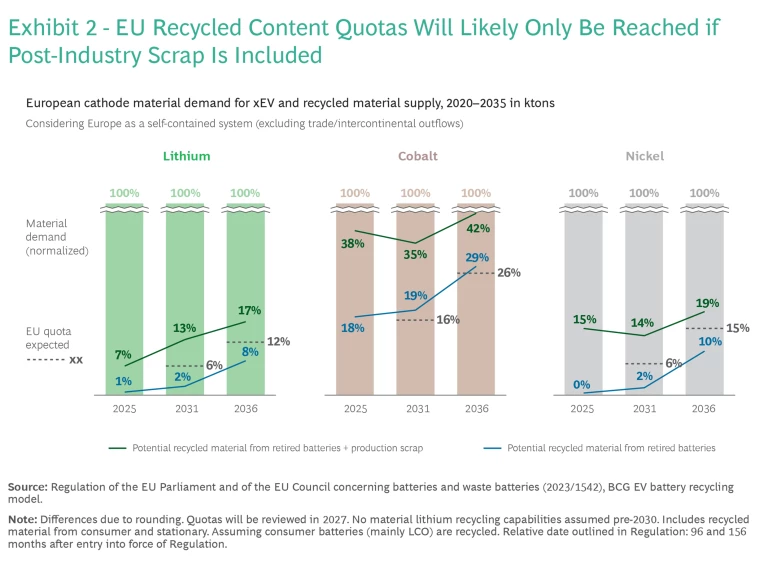
Attractive Profit Pools Exist Along the Value Chain
The recycling value chain for end-of-life EV batteries can be broken down into four steps: (1) battery collection, logistics, and sorting; (2) battery discharge and dismantling; (3) pretreatment with battery shredding and black mass production; and (4) battery materials recovery with chemical processes. The last step, which includes refining and possibly blending with primary materials to deliver attractive volumes of battery grade content, is critical to closing the circularity loop. It includes both pyrometallurgy (a thermal-based extraction and purification process) and hydrometallurgy (using aqueous chemistry for extraction and purification)—or only hydrometallurgy. Pyrometallurgy is the more robust technology, but it recovers fewer recycled materials, leading to different economics.
Overall, profit potential is highest in the battery materials recovery stage, due to the possible upside in the price of these recycled materials when sold to battery manufacturers as well as higher margins resulting from significant scale. (See Exhibit 3.) Nevertheless, this stage also has the steepest entry barriers due to significant capex requirements and the expert knowledge necessary to specialize in this work. By contrast, activities earlier in the value chain have a smaller margin potential, but they also have a lower commodity price risk and require fewer skills.
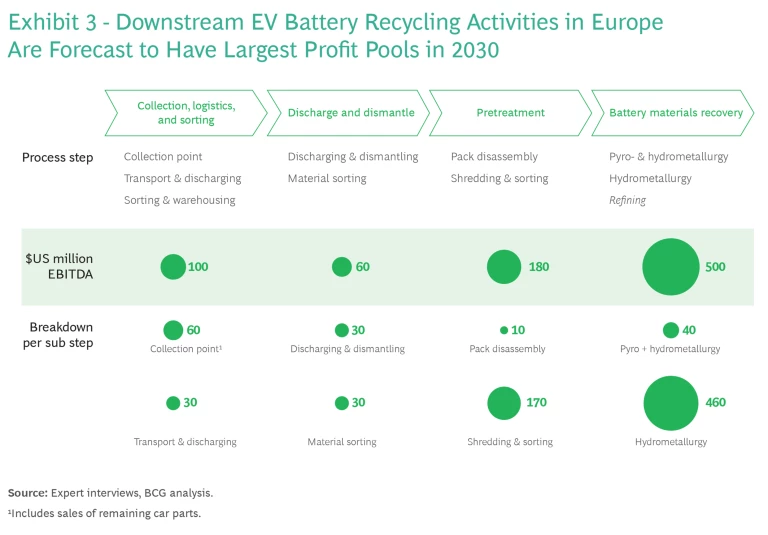
Value-chain activities with low barriers to entry, such as shredding, already face overcapacity in part due to a lack of scrap for recycling. This in turn lowers margins and is not very attractive to ambitious players, who will focus more on the tail end of the value chain. Hence, traditional recycling players are advised to compete for a piece of the overall materials recovery profit pool and not just the front end.
Heterogeneous Archetypes Form Recycling Ecosystems
Across the four steps in battery recycling, companies can choose among different stages as an entry place into the market. (See Exhibit 4.) Each offers various profit pools and requires specific skill sets. The decision of which archetypical value play to engage in and how to position a company along the value chain will depend on (1) the current business model and existing know-how, and (2) future goals and expected strategic gains from recycling.
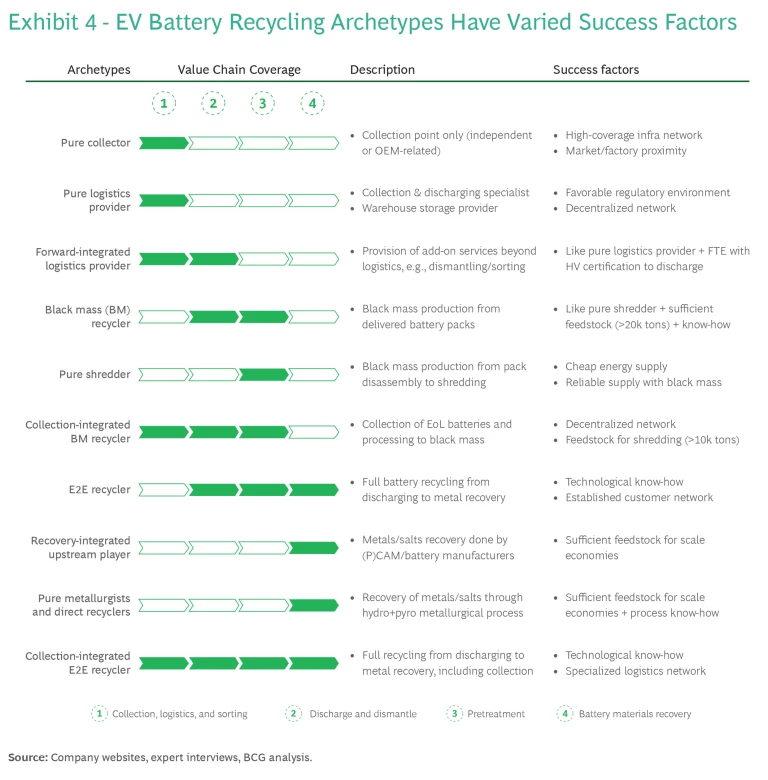
The current long list of archetypes arises from companies trying to establish a foothold in niches of the battery recycling market where they best fit depending on their capabilities. For instance, a forward-integrated logistics provider would both collect old batteries as well as dismantle them in preparation for shredding. Given the nascent state of the EV battery recycling sector, we expect this heterogeneity will not disappear any time soon.
With so many different types of activities along the value chain, success will be tied to the ability of companies to forge closed-loop ecosystems. For instance, given that the recycling market is currently supply-constrained with a high demand for black mass (essentially, crushed battery chemicals), a shredder or an upstream refiner needs to be closely integrated into an ecosystem that can secure feedstock supply and ensure a reliable customer base to sell their products. Technology alone will not be able to create competitive advantage if these supplier and customer relationships are lacking.
The key to success for smaller players lies in integrating their capabilities into functioning ecosystems that often will be formed around large OEMs and battery cell manufacturers. These large companies—or sometimes other sizeable businesses in the value chain—may also act as orchestrators among the ecosystem members to reduce friction, increase efficiency, and enable higher recovery rates.
Watch for Key Uncertainties
As companies consider their place in the EV battery recycling sector, it is important to be mindful of the challenges and uncertainties that must be addressed and overcome. Four primary risks stand out.
Evolution of cell technologies
A shift in cell technologies could threaten the economic viability of investments in recycling activities related to older battery types. For example, while shredders can be used for a variety of cathode technologies, Nickel Manganese Cobalt (NMC) and Lithium Iron Phosphate (LFP) batteries, two of the most commonly used Lithium-Ion chemistries, require separate recycling techniques and facilities at the back end of the value chain. The evolution of cathode chemistries could even make existing and anticipated government regulations difficult to achieve. Some rules mandate materials recovery rates based on battery weight. However, those rates may not be attainable by recycling Sodium-Ion batteries, which are just beginning to surface but are heavier and have fewer valuable materials than Lithium-Ion cells.
Regulatory risks
Legal and political changes affecting the ability to either purchase, transport, or sell waste batteries and intermediate products, such as black mass, could change the contours of the industry. Also, regulation plays a vital role in shaping the vehicle export business. Excessive export activity for second-hand or end-of-life vehicles leads to reduced availability for local recycling and decreased feedstock.
Advances in battery recycling technologies and processes
The evolution of new recycling technologies could harm recyclers that have adopted older methodologies. For instance, a process known as direct recycling can recover pCAM (precursor cathode active materials) or CAM (cathode active materials)—the starting points for cathode manufacturing—at a lower cost than traditional recycling techniques. This technology may have its biggest impact on recycling certain forms of Lithium Iron Phosphate batteries and could cannibalize profits of traditional metallurgists, compelling them to reconfigure their processes at a possible substantial cost. In addition, the Chinese export restriction on graphite might pressure other nations to scale-up their recycling efforts in order to recover it.
Volatility of commodity prices
The value of raw materials recovered from recycled batteries can vary significantly with market demand and supply, which presents a dual challenge and opportunity. Financial attractiveness in the case of high material prices can be reverted if prices drop, making it difficult to predict and plan for consistent returns in such a dynamic market environment.
The Time for Action Is Now
Despite the challenges, the recycling market is a sizable opportunity for a broad range of companies. Uncertainties can be mitigated by forming intelligent partnerships to access battery feedstock and recycling technologies—and by making informed decisions about the best returns for the future based on a company’s current strategic thrust. Ignoring this can mean missing out on a lucrative evolving market.
For OEMs, creating sustainable, circular supply chains by engaging in recycling partnerships is imperative. It not only aligns with global regulatory shifts but also is essential for a competitive edge honed from supply security and cost-efficiency. By forging partnerships with seasoned recyclers, OEMs can ensure a steady supply of critical raw materials through the recovery of valuable components from end-of-life batteries, mitigating the risks associated with raw material price volatility and supply disruptions. Moreover, engaging in recycling operations—either independently or through collaborations—positions OEMs favorably in the market as responsible and forward-thinking players.
For traditional recyclers, EV battery circularity opens new avenues of business and innovation through collaboration with automotive and battery manufacturers. This also positions traditional recyclers as leaders in promoting sustainable practices, providing access to new markets, partnerships, and revenue streams. By actively engaging in dialogue with stakeholders, advocating for supportive regulatory frameworks, and participating in industry collaborations, traditional recyclers can become the key enablers of a circular economy for batteries and EVs.
Embracing the recycling wave for these companies—as well as for aftermarket players, battery cell suppliers, and adjacent businesses—is not an option but a strategic imperative to stay ahead in an industry that is undergoing a transformation. Proactive steps today are the cornerstone for a sustainable, profitable, and resilient business model in the automotive industry’s electrified future.
The authors wish to thank Berit Leinhaeuser, Diana Stimmler-Caesmann, and Adrian Brandenburg for their research and analytical support in putting this report together. Also, we would like to share our appreciation for the many automotive and recycling executives that agreed to be interviewed for this report. Their significant insight greatly informed our thinking on this topic.