Imagine a manufacturing workforce empowered by data, digital tools, and advanced analytics: operators employ data-driven technologies to evaluate productivity losses in detail, optimize corrective measures, and seamlessly communicate across teams. At the same time, they leverage AI's predictive and prescriptive capabilities to improve safety, quality, and reliability. These enhancements reduce waste, promote productivity gains, and support the sustainment of lean practices.
Despite all the clear benefits that digital and AI can deliver on the shop floor, most manufacturers are not realizing the full potential of this opportunity. A BCG global survey of almost 1,800 manufacturing executives across seven industries found that 89% of companies plan to implement AI in their production networks and 68% have already started implementing AI solutions. Yet only 16% of companies have achieved their AI-related targets. Nearly all companies said they face challenges in scaling their AI solutions.
To realize value from digital and AI integration at scale, companies will need to focus sharply on people and processes—even more than they do on technology and algorithms. Manufacturers need to define their vision, build capabilities, and orchestrate the activities of multiple stakeholders. They must support these efforts with the right data infrastructure and governance, as well as establish the prerequisites for scaling technology across the production network.
Build the Transformation on Lean
Lean principles are the foundation of modern manufacturing practices. Best-in-class lean production systems enhance safety, quality, employee engagement, and delivery performance. They also boost overall productivity by building frontline workers’ capabilities to understand and eliminate efficiency losses.
Traditional lean approaches fall short when stacked against the ever-increasing number of machines and control systems that require a much stronger technical understanding of equipment.
Traditional lean approaches fall short, however, when stacked against the ever-increasing number of machines and control systems that require a much stronger technical understanding of equipment. At the same time, the workforce is changing. New generations of workers are accustomed to real-time digital interfaces. The paper-and-pencil approach of many lean practices is decidedly less engaging, and lack of engagement jeopardizes the sustainability and quality of lean systems. Moreover, as seasoned operators and leaders who possess technical knowledge move into retirement, manufacturers lose their uncodified expertise. Such losses undermine the standardization that lean systems rely on.
By incorporating digital tools and AI, companies can ensure that lean manufacturing remains effective. (See Exhibit 1.) Digital tools provide increasingly critical data for solving issues or informing decision making in plants. Embedding advanced analytics into processes supports efforts to identify inefficiencies, predict trends, and tailor action plans and strategies to meet specific conditions.
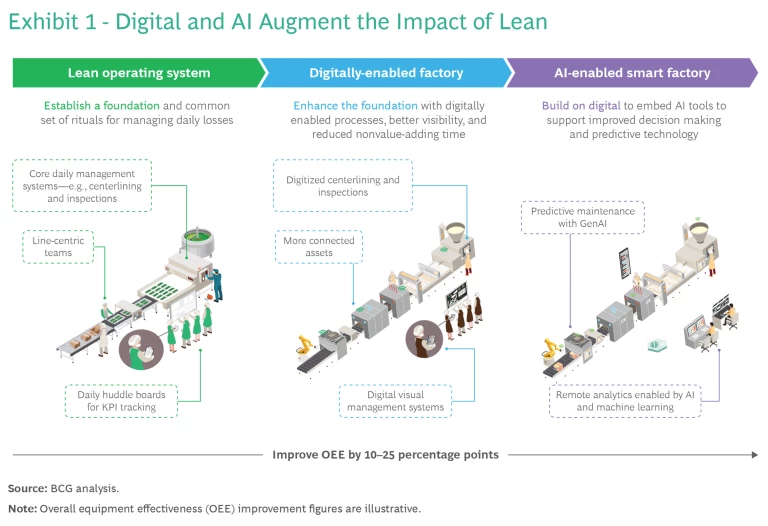
Don’t Let Technology Define Your Strategy
Many manufacturers have taken a “let many flowers bloom” approach to technology deployments—investing in an array of off-the-shelf point solutions from various vendors. This approach forces operators to utilize a wide variety of poorly integrated solutions that may have overlapping functionality and confusing user interfaces.
In many cases, the solution developers lack firsthand knowledge of shop-floor operations, leading to technology that is misaligned with actual ways of working or conflicts with established lean practices. In addition, manufacturers face the challenge of integrating the different solutions and their separate collections of distinct underlying data to build a cohesive platform for applying advanced analytics.
To capture the potential of technology deployments, a manufacturer should start by developing a clear vision of its factory of the future.
To capture the potential of technology deployments, a manufacturer should start by developing a clear vision of its factory of the future. This includes defining standard processes and rituals and fully integrating these into a technology stack that supports them. To realize their promise, digital and AI need to drive efficiency and information in ways that promote each manufacturer’s distinctive vision.
Across applications, the improvements to cost, productivity, quality, and customer service can be significant. There are also nonfinancial benefits, including enhancements to safety, engagement, and customer satisfaction. (See Exhibit 2.)
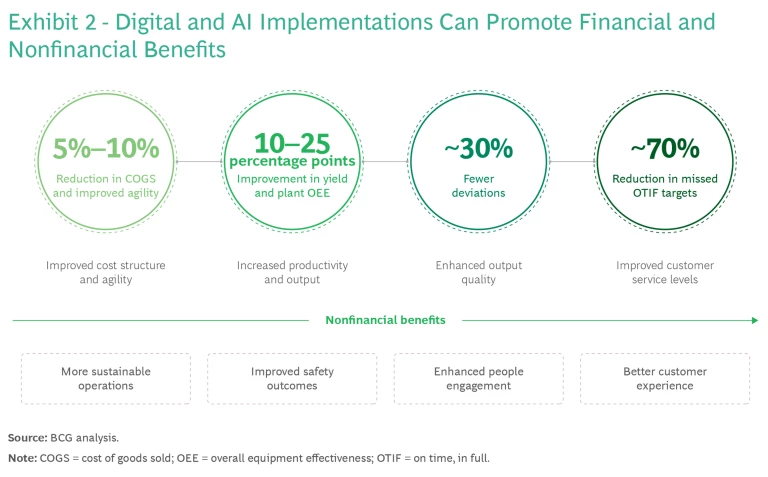
Digital and AI Enhancement in Action
Equipment maintenance offers a prime example of how companies can enhance lean practices by leveraging digital and AI technologies. Traditional maintenance planning and scheduling focuses on replacing costly unplanned repair jobs with well-planned preventative work. However, in order to schedule work, users must stitch together data from a patchwork of enterprise resource planning systems, spreadsheets, and third-party vendor solutions. By integrating digital and AI, manufacturers can incrementally evolve their capabilities in the following ways:
- Digitized Monitoring, Planning, and Alerts. Sensors provide real-time data that is fed into a centralized data repository. Trend analysis and data visualizations help to optimize maintenance planning. Any deviations relative to defined criteria trigger automated alerts for proactive interventions.
- Algorithm-Enabled Predictive Maintenance. Algorithms are trained to analyze real-time machine performance and predict failures before they occur. By servicing systems before they fail, operators improve uptime.
- Generative AI Copilots That Support Execution. GenAI copilots suggest repair strategies instantaneously, including parts and availability information—accelerating the execution process from hours to minutes.
When implemented correctly, the integration of lean, digital, and AI creates a reinforcing virtuous cycle. For instance, Exhibit 3 illustrates how the use of digitized issue identification and resolution and AI-enabled predictive maintenance augments inspection routines by equipment operators.
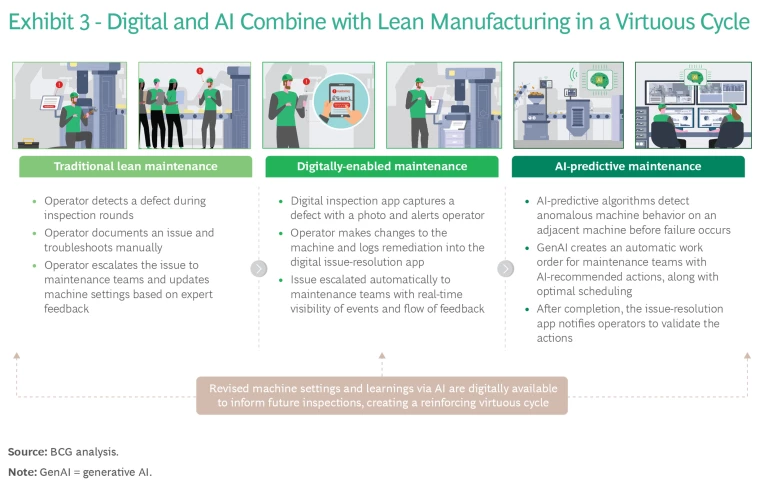
Unlocking the Value at Scale
Integrating lean, digital, and AI at scale is not an easy journey. Depending on the starting point and culture, manufacturers will face challenges. These include change resistance, gaps in digital literacy, and the inherent complexities of integrating new technologies.
This makes redefining the interaction between humans and technology essential. To unlock the full potential, our implementation strategy focuses on the 70/20/10 rule: dedicate 70% of the effort to people and business transformation, 20% to the data and technology backbone, and 10% to algorithms.
Our implementation strategy focuses on the 70/20/10 rule: dedicate 70% of the effort to people and business transformation, 20% to the data and technology backbone, and 10% to algorithms.
To achieve value at scale, companies need to address several topics at the start of the journey:
Vision. Define a clear, user-centric vision of the future factory, underpinned by the foundational lean principles required to deliver business impact. Determine the digital and AI use cases that reinforce and support that vision. Avoid the trap of taking a technology-first approach to investments. Identify the organizational capabilities required to advance in stages from the current state to the envisioned future state.
Talent. Upskill existing talent on the shop floor to leverage digital and AI. Identify or train champions in the manufacturing organization to accelerate digital and AI adoption. This includes designating digitally savvy operators or engineers to serve as liaisons between software users and technology developers. These “product owners” translate user requirements into specifications for developers, ensuring alignment between technical capabilities and shop-floor processes.
Orchestration. Align the activities of business and technology leaders, third parties, and deployment teams, so that initiatives are clearly prioritized and roadblocks identified. Target leadership interventions to promote progress.
Data Architecture and Infrastructure. Consider investments required to support the long-term vision, providing sufficient and reliable data and integrated systems as your technological sophistication increases over time. For example, create an infrastructure to ingest and store the data needed to train AI algorithms.
Data Governance. Develop any needed capabilities to promote the security, accuracy, and availability of the data generated by digital systems.
Scalability. Ensure that data and infrastructure are consistently available, structured, and clean across the production network. Determine the loss profile and local technical capabilities at all sites and address any deficits identified.
A best-in-class lean production system provides the basis for deploying data-driven digital tools and AI on the shop floor.
A best-in-class lean production system provides the basis for deploying data-driven digital tools and AI on the shop floor—and potentially reaping double-digit improvements in cost, productivity, quality, and customer service. To capture these benefits, manufacturers must establish a clear vision for their factory of the future, implement disciplined lean processes, and ensure that their technology solutions support these processes. Manufacturers that succeed will achieve higher levels of efficiency and effectiveness and keep pace with the ever-accelerating changes in the business landscape.